Conducting cycling tests on a chamber that replicates seafloor conditions is just part of the qualification process of a valve design. In this article, we are going to explore what a subsea valve is and the effort it takes to make sure it will perform under sea.
By Davi Sampaio Correia – Technical Consultant
Subsea Production Systems
Industrial valves on land are connected to piping and used to control flow between equipment and vessels. Under the sea they perform the same function, but now they are part of a subsea production system. A subsea production system is an arrangement of dedicated components connected to permit extraction and flow of hydrocarbons from a reservoir to production facilities, which may be onshore or offshore. It typically consists of two groups of components (see Figure 1): lines and equipment. Lines are used for flow production or control. Some examples are flowlines, risers, umbilical, and production jumpers. Some examples of equipment are Subsea tree (commonly known as wet X-mas tree), manifolds, Pipeline End Manifold (PLEM), Pipeline End Termination (PLET), and Subsea Isolation Valve (SSIV).
All the equipment listed above has valves or is a valve itself. So, it is worth taking a better look at them. An X-mas tree is a valve package placed on top of the well, facilitating the interface between the well and the manifold. X-mas trees provide barriers and control the flow from the well. The manifold is a shared connection point for several wells, facilitating distribution of production flow and communication to a topside facility through flowlines and umbilicals [1].
A PLEM is a manifold without means of monitoring or control. It takes flow from several lines and converge it to one (or vice-versa). A PLET is an equipment normally used to connect a flowline to a riser. And the SSIV is a safety equipment comprised of a metallic structure with a valve inside, whose fail-safe position must be closed. The SSIV is installed between a riser and flowline, in order to prevent unintended release of hydrocarbons to the surface in case of line rupture or fire.
There is no international definition of drilling or production water depths, but a common one can be seen on Figure 2. Today, the Stones project in the Gulf of Mexico holds the record of deepest oil and gas production system, with a subsea system located 9,500 feet (2,896 meters) below surface.
As depth increases, so does water pressure. To give a glimpse of what water pressure can do, we can look at the tragic fate of the submarine ARA San Juan S-42. This vessel was once part of the Argentine navy and disappeared on 15 November 2017. The remains of the submarine were found on 16 November 2018, at a depth of 907 meters. It is believed the disaster was due to the submarine having reached its crush depth and imploded, at a water depth of about 500-600 meters. When a submarine malfunctions and sinks to forbidden depths, the increasing water pressure acts uniformly all over the hull. As soon as the buckling or safety structural thresholds have been crossed, implosion happens abruptly, within milliseconds, like a tin can being crushed [2]. Figure 3 shows the submarine docked and a simulation of the failure [2].

Design Challenges
As we have seen, subsea valves must perform at depths approaching 3,000 meters. That means keeping physical integrity, controlling the process fluid, not leaking it to the sea, and not permitting seawater to ingress into the valve. We must keep in mind that the valves – and the rest of subsea system for that matter – are laid on the ocean floor using very expensive and specific boats, operated by a very experienced crew. These vessels are few and scheduled to operate months in advance. So, in an emergency, you cannot just call them and expect help next week. This means that maintenance opportunities are limited – to say it mildly – and that the valve is expected to perform without any intervention for a period ranging from 20 to 30 years.
Materials selection for subsea valves is a bit more complicated than for surface valves. Surface valves tend to deal with one fluid, that does not vary much during the life of the valve. On the other hand, subsea valves may have to handle a variety of fluids: produced water, seawater, hydrocarbons (liquid and gas), and injection chemicals. That’s because fluids in a reservoir change as it becomes depleted. Also, there are failures or scheduled interventions that require chemicals intended for the well to go through the valve.
Another challenge for materials selection is corrosion. The problem here is twofold: not only the materials have to withstand the internal fluids, but also seawater. And for the latter, sometimes the cure is worse than the disease.
Hydrogen embrittlement can be defined as a delayed brittle failure of a metal component caused by trapped atomic hydrogen interacting with a susceptible metallurgy under stress. Certain alloys used in subsea systems, such as nickel alloy 718, are not corrosion resistant in seawater and may therefore be connected to a cathodic protection system. The problem is that such protection system will generate hydrogen on the protected component, which can cause hydrogen embrittlement and later failure [3].
