By Daniel Sweet
Though trained as an engineer, Bridget Spencer does not deal solely with process components and project documentation. Instead, she combines her technical knowledge with a passion for people, helping to manage a sizeable team of engineers—her team is comprised of over 130 individuals—within the Instrument Engineering and Design Department at Wood, a global engineering and consultancy firm.
Based in Wood’s Houston office, Spencer’s team provides expert technical and engineering solutions to Wood’s clients on a variety of project types. In a recent interview with Valve World, Spencer described her role as a manager and touched on some of the challenges—and the rewards—the position has afforded her over a 14-year tenure with the company.
“At Wood, my department supports projects in many sectors, ranging from downstream refining to midstream on shore and upstream offshore projects. We deliver both greenfield and brownfield projects, along with automation and pipeline assignments, and onshore and refining activities. We support client projects with the expertise needed to deliver the best outcomes, and my department contributes to proposals, provides detailed engineering manhours, scheduling insights and then delivers on projects from study to FEED and through the detailed design phases.”

Dramatic Change
Spencer says she was first attracted to Wood because of the stability it offered. Coming from an operations background in food & beverage, she found that her irregular hours and the “shift mentality” of her workplace did not match with the schedule she wanted for her family.
As she moved from an engineering to a management role, she quickly realized the additional benefit of working for a global company, namely the ability to work across a diverse range of projects and sectors.
“As a manager and engineer, I am proud of all the different projects I’ve been able to work on in a relatively short period. In one of my first assignments, I was working on a coker project for a refinery, and I followed that up by working on a cryogenic project. I went from the hottest process in the world to the coldest process in the world. This dichotomy was interesting because of the different metallurgies involved, the batch processing versus continuous processing, and all the different factors you have to take into account: with valve usage for example, steam purges on valves with cokers, but not in a cryogenic system. This dramatic change between one assignment to the next is representative of all my work with Wood. It is also reflected in my current department: my team is capable of switching between a host of tasks within multiple sectors, and for me, this diversity of experience has been the most interesting aspect of the job.”
Employee Engagement
Asked about the other dimensions of her work, Spencer emphasized her work with people and the never-ending cycle of employee training and knowledge transfer. “My current role is very much centered around people engagement and management. But I also have to make sure that I have the right technical knowledge within my team to deliver on a wide variety of projects; in this way, I have to be sure my team members are trained so they can do any number of jobs.”
“On the people engagement end of this,” she said, “it comes down to managing my team to keep them on-task and on-deadline. It also means solving problems. If we do get off schedule, I need to determine how to get us back on track. More broadly, I need to communicate to my team the motivation behind leadership decisions, helping my team to understand these motivations in a way that relates to them. After all, an employee knows the company wants to make a profit. However, they do not always see how this connects to their day-to-day activities. Employee engagement is crucial to address this.”

Strategic Staffing
“One thing that helps with employee engagement is knowledge sharing. In terms of training and advancing my team’s knowledge, this is an ongoing and, really, never-ending cycle. We are a team of engineers and designers that are dealing with multiple projects and business sectors. So, we have to embrace change and the fact that different team members will have a variety of challenges come across their desk. And while it is great to have specialties as an engineer, I also want my team members to diversify their knowledge to become well-rounded in their capability and delivery.”
Asked about the strategies she employs to create this well-rounded group, Spencer explained the concept of strategic staffing. “It is important to me that my team members do not get pigeonholed into one discipline area. So, if we have a subject matter expert in a particular project, I do not want them to be in a position where that is all they do for the rest of their career. Instead, we strategically pair people up. For example, a new college graduate would team up with someone more experienced that wants to teach them about his or her specialty. In this setup, there would be daily meetings to go over any questions or challenges. More broadly, about half of my engineering team come to a weekly lunchtime training session where we go over different technical subjects and competencies. About 10% of my team are junior engineers that have an additional lunchtime training session weekly as well, focused on getting a solid foundation to build upon.”
“I am trying to nurture a group that is not afraid to admit that they do not know something,” Spencer concluded, “because asking for help and instruction is one of the best ways to learn.”
Biggest Challenge for an Instrument Engineer
Even as Spencer’s team shares knowledge and transfers skills across the team, there will always be challenges to tackle when the department works across a diverse range of sectors. Spencer said that “a complete understanding of the process is crucial and this is the biggest challenge for an instrument engineer.
