By Jon Kestner, Product Manager, Swagelok Company
One of the trickiest elements to get right within a sampling system design is the back-pressure regulator. Unlike pressure-reducing regulators, back-pressure regulators control inlet pressure and are usually installed on the end of a line; pressure-reducing regulators are found at the beginning of the line and control outlet pressure. These two regulators work in harmony to balance out forces resulting from system pressure created when establishing the set pressure.
Importantly, these two devices should not be confused, nor should their importance be overlooked during initial sampling system design. Yet, some common errors involving the relationship between back-pressure regulators and pressure-reducing regulators are still found in systems everywhere. This article will walk through the proper setup and installation for a back-pressure regulator to help optimize performance and ensure reliable, repeatable sample accuracy.

Image © 2013 “Industrial Sampling Systems”
Common Setup and Configuration Errors
Figure 1 demonstrates a typical back-pressure regulator setup for an analytical sampling system. In this setup, the regulator’s job is to divert excess flow not being used by the analyzer (A) into a bypass vent, helping to maintain pressure. The flow restrictors (shown as R1 and R2) then enable the regulator to properly manage pressure. When the source pressure changes, the regulator responds by altering the amount of diverted flow, helping to maintain balanced, constant pressure at the regulator inlet and through the analyzer.
To accomplish this, the back-pressure regulator requires some form of flow restriction – most commonly a needle valve. Lacking that restriction, the backpressure regulator will not be able to control upstream pressure effectively.
Because it plays such an important role in maintaining constant pressure to the analyzer, omitting a restriction like a needle valve is one of the most common, most consequential mistakes that can occur during the design stage. Many engineers assume the back-pressure regulator will itself be enough to control upstream pressure, but that is not true in most instances. Without a restriction, when system flow changes, the back-pressure regulator would continue to divert processing fluid in an attempt to increase flow through the bypass and control upstream pressure. However, because systems are generally very large compared to their sampling systems, there would be little change in pressure, which would result in the regulator being left wide open.
Conversely, another common mistake involves allowing too much flow through the restrictor (as shown by R2 in Figure 1). This can cause the regulator’s inlet pressure to drop below set pressure, which can in turn cause the regulator to shut completely and restrict vent flow. Designers should size the upstream flow restrictor (R1) appropriately, allowing some flow to go through the regulator even when flow is at its maximum to the analyzer.
To eliminate the potential for these errors, follow these steps (correlating with Figure 1):
1. Close R2, adjusting R1 to sufficiently allow bypass flow for your target analysis response time.
2. Next, fine-tune R2 for the analyzer flow desired. The bypass flow should automatically drop by the same amount.
3. If necessary, next open R1 slowly until the bypass flow is at least as fast as the analyzer vent flow. This enables the regulator to control inlet pressure if and when the source pressure changes.
4. If the source pressure is expected to change significantly, adjust R1 to generate a small amount of bypass flow at the lowest anticipated source pressure.

Image © 2013 “Industrial Sampling Systems”
Regulators in Competition
Figure 2 demonstrates one of the most common design errors that can negatively influence analyzer accuracy: placing a back-pressure regulator immediately following a pressure-reducing regulator.
The reason this setup does not work is because both regulators will be competing to control pressure, and only one can do so. To understand why, it is helpful to consider two alternating scenarios:
Scenario #1
The back-pressure regulator will stay closed if its set point is higher than the pressure coming into it from the upstream pressure-reducing regulator. This is due to insufficient force to lift the back-pressure regulator’s poppet from the seat, thereby allowing flow through the back-pressure regulator. Since the back-pressure regulator is closed here, it is unable to divert flow into a bypass channel. Without that diversion, excess flow and pressure will therefore be transferred to the analyzer, influencing its accuracy.

Image © 2013 “Industrial Sampling Systems”
Scenario #2
Here, consider a lower set point for the back-pressure regulator. In this scenario, with the flow now increasing, pressure from the pressure-reducing regulator will decrease at the rate of the upstream regulator’s droop curve. The increasing flow rate will push the back-pressure regulator up its accumulation curve and will dramatically increase its inlet pressure.
A few things can happen as a result of this action. First, if the set points for both regulators are close, the flow rate will rise until the droop pressure out of the first regulator matches the accumulation point of the second. Typically, the result is a very high flow rate. However, if the set points for the regulators are further apart, the flow rate will rise until one of the regulators eventually relinquishes its control. In effect, this results in one of the regulators controlling pressure while the other acts as a flow restrictor.
In either case, the bypass flow rate will be impacted, and largely depends on the difference between the two regulators. As shown in Figure 3, flow rate will continue to increase until both regulators attempt to hold an intermediate pressure between their set points, and the results here may be uncertain.
Despite the issues that can stem from the above scenarios, two regulators can function properly when set in a series if the application demands it. This requires a flow restrictor installed between the regulators. As shown in Figure 4, under the correct settings pressure remains constant at each end of the two restrictors. This pressure consistency ensures the flow is steady and helps protect the analyzer from variations in source and vent pressure.
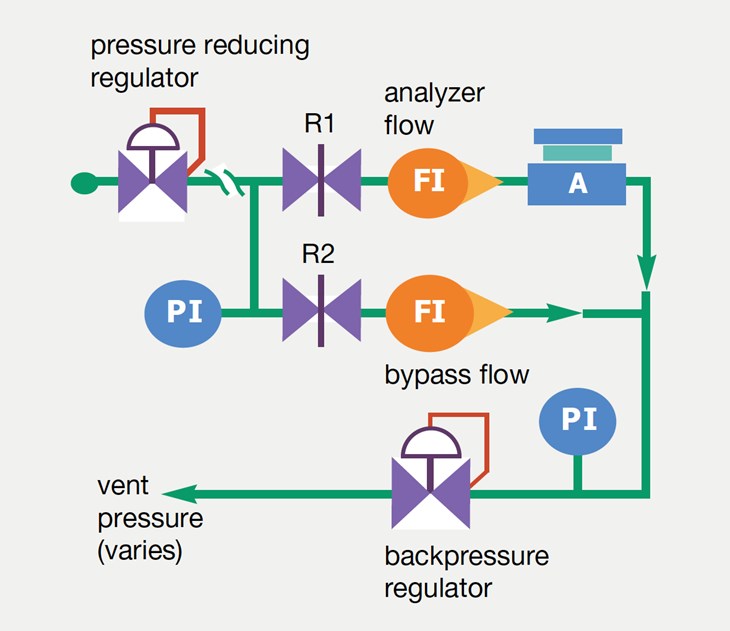
Image © 2013 “Industrial Sampling Systems”
An Optimized System
Proper back-pressure regulator functionality is critical for accurate sampling, and most commonly, a malfunctioning regulator is due to improper system design. For that reason, design engineers and technicians should follow the important best design practices discussed in this article to promote proper back-pressure regulator functionality – and therefore, more accurate sampling.
For more information, please visit: www.swagelok.com/en/blog/back-pressure-regulator-set-up-sampling-system-engineers