Valve World Americas had the opportunity to sit down with Deckard to talk about how he emerged into the EPC market and what kind of experiences he has gained since beginning his career in the sector. Through his varying roles in the industry, Deckard has learned what is required of a piping engineer, and aims to share that knowledge with engineers coming out of school.
By Brittani Schroeder and Sarah Bradley
An Interesting Beginning
Justin Deckard did not originally plan to be an expert in the piping realm. He went to Texas A&M University and obtained a degree in Ocean Engineering, with a specialization in Coastal Engineering, which included such things as beach water restorations and marina harbors. “Coming out with a degree like that, I had two choices: work for the army or work for the government in some other capacity. I did not want to do that,” Deckard relays. “I even had a job offer to work in Korea, but I wanted to stay closer to home.”
Deckard secured an interview at his first engineering company through a connection of a college roommate shortly after graduating. “He told me that I would not understand what they were doing, because they do not teach it in school, but he would look over my resume. The interview was very casual, but I thought I bombed it. Surprisingly, I had an email offer waiting for me the next morning,” says Deckard.
Deckard spent five years at Mustang Engineering, moved to Jacobs Engineering for four years, returned to Mustang Engineering (rebranded to Wood), and eventually found his place at Arion, where he is now the Piping Department Manager. Through all the companies he worked for, Deckard has gained a lot of experience from different projects. “I had the opportunity to work on refineries with really big, really hot pipes – everything from 72-inch cooling water lines to 1,200° heater lines. I have worked on many topside projects for a vast range of clients, so I have been exposed to a lot of different realms.”

A Day on the Job
When Justin Deckard started his career at Arion, he had the opportunity to build his department from the ground up. In Deckard’s opinion, it was a great situation to be in, rather than taking over a department from a past manager. While there were still a lot of challenges to overcome, there was also a lot of excitement.
Deckard manages piping engineering and design at Arion, and he and his team handle everything from 3D modeling, routing, drafting isometrics, piping classifications, to pipe and valve procurement, through to final delivery.
Deckard does not have a typical working day. “Every night before I head home, I make a plan for the next day of all the things I want to do. By 8 a.m. I have to re-evaluate the plan, and then it is re-evaluated after lunchtime. By the end of the day, I have maybe accomplished a few things that were on my original list,” Deckard admits. “Our team is bringing a lot of experience from past jobs to the company, and we are learning how to make processes better moving forward.” Deckard works with a team of 21 designers and three engineers, with a focus on the offshore and midstream sectors. “We are going to branch out into different areas soon, and I think we are able to do that because we have a strong, diverse, rollup-the-sleeves-and-get-dirty team.”
Deckard thoroughly enjoys working with his team of designers and engineers. “I like that I get to work with such a diverse group, and we are able to make clients successful. We are problem solvers, and when each person has a different background in the industry, we can cover a lot of ground,” he says.
Specialty Materials
In Deckard’s line of work, he sees many different materials being used for varying applications. When there is the requirement to work in different environments, it is crucial to consider what the best material is for the application, based on where it will be located. Deckard must ask questions such as, “Are we dealing with corrosion? If so, do we need to have more intricate corrosion-resistant alloys (CRA) present, whether that is nickel or stainless?”
Deckard enjoys being able to work with CRAs because of the complexities that come along with them. “CRAs come with a lot of nuances and intricacies, especially in the piping realm. We will have to work with materials such as clad Inconel alloy 625 or solid Incoloy 825,” Deckard states. It is crucial to consider what the most cost-efficient option is to produce these applications, versus how long the material will last, while also considering any delivery issues that may arise. Due to the difficulty in procuring the more ‘specialty’ alloys, delivery times can be extensive. Mills can take anywhere from 32 to 48 weeks to manufacture and deliver materials, depending on the size and quantity of the order.
