By Michelle Segrest — Contributing Editor
Bryan Bieschke considers himself a “champion of all things maintenance.” The critical thinking quality-driven maintenance and reliability leader uses his diverse, non-traditional experience to find creative solutions every day for T. Parker Host, a small, family-founded ship agency in Newport News, Virginia.
But his career path was different than many maintenance and reliability professionals.
“I started out by dropping out of college to go to automotive school,” Bieschke explained. “I learned how to be a mechanic working in a shop. I lost my job during the recession of 2008 and joined the Navy. This is where my technical abilities were tested and broadened.”
Bieschke was one of four Ground Support Equipment (GSE) troubleshooters running the flight deck of the USS George Washington. He was responsible for troubleshooting, maintaining, and repairing all machines used during flight operations. Following his Navy stint, he was hired by Caterpillar, where he served as a machine technician performing overhauls, electrical and hydraulic troubleshooting.
“I have had a hand with pumps and valves ever since the Navy, but more recently it has been because my employer, Host Terminals, purchased two facilities in Louisiana on the Mississippi River,” he said. “These facilities have many environmental control, storm water, and facility supply pumps and equipment. It is no secret that pumps are literally keeping New Orleans above water, so what better place to get an opportunity to work on them.”
Bieschke currently serves as the Director, Maintenance & Reliability. In this role, he builds, standardizes, and oversees all the maintenance programs for Host terminals. This includes cranes, heavy equipment, valves, pumps, conveyors and all other types of equipment.
“As an individual and as part of a team, I direct and manage programs, managers, and technicians in RCM of electrical, mechanical, and hydraulic machinery,” he said. “I am experienced in developing and implementing maintenance programs that employ CBM and PdM. I have also gained experience in the implementation and use of various CMMS programs. From my military background, I have learned that dedication and attention to detail are paramount, mixed with a high degree of skill and safety.”
The majority of projects that Bieschke works on are process oriented, he explained, but he has also led projects on stacker reclaimer overhauls and commissioning, crane rebuilds, facility pump upgrades, and many heavy equipment overhauls.
He considers heavy and industrial maintenance management, business alignment, holistic reliability, and leadership among his areas of expertise.
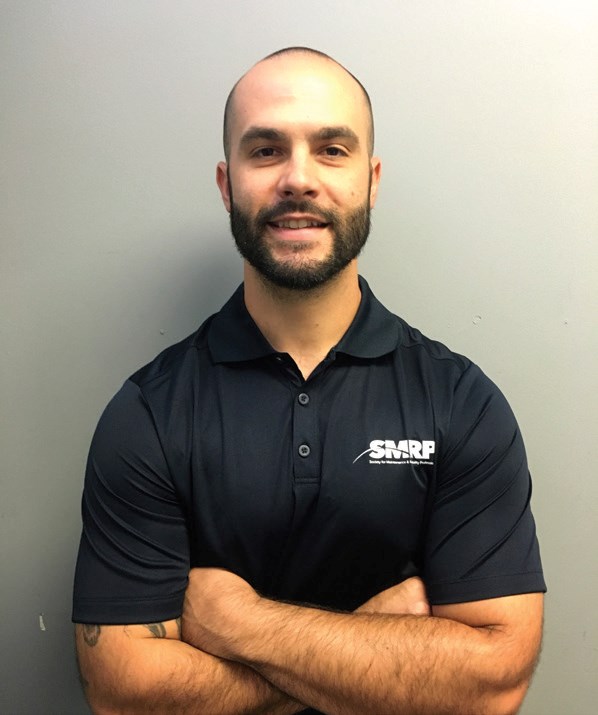
How End Users Solve Problems
Bieschke believes that the vast majority of pump and valve problems begin in design or system design and then are further exaggerated by poor installation.
“The remedy for this is to always have a cross-functional team of people to work on design and installation, making sure there is alignment of what is needed from the asset,” Bieschke explained. “This includes business leaders, engineering, maintenance, and operations. The goal is to specify it correctly, and then get the who/what/where/how/why sorted out before its breaking on your dime.”
In his experience, Bieschke said that one problem plaguing some industries is in the fact that some valves are of out sight, and therefore, out of mind.
“Some valves can remain in one state for years,” he said. “These valves only come into view when something fails or when maintenance is needed on something up or down stream. The problem is that the valve then needs to function as intended, and all maintenance and reliability professionals know that it rarely goes that way. This adds more time to your repairs (MTTR) and therefore effects your outage window, further compounding down the line.”
The answer, he said, is simple in explanation but often tedious in execution.