Failures due to hydrogen embrittlement have led to the development of specifications addressing the problem for some the most common materials used in subsea systems. Examples of these specifications are API 20E and API 20F for carbon alloy steel bolting and corrosion resistant alloy bolting, respectively; DNV-RP-F-112 for duplex & super duplex stainless steels and finally API 6A718 (currently titled API 6ACRA) for nickel alloys [3].


Types of Subsea Valves
There are basically 3 groups of valves on a subsea system: on-off, choke and check. Check valves are valves that prevent backward flow of liquid or gas. Choke valves are control valves responsible for reducing pressure or restricting flow from a well. On-off valves are isolation valves, that is, they are designed to be left either totally open or totally closed. They have the highest percentage among the subsea valve population, and, for that reason, they will receive more coverage in this article.
There are two groups of isolation valves – ball and gate – each with two variations (see Figure 4). Ball valves can be either floating or trunnion and gate valves can be either slab or double expanding. No matter the group, they are all normally hydraulic actuated, with or without the possibility of ROV operation (ROV stands for remotely operated vehicle). Some companies also offer the possibility of electric actuation. This technology lacks the standards of the more traditional hydraulic option but offers a more environmentally friendly solution in a compact design.
For each valve type, a brief introduction can be found ahead:
Gate – this is the most common group. For the same diameter and pressure rating, they tend to require more space to be installed in the equipment. They also tend to be heavier. Because of this, sizes over 10 inches are rare. Although both gate and ball are equipped with metal to metal sealing, gate valves deal better fluids with a high percentage of sand or solid particles. Also common for both groups is the use of overlays with corrosion resistant alloys on seat pockets, stem passage and other critical sealing areas of the valve. Slab gate valve has a parallel obturator (gate) that raises and lowers between two seat rings. This type of valve is pressure-energized, that is, it depends on upstream pressure to seal downstream. Double expanding gate valves have a gate split into two parts that slide against each other, providing a mechanically energized sealing both on the upstream and downstream seats at the same time.
Ball – Ball valves have an advantage when weight and space become a limitation, as they have a more compact design. In a floating valve, the obturator (ball) is free to move and the seats have fixed positions. The higher the pressure, the higher the force pushing the ball against the downstream seat. Consequently, the higher the pressure, the better the seal. The trunnion version inverts the roles and keeps the ball fixed. Now it’s time for the seats to move. But the overall sealing principle remains the same: the higher the pressure, the more the seat is pushed against the ball and the better the seal. For the same size and pressure rating, torque is higher on a floating valve, which may become a limitation.
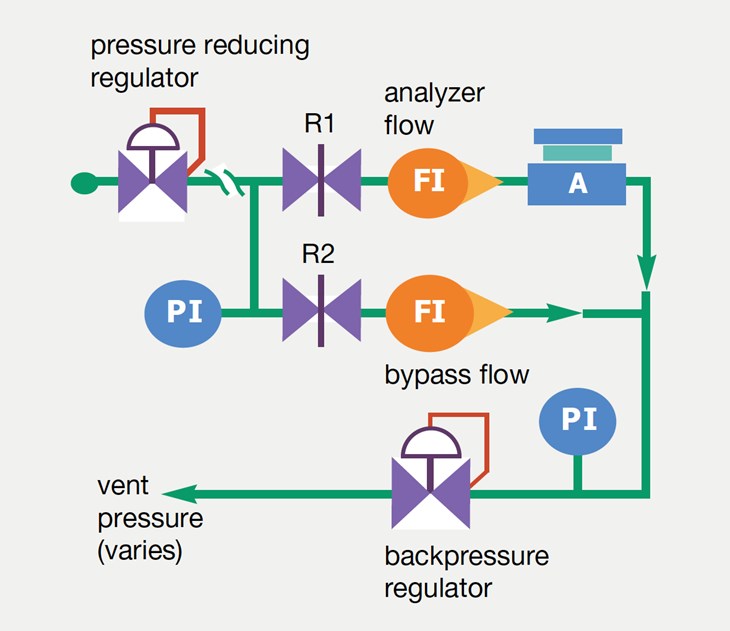
Procurement
One of the most striking differences between surface and subsea valves is in the procurement process. While for a low-risk application on land it is possible to buy a commodity valve out of the shelf from a distributor, for subsea valves this is almost inconceivable.
