Predicting valve failures can help during a planned shut-down to prioritize maintenance on specific valves, out of hundreds in service, that may potentially present a problem and cause operation inefficiency in the near term. This would, ultimately, reduce wasted time, labor costs, and resources. Obtaining this type of actionable valve health information requires a reliable predictive monitoring system with the application of Artificial Intelligence (AI), that estimates the health condition of each valve and determines the early signs of degradation to diagnosis the problem.
This article highlights the use of the Predictronics (PDX) software to demonstrate this predictive monitoring capability for valves. PDX is a unique end-to-end predictive analytics and industrial AI software solution that collects, analyzes, monitors, and visualizes data to identify potential failures and allow for maintenance to be performed in a proactive manner.
Methodology
For this particular case study, machine learning and predictive analytics approaches, combined with domain knowledge, were used to build models in order to infer the valve health condition. Domain knowledge was used to group the full stroke motion of each valve profile into several segments, in order for aspects of the valve condition to be examined more closely. In addition, features are extracted to characterize valve performance with respect to friction, supply pressure, stiffness/slope, among other aspects. Feature ranking methods were then applied to help determine which features to include in the health model. By merging domain knowledge and the ranking results, a final determination was established.
This data was plugged into the PDX machine learning algorithm, which brings together multiple features into a single health index that estimates the health condition of the valves. The condition of the valves and machines are represented in the software by either a green color, meaning they are operating within a normal and healthy range, a yellow color, meaning they have crossed into a warning stage, or a red color, meaning failure is imminent and immediate action must be taken.
Outcome
Results of this case study at a large valve OEM company have shown great promise to deliver strong business value. An example of the solution is shown in Figure 1. As established before, a green color demonstrates a normal and healthy range, a yellow color, means the condition has degraded into a warning stage, and a red color, alerts to imminent failure, requiring immediate action. In this example, the value health was initially normal (green), but over time it begins to erode, and approaches the yellow threshold condition.
The health index model is calculated from multiple features extracted from the pressure, position, and other signals. In this example, the main contributing feature is related to a position related issue, and this variable has a contribution of 44%. This guides the operator to inspect the position related features and confirm the results of the health monitoring algorithms. The valve health monitoring approach was also able to pick up actuator, leak, friction, and other observed degradations and faults. Validation of these analysis methods with more field data is part of the planned future work. The use of additional sensing, such as vibration and acoustic emission, to complement the valve position and pressure analysis is also possible for this smart valve application.
Everybody Wins
It is envisioned that the smart valve initiative can lead to better customer satisfaction and future service revenue for the OEM. A smart valve will ultimately lead to lower maintenance cost, less downtime, and improved operations for the end-user/process plant. For process plants and other valve endusers, this is an exciting time.
About the Authors

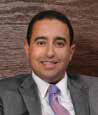
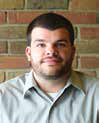