In terms of commonly used materials, Deckard has seen the application of Inconel in crude projects because of its ability to withstand the fluid’s corrosiveness and the higher temperatures of the heaters. However, Inconel is not the only CRA used for the construction of heaters. “Normally you would see Alloy 800 HT, which is the heat-tempered version of Alloy 800 H, used to avoid cracking and creep issues. But in one particular case, the client wanted Alloy 800 H,” he explains. “The material came from a licensed provider, and we took the 800 H material through the heater to a place where we could then transition to chrome.” To achieve success, Deckard and the client had plenty of discussions on how to properly complete this transition. and ended up welding a 9 chrome flange to an 800 H pipe. While this was an uncommon situation, Deckard and the client experienced positive results.
When asked if Deckard chooses the materials for each application and project himself, he explains that it is typically the client who will choose. “They will bring us a list of what they will need, and we will work with their approved manufacturers list (AML) to procure the materials. If we somehow get ourselves into a pinch, we are able to deviate from the AML, to either get products quicker or for a lower cost,” he relays.

Various Equipment
Although pipes are his specialty, Deckard has experience with many more applications. “I have worked with valves, pumps and hoses, among many others, in my line of work,” he states. “Even though the instrumentation team works on all the fun valve projects and installing them, we do plenty of work with gate, globe, and check valves. Thankfully, we do not see many failures with these applications.”
Deckard has worked with every type of pump there is, including basic water pumps, crude pumps and transfer pumps. He explains that it is common to work with pumps regularly in the piping realm, and it is crucial that they ensure each pump is installed correctly and that they will operate reliably.
Another application Deckard has become familiar with, is hoses. His experience includes hose design, especially in terms of flex hoses and couplings. Typically, Deckard and his team design hoses that are 2 inches and smaller, which are used for water connections and offshore applications. “The neat thing about working with hoses offshore is that you are not only dealing with eroding from the inside, but also from the outside,” Deckard explains. “Salinity in the Gulf of Mexico is so high that corrosion issues are often experienced on the exterior of hose and piping systems.” For this reason, coatings are crucial.
Deckard’s experience with offshore applications used in the Gulf region has given him the understanding of why coatings are so important when it comes to corrosion prevention. “Coatings are significant here; once the equipment has been through a round of coating, the next round starts up right away to protect the equipment as much as possible. We are always working with clients to mitigate corrosion issues, whether that is talking about piping supports, considering the use of I-rods – which are a type of pipe support – or fiberglass pads,” Deckard relays. As problem solvers, Deckard and his team will strive the best solution for the client, as they want to eliminate the constant worry about corrosion.
Evaluating Fugitive Emissions
Deckard’s vast experience with various equipment and applications has allowed him to understand how serious the topic of fugitive emissions is. As the topic is continuing to become prominent worldwide, Deckard and his team have recently completed many dispersion analyses for emissions. A dispersion analysis looks at the effects when a flammable or toxic material releases into the atmosphere and the potential impact it can have. This can be due to a PSV, vent/thief hatch on a tank, or when the flare flames out. “We need to make sure everything is still ‘safe,’” he explains. As Deckard works with clients in the midstream region, he and his team are making sure their safety standards are up to date. “It is pretty interesting to see the dispersion clouds, and knowing where the safety guidelines and regulations are.” Deckard also expresses his appreciation that valve manufacturers and suppliers are all on board and certified to watch emission levels.

Digitalization
Digitalization and innovation are two things that Deckard is passionate about in his work. When he first entered the industry, Deckard recalls everything was paper-based. “You would get reams of paper in binders to go through, and almost every process was manual. What really excites me about Arion and my current role is that we are really pushing innovation,” says Deckard. One of the goals for Deckard’s discipline is to go completely paperless. There are many manual tasks that Deckard hopes to automate in the near future. He also hopes to incorporate a database-driven design where all information is held in a central location and then pushed to other locations that will require it. As opposed to relying on and managing paper files in several locations, it can all be managed in one place, and could also cut down the cost of business drastically for every party that needs access to the data.
A task that Deckard has taken on is digitizing all the information stored in binders by the experienced engineers. “As these people will start retiring, I am obtaining their old binders of reference material and slowly, but surely, I am inputting all that information in our digital system. I may need some help to get it all in there, but this is something I am really passionate about doing.”
