By Brittani Schroeder and Angelica Pajkovic
Paulo Luman has always been curious about how certain products and processes work. He knew from a young age that he wanted a career where he was able to take things apart and put them back together again. “I knew that I was going to end up in the oil and gas industry because my hometown is a very industrial city. We had a refinery, and all the related downstream plants were close by. They were always looking for new mechanical engineer graduates, so after university it seemed like the natural choice,” Luman explained. “I could have chosen the career of a plant or operations engineer, but instead I chose to work on the consulting side of the business.” As a mechanical engineer, he has been able to continually learn about new products and solutions, and is fulfilling his lifelong curiosity.
Luman went to the Universidad de Concepción (University of Conception) in Chile. His professional career has taken him from Chile, to Montreal (Quebec, CA), and finally to Tampa (Florida, USA) where he holds his current position as Manager of Mechanical and Piping Engineering at PegasusTSI.
PegasusTSI is a privately-owned company that provides engineering, procurement and construction management (EPC) services worldwide. Their goal is to serve the needs of their customers, and by doing this, Luman gets to work on various projects and learn about many different processes. He considers himself a lifetime student— always learning news things as he works with more clients.
A Typical Day
Paulo Luman finds that he does not have a typical workday—his days are always interacting with something new. “Work comes in waves for engineers. Sometimes there is a lot to do, and then there is a lull and you must find things to keep you busy,” he said. One of the ways he keeps busy is by working on several projects at the same time. “We know that everyday we will see the same faces at work, but what we are working on and who we are interacting with outside the company is always changing.”
As working on multiple projects at once can be very time consuming, Luman’s days are generally quite full. “Sometimes our projects are all peaking close to the same time, and that makes it a little harder to focus on completing one task at a time,” he related. “You definitely do not get bored.”
Luman also works in what he calls a ‘dual role’. “The first thing I do in the morning is plan out my day. The first part of my role is to manage a team, and so I must make sure they have work to do and they have the supervision and support for whatever they are doing,” Luman explained. “The second part of my role is completing all of the necessary technical aspects associated with mechanical engineering. I need to be well-versed in every single aspect of both of these roles, because it is important to meet the high standards I set for both my clients and my team.” Luman spends a lot of his time in meetings, so he is constantly balancing his team, meetings, and his engineering tasks. “You have heard this a lot, but communication is key. Sometimes, as engineers, we need to learn that skill on the job, as communication is not always our forte,” admitted Luman.
Over the years, and after working on many different projects with a variety of people, Luman has learned many of the ins and outs associated with his clients and their projects. “It is my job to see what they want and how they want it done; to find their needs and hopefully fulfill them,” he said.

The Joys of the Job
The variety of roles and responsibilities he takes on, on a daily basis, is Luman favorite part of his job “Being in a company that works with different specialty chemicals on a regular basis is a lot of fun. One day you can be dealing with a weird chemical you have never seen, and the next day you can be working with a highly explosive chemical that you have worked with many times,” explained Luman. Before working with the new chemicals, or other materials, Luman will study it to make sure he knows how to properly handle it. “Sometimes we even have to study how to say the name of the new chemical. That can be tough!”
Luman believes that the more he knows in the industry, the more he realizes how little he actually knows. “You teach yourself something, and you keep adding to your knowledge everyday. You think you know everything, and then something new comes out and you must alter what you already know to fill in more information. I am always learning,” he admitted. To Luman, there is no such thing as a ‘guru’ in engineering—it is impossible to know everything. The most rewarding aspect of Luman’s job is seeing his work come to life. “You plan and plan, you make calculations, you talk with so many people, and then finally the plant has been built, or the expansion has been completed. Seeing it all finished and knowing that I had a hand in creating this new thing, is incredible,” he explained.
Project Breakdown
PegasusTSI executes projects in all their stages, they usually start with a feasibility study, then cost estimates, process design, basic and detailed engineering, all the way to construction management, commissioning and the always exciting start-up. “We will therefore be with a project from the start to the finish line,” Luman explained.

A Pump Specialist
When asked what kind of pumps he interacts with, Luman said he works with too many different kinds to count. Slurry pumps, positive displacement pumps, sealless pumps, vertical cantilever pumps, submersible pumps, are just some of the many industrial pumps he works with on a regular basis. “Pumps are my bread and butter,” he explained. “For the most part I engage with chemical transfer pumps, which pump solutions from one part of the plant to another, and from one process to another.”
Typically, the Process department or the Client will tell Luman what duty the pumps need to satisfy, and from there he will take over. In most cases, he and his team will find the pumps that will work the most efficiently, for either the expansion of a plant, or for the original construction.
Luman and his team also consider maintenance part of their selection process. “As soon as the pump starts working, we consider it to be dying. We therefore look at how long a pump can last before it needs to be repaired, or have parts and systems replaced,” explained Luman. “We ask the clients to bring in their maintenance engineers so that they can be part of the selection process as well. That way, we have the people who are actually going to be using the pumps putting their opinions in.” As the maintenance engineers will occasionally object to a pump brand or model, during the selection process, Luman and his team strive to ensure that they always have an alternate pump they can suggest which meets the expectations of the client and will not have difficulties operating.
One of the challenges Luman faces when dealing with pumps are the price points. “It is like buying a car: you can buy a very expensive luxury car, or you can buy a standard car with no special features, and they will both get you from point A to point B. A lot of our clients want to choose the standard car because it means saving money,” said Luman. “However, that standard car – or less expensive pump – may break down and require repairs more frequently than the luxury car. Clients are all about saving money, and we are too! We want to give our clients the best price possible. But we also want them to understand what they are paying for, and why certain pumps are more expensive. It always comes down to quality.”

