The market for valves for ammonia applications is growing at double-digit rates due to various environmental drivers. This market is particularly susceptible to political developments and there are more than 1,000 market niches where the facts and factors differ enough that the same value proposition cannot apply.
By Bob McIlvaine, President & Founder – The McIlvaine Company
Power plants use ammonia transported in three different phases. This makes treating ammonia as one market a mistake. Ideally, the facts and factors which create a unique value proposition in each niche should be analyzed.
Furthermore, the only way to adjust forecasts is in the niches impacted by the new development. This entails the best of equals: the best analysis of facts and factors = the best forecasts = the best value proposition = the best validation = lowest total cost of ownership. Currently, the world ammonia production is under 200 million tons per year.
Examining the Factors
China produces approximately 40% of ammonia worldwide capacity, followed by Russia with 9%, India with 7.5%, and the U.S. with 7%.
The future of the market is driven by the net zero CO2 initiatives. Billions of tons of fossil fuels are now consumed by power companies. This impact will reflect significantly on the market if a small fraction switches to ammonia. Many factors determine whether the use of ammonia will be measured in thousands or millions of tons.

Ammonia can be transported more cost effectively than hydrogen. For example, Yara has a contract with Japanese utilities to supply them with ammonia shipped from Australia. Given this distance, shipping costs are significantly high.
Ammonia is one of the best known and most widely used refrigerants in use today for ice plants, food lockers, cold storage warehouses, and other industrial cooling processes. It has a higher refrigerating effect per unit of liquid volume than any other type of commonly used refrigerant.
Other advantages are low initial cost, low pipe friction losses, zero ozone depletion potential (ODP) and zero global warming potential (GWP). With the recent trend of environmental awareness in the refrigeration industry, natural refrigerants like ammonia are even more desirable.
Ammonia does not emit CO2 when burned, and is therefore expected to become a next-generation fuel, as it contains properties ideally suited for the hydrogen economy. Ammonia does not require cooling and has a higher energy density than liquid hydrogen, making it more efficient to transport and store. Furthermore, producing ammonia with renewable energy results in zero or minimal greenhouse gas emissions.
For example, The Yuri project includes a 10 MW electrolyzer, 18 MW of solar PV, and battery storage. Once completed, the project will be one of Australia’s largest electrolyzers, capable of producing up to 640 tonnes of green hydrogen each year.
Yuri Operations will build the renewable hydrogen facility and supply the green hydrogen to Yara Clean Ammonia. The renewable hydrogen production is scheduled to be supplied to the ammonia plant in 2024.
Ammonia is transported in three phases, gaseous (anhydrous), aqueous, or as urea, converted to ammonia at the site of use. For the reduction of NOx at power plants, all three phases are being applied. Anhydrous is the least expensive, and aqueous is relatively safe, however it is more expensive. The on-site conversion of urea is popular for small applications where the safety requirements for anhydrous are challenging.
With all of these variables to consider, it is a big challenge for valve suppliers to determine how much ammonia will be used, where it will be used, and in what phase. Continuous analysis is needed to track the potential big changes in demand and location.

Valve Types
A number of different types of valves are used to transport ammonia. Most of the use is in industrial processes, but customers may also have use for valves in air pollution control, or other non-process applications.
The same customer may also need valves for water intakes, cooling, dosing, and wastewater treatment. The value proposition for a valve package can be more attractive than for a single application.
There are various valves present in the ammonia synthesis loop, controlling the flow of synthesis gas into the converter and ensuring proper recycling of the unreacted synthesis gas. Wide design options make valves suitable for all on-off/control applications in the ammonia synthesis loop. Triple offset design reduces wear and provides extended operational life in control and shut-off applications.
Due to the toxic nature of ammonia, all valve components must be constructed with appropriate materials. Carbon steel is suitable for anhydrous ammonia applications, however if moisture is present, stainless steel should be the choice material.
As can be seen in Figure 3, there are hundreds of different combinations of valve design and materials.


Many valve companies sell packages with both the valves and compressors or pumps and valves. It may be necessary to have a pressure relief device in any part of an ammonia pump and piping system that can be ‘valved’ off. This provides essential over-pressure protection, as cold liquid ammonia when isolated will expand as it warms up and exert pressures that could rupture the pump or piping unless relieved.
Additionally, return-to-tank pressure relief valves should be mounted on the discharge side of the pump. Internal type pressure relief valves should be mounted with the cap pointing towards the suction side of the pump.
Summary
The best strategy for pursuing the ammonia market is to analyze the facts and factors in each niche, and then create forecasts which reflect the value proposition which in turn is the obtainable market.
This is a challenging task involving thousands of factors. The use as a power plant fuel requires a different set of facts and factors than does the use for refrigeration. The NOx control niche alone is an annual revenue opportunity for valve suppliers of more than USD $50 million per year.
There are many valve selection factors including materials. All the factors need to be continually analyzed and the appropriate factors applied to determine not only the forecast and market plan, but to create a value proposition.
References:
1. Valve Facts, Factors, and Forecasts published by the
Mcilvaine Company
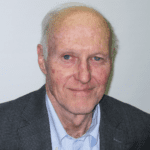