Finding the Problem Solvers
In Deckard’s opinion, it takes a “special breed of person” to live the life of a piping engineer. “The piping world is very analytical and meticulous, with endless calculations. It is always about the details in our line of work, whether they are big or small,” he explains. For this reason, Deckard is always looking for problem-solvers, and he is not afraid to bring in new engineers straight out of school. Throughout his career, he has brought in upwards of 20 new graduates to work with him and his team. For Deckard, it is important to attract the new engineers during the early stages to determine if they will become invested in the work. “Sometimes, finding an engineer who is extremely meticulous in their work is as difficult as finding a unicorn – but once we find them, we will hold onto them forever,” says Deckard.
When he is training his new recruits, Deckard focuses on their problem-solving skills. “In the pipe stress realm, it is all about, ‘How do I solve fundamental problems?’ There are very simplistic concepts, but you need to be able to apply them in so many ways to different situations,” Deckard explains. “Sometimes the pipe does not have enough support, sometimes there is not enough space for the pipe, and you have to be the one to figure it out and find a solution. I love how easy it can be to solve a problem, but also how challenging it can be. It makes every day different.”
During the training process, Deckard also tries to incorporate the senior engineers and their vast experience. “We have engineers with 30 to 40 years of experience, below them there are engineers with maybe 10 to 12 years of experience, and then there are the new grads. There is such a large generation gap for engineers, and I am trying to bridge that gap any way I can,” Deckard admits. “In the past, during a downturn in the industry, we would lose our younger engineers, and the older, more experienced ones stay. That also contributes to the industry’s knowledge gap. Therefore, if I am able to bring together our experienced engineers and our new engineers to share knowledge before retirement, I will be a happy man.”
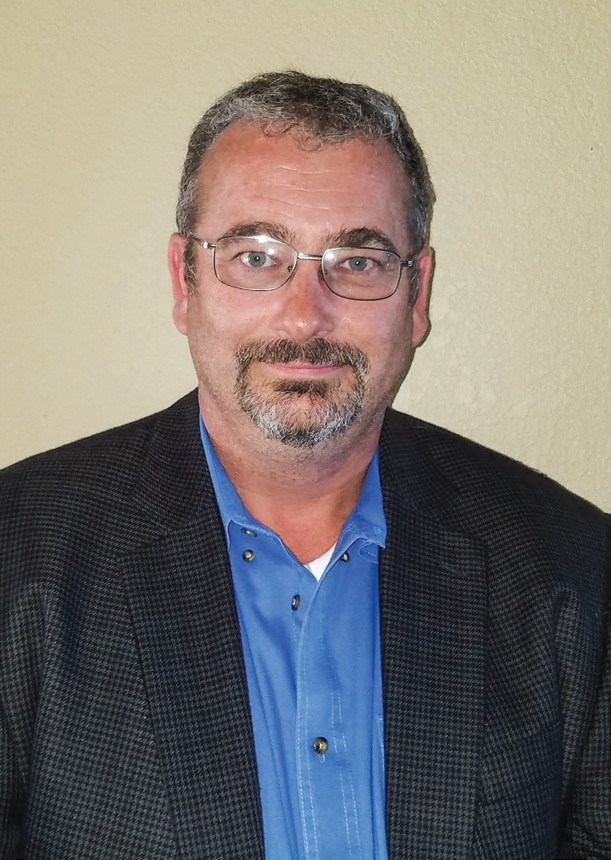
Advice for the Future
If Justin Deckard could give one piece of advice to young engineers, he would recommend staying dedicated to the craft they have chosen. It is important to put the time into the craft and become invested. In Deckard’s experience, it is very rare to see a new graduate with enough knowledge to be good at their job on the first day. “You have to be adaptable. I learned quickly that just because I want to do something does not mean that I get to do it every day.”
A big influence on Deckard’s career also came from his mentors. “I think it is really important to find one, or a few, good mentors. You need to latch on to them and suck all the knowledge out of them,” Deckard laughs. “There are mentors from my past that have retired, and I still call them up and talk about past projects and ask them why they chose the solution they did. I am not ready to lose all the knowledge that these engineers have, and I think it is very important for young engineers to be obtaining as much information as possible, before it is too late.”