A Valve Enthusiast
“If you work with pumps, chances are you are also going to work with valves,” Luman said. He works with many different valves and considers himself to be well-versed in the valve market. “Selecting valves for use in chemical plants is a very similar process to choosing pumps. We study and understand the process and its fluids, we talk to the clients and find out their needs and preferences, we follow specifications they have set out or even create them for the project, and we work with that information from there.
A challenge Luman frequently faces is that of variety. “Every brand thinks they are the best of the best, so sometimes it can be hard to figure out who actually has the best product for the job,” said Luman. “In the end, it comes down to find the perfect balance to meet all the requirements of safety, reliability, economics and any end user preferences for a particular valve.” Luman and his team will come up with a selection for the clients to choose from, and they will discuss their decisions before choosing the final valve.
Another consideration for valves, like pumps, is price. “The prices will change depending on the quantity I am ordering, so it can be hard to give the clients a final number before choosing the valve and ordering it.”
In some cases, due to the complexity of the design conditions we work directly with the valve manufacturer to come up with a special design or to select the right combination of materials of construction to make the valves suitable for the application.
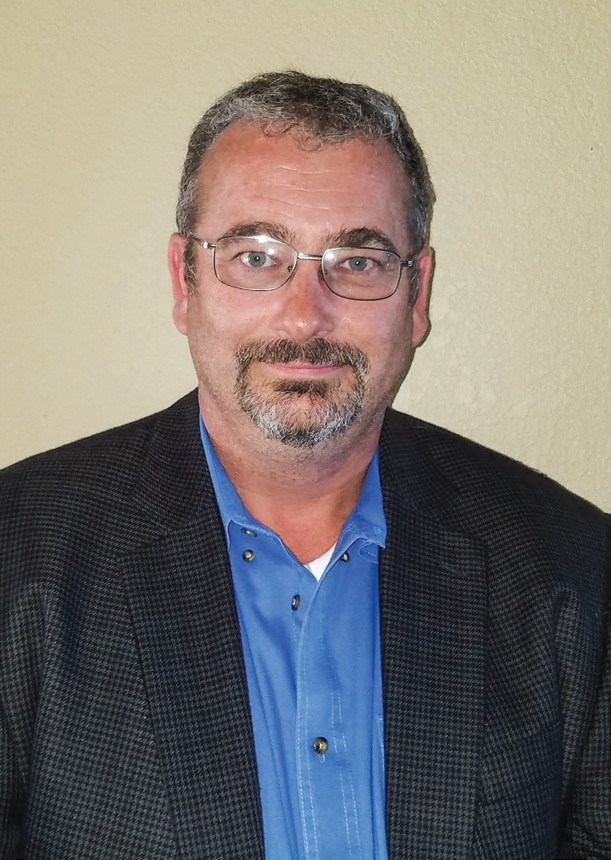
Thoughts on the Future
The constant changes in the industry is both thrilling and a challenge explained Luman. “Sometimes there is not enough time to study every new product out there, but our clients expect us to know everything. So yes, it can be challenging to keep up,” he explained. Luman knows that to satisfy his costumer’s needs, he must find the time to learn on his own. “We try to keep work at work and home at home as much as we can, but there are days when that is not possible. We learn from those times, and we try to make sure it does not happen again.” By learning about of as many pieces of equipment as possible, we are better able to adapt with the changing technology and expand on our ever growing understanding of the industry. “There is a push for highly efficient products, but it takes time to get there. These leaps in technology and products take time, and we definitely feel the nudge to start working on better, more efficient practices,” Luman explained. “We need to find a balance between the new and the old, and I will be helping in the search for that in the near future.”
In recent years, Luman has seen a shortage in new engineers coming out of school. “If we see engineers graduating, there is a strong chance that they will be going to work with new technologies— something that is flashy and exciting. But what people do not realize is that our industry is just as exciting, even if it is a little older,” said Luman. “We want to see engineers who can design tanks, or engineers who can design pumps and valves. The real challenge is getting new graduates to see that there is so much potential working in a more traditional industry so that we can achieve that sought after balance of old and new.”