“Rank your valves based on criticality (Operation, Safety, Environmental),” he recommended. “Have a working list and location of all the valves in your CMMS and schedule periodic maintenance based on criticality. This can be as basic as cleaning, lubricating, testing/actuating or as complicated as your business objectives dictate. The effort will be worth it.”

Maintenance and Safety Tips for Valves and Pumps
From his experience, Bieschke recommends the following tips for maintaining valves:
1. Thoroughly inspect valves before installation, even if they are brand new. Observe case markings for direction, PSI, flow rate, materials, etc.
2. Cleanliness always is key, especially around seals and gaskets. Foreign debris can compromise sealing ability but can also give false bolted joint torque readings, causing mechanical looseness over time. This is especially in the case of heavy corrosion.
3. Be mindful of pipe and mounting stresses that could affect valve actuation. If you are forcing bolts in or having to use excessive force, you could be distorting the valve body.
4. Remember the basics of lubrication, testing design parameters, cleaning, etc.
He also offers some tips for maintaining pumps:
1. Standardize your inspection procedures to target failure finding and create repeatability.
2. Weigh the benefits of having old pumps rebuilt or new pumps internally coated to fight corrosion and erosion, leading to suction inlets opening up and effecting NPSH.
3. Incorporate inspection criteria for pump, prime mover, pipes, and foundation viewed together. This gives technicians a holistic understanding of the pumping system, which can lead to more in depth inspection and understanding.
4. Remember the basics of monitoring lubrication, seal leakage, vibration and discharge pressure. The latter requires gauges on both suction and discharge.
Bieschke also shares some safety tips for working with valves and pumps:
1. Observe signage and guarding. Remember that pumps are rotating assemblies and can be an extreme hazard when in operation. Valves are control devices and may be protecting something or keeping a system working.
2. Have an isolation plan and understand how to activate it in case of an emergency. Being able to close/open a valve or start/stop a pump could be the difference between a small spill and a catastrophic failure. Automation and test schedules help to eliminate human errors.
3. With regard to specification and design, know what you are working with and ensure all components of the system are compatible. Remember that two valves can look identical but be very different.

Tackling Challenging Projects
Bieschke’s daily activities include meeting with his maintenance leaders to discuss past and future operations and meeting with operations leaders to get feedback and alignment. He daily dives into analytics by using the CMMS program and continuously creates process improvement strategies. He also spends a lot of time writing and auditing PM/Inspections for standardization. He also knows the importance of talking directly with all maintenance personnel to get the real information from the “people actually doing the work.”
Aside from the daily activity, he often must tackle more difficult challenges.
“Implementation of our company’s CMMS system was my hardest project so far,” he explained. “I had to align six different terminals across the country. These terminals have different assets, operations, environments, and so on. The way I accomplished this was by first bringing people into the process. This included technicians, managers, and support staff. I needed buy-in from all levels. Then, I established champions at each location that were accountable for upholding the standard. There was a lot more that went into this but these were the high points, and truth be told, it is still work to this day. Anything worthwhile is not easy.”
An Industry Outlook
Bieschke said there are two major trends in the industry that essentially have the same outcome—a need for more and better training.
“We are seeing in many industrial trades the lack of knowledge and basics of technicians to perform the needed functions,” he explained. “This often is the cause of many common pump failures like seals, bearings, alignments, etc. The remedy to this is a structured mentoring and OJT plan. But I am a realist, and I know that it’s pretty difficult in today’s fast-paced environments to quickly achieve measurable results that will reinforce the efforts. However, I am still a huge champion of any kind of mentorship and training regardless of size.
“On the opposite end of the hierarchy is the push by many organizations to be more efficient. In pumps and valve language this means more reliable assets that can be monitored remotely—for example, the Industrial Internet of Things (IIoT) and the collection of big data to drive decisions. Here, however, we fall back into some individuals and departments possibly not being trained enough or being completely overwhelmed by it. I find that even if the technology is implemented with some degree of accuracy and structure, it still falls on the humans involved with the process to make it successful. This requires training and ownership.”
Bieschke believes that IIoT will continue to revolutionize all industries.
“I just hope we, as humans, can keep up!” he said. “I also firmly believe that finding people to turn the wrenches and guide the processes will continue to be difficult. This actually further justifies IIoT and condition monitoring by providing outlets to not touch machines until they need it. The end goal of maintenance is to do nothing. This is only achieved by designing out failure modes and monitoring machines remotely.”
Even though his education and experience were achieved in non-traditional ways, Bieschke has wise experience for other end users who are beginning careers working with valves and pumps.
“Always seek knowledge,” he advised. “Do everything you can to surround yourself with people who come to work present, positive, and ready to perform. Never underestimate the power of fundamentals and the precise application of those fundamentals. Keep things simple.”
And most important… “Be a doer, not a talker. And know the difference.”