Take varying ambient conditions of the environment and the technical challenge this creates. If you are in the Saharan Desert versus Newfoundland, you’re going to have completely different ambient conditions. The environment is going to determine factors like painting and insulation, as well as material selection. This also pertains to safety. Safety ratings on valves, for example – especially for on/off valves. Safety applications require a higher Safety Integrity Level (SIL) for reliability. The different top works components can have their statistics on the reliability ratings and a lot of what I have seen from valve manufacturers recently is to rate the system as a whole, rather than having the individual components itemized separately e.g., the solenoid separate from the positioner, separate from the actuator.”
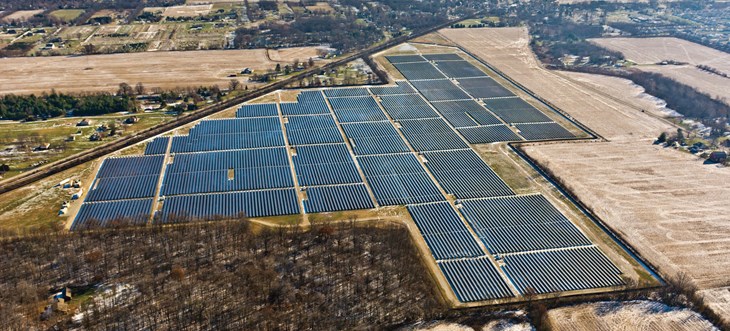
Digital Evolution
Wrapping up the interview, Spencer shared her observations on some of the latest trends that are becoming important across projects, especially regarding the Internet of Things (IoT).
“The process industry is digitalizing. However, while we are certainly experiencing a digital transformation, it is not happening all at once. Take, for example, the IoT and digitally-enabled automation. One of our primary tasks when working with clients is to determine how adaptive they are to new technologies. Based on their operating environment, culture and appetite, we will make recommendations and provide guidance to suit. Wireless transmitters for process plants have been around for years now, but I have only recently seen them become truly widespread. This is somewhat dependent on the component as well. For example, clients setting up a tank farm are very comfortable using wireless techniques, but it has been somewhat slower for those in the valve industry. There is so much potential, though, as you can do predictive maintenance on valves with wireless technology. So when it is possible to recommend to a client that they implement IoT solutions, we try to make sure they are aware of the potential.”
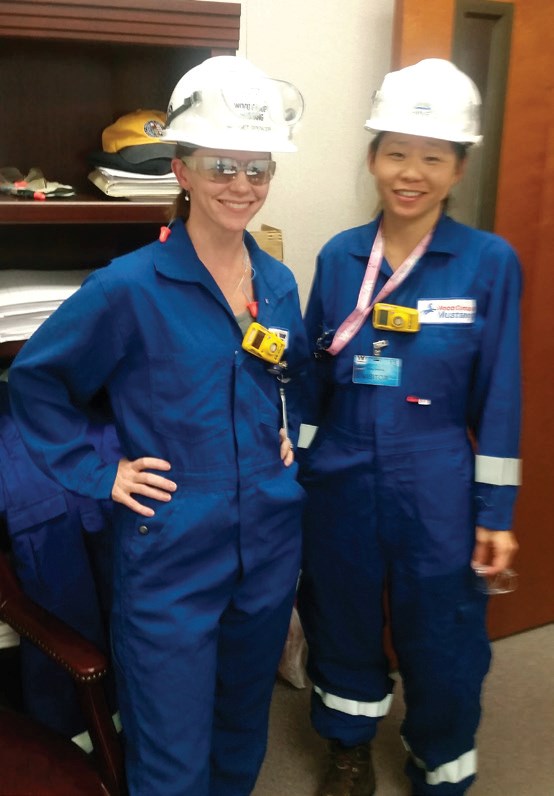
WOMEN IN ENGINEERING
To spotlight women in engineering, Wood released a brief interview with Ms. Spencer in March 2019. On the topic of her position as a department lead one of only a few female department managers in Wood’s engineering space Ms. Spencer said: “I do not see the energy industry as a man’s world. I see it as my world. I recognize that I’m the only female department manager just now, but I don’t let it define me. I do not want to be the best female department manager; I want to be the best department manager.”
ABOUT WOOD
Wood is a global leader in engineering and consultancy services across energy and the built environment. Providing consulting, projects and operations solutions to unlock solutions to some of the world’s most critical challenges, the firm employs around 45,000 people in more than 60 countries. As Spencer describes it, “Wood is a complete lifecycle solution to our clients. Clients come with a challenge or problem, and we come up with a solution. Then we do the complete design, material procurement, and construction support. And finally, once the project is up and running, we have a team in Wood that allows us to staff their facility on a contract basis. In the offshore sector, where projects and facilities have a life expectancy, we provide decommissioning services too. Wood is there every step of the way—the complete lifecycle, in every sense.”