Subsea valves are not commodity valves; they are highly engineered products tailored for the specific needs of a given project. As such, they are rarely interchangeable and follow a rigid sequence of supplier qualification and design validation before any purchase order is considered. As subsea valves are very expensive valves, installed by very expensive boats, and responsible for the flow control of a product generating several millions of dollars per day, it is no wonder that their procurement process is very meticulous.
Figure 5 gives an overview of what is involved in the procurement of a subsea valve. There are two main phases, design validation and production validation; the former happens before the purchase order and the latter afterwards. Design validation comprises auditing the supplier’s capabilities for designing and manufacturing a valve. During this phase, extensive testing is done on a prototype to qualify the design, including a marathon of cycling, carried both on atmospheric conditions and on a hyperbaric chamber (in order to simulate conditions on sea floor). After testing, valve and actuator are disassembled and all parts evaluated for excessive wear. In the second phase, there are several holding points during the manufacturing process when end users’ representatives must check how the valve is progressing. Once completed, the valve is subject to another set of tests, this time less demanding, to avoid excessive wear on the components.

Conclusion
David Marquet is a former submarine commander of the United States Navy. While talking about submarine warfare he said, “Here’s the thing in war. If you can be seen, you can be targeted. If you can be targeted, you can be shot. If you can be shot, you can be killed. So, the best way to break that chain of events is at the very beginning.” Given what we know now about subsea valves, I think we can adapt Mr. Marquet’s quote to: Here’s the thing about offshore production. You don’t qualify, you get a failure; if you get a failure, it will be next to impossible to fix it; If you cannot fix it, you lose millions of dollars per day. So, the best way to break that chain of events is at the very beginning, making sure valve and supplier are on pair with the project’s demands.
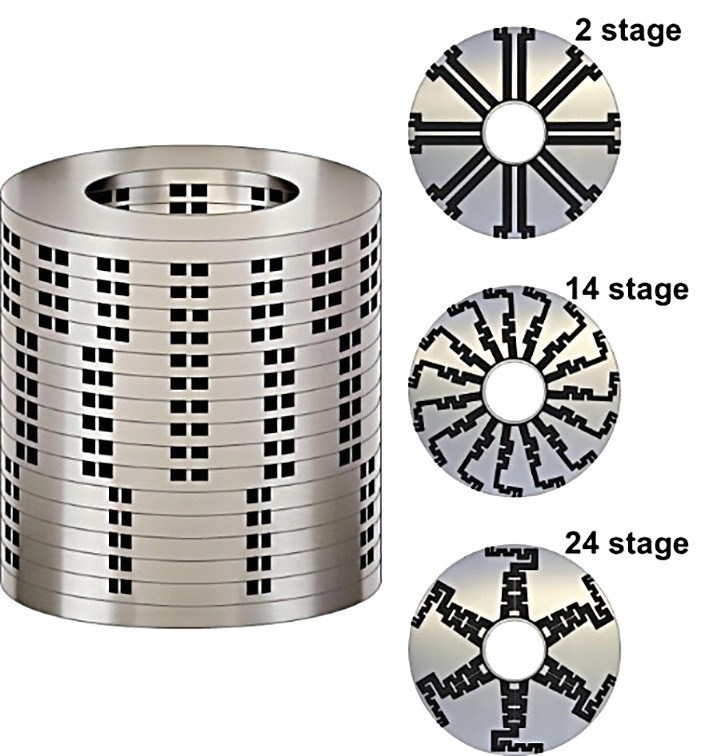
REFERENCES
1. Henanger, T., et al, Managing Installation Tolerances through System Modeling and Tolerance Budgeting, July 2016INCOSE International Symposium 26(1):1176-1191, DOI: 10.1002/j.2334-5837.2016.00219.x
2. Implosion of the Argentinian submarine ARA San Juan S-42 undersea: Modeling and simulation, Chunqiu W., et al, Communications in Nonlinear Science and Numerical Simulation, Volume 91, December 2020
3. Amaya H. & Dyer, A., Failure Investigation of UNS N07718 (Inconel 718) Bolts Under Cathodic Protection for Subsea Oil & Gas Operations, contributed Papers from Materials Science and Technology 2017 (MS&T17), October 8 – 12, 2017, David L. Lawrence Convention Center, Pittsburgh, Pennsylvania USA, DOI 10.7449/2017/MST_2017_873_882