By Brian Booth – Assured Automation
Up until now, estimates of greenhouse gas emissions from industries have relied mainly on paper-based calculations of what is pouring out of tailpipes and smokestacks, based on the amount of energy consumed by people and businesses. Other data relied upon was gathered through “self-reporting” by industry.
As satellite technology improves, researchers are starting to stress test that data – and the early results show leaky oil and gas industry infrastructure is responsible for far more of the methane in the atmosphere than previously thought.
It is estimated that 51% of all fugitive emissions have been attributed to valves.1
Any producers working with toxic gases such as those listed in Table 1 are upgrading their process lines to prevent fugitive emissions. A big focus of this effort involves the valves used.
As with all significant upgrades, there are significant costs involved. But fear not – chemical and petrochemical companies have a strong business case to upgrading both legacy production plants and newly designed lines.
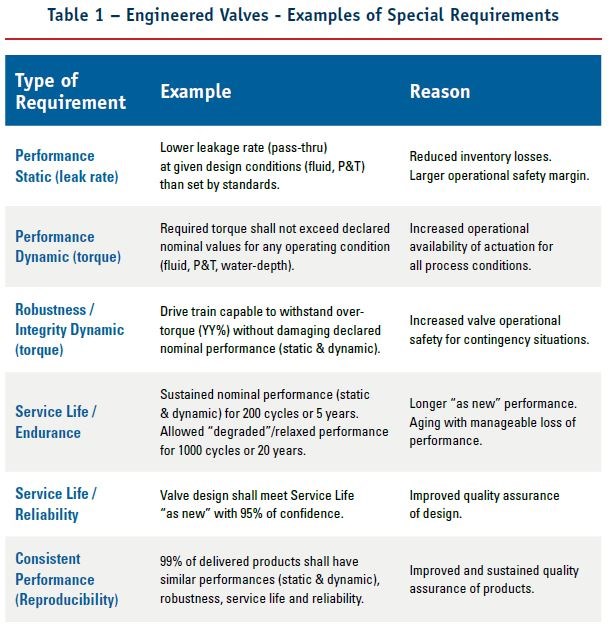
The Business Case for Justifying the Cost of Upgrades Includes:
- Avoidance of Fines & Lawsuits
- Avoiding Plant Shut-downs and Process Line Downtime
- Avoiding Increased Insurance Premiums and Workmen’s Compensation Costs
- Compliance with International, Federal, and State Regulation
- Compliance to Industry Standards
- Improved Public Relations and Market and Industry Protection
1) Avoiding Costly Fines & Lawsuits
Installation of leak tight valves is much less expensive than costly fines for fugitive emissions violations. Recently a Wisconsin chemical plant that processes spent solvents was assessed with USD $480,500 fine for air pollution violations. That amount is far greater than the cost they would have incurred to upgrade their valves. Plus, now they have to upgrade anyway to avoid further fines.
American Synthetic Rubber Company: fined for USD $135,375 in 2019 plus four other agreed orders since 2009 totaling more than USD $170,000.
Section 304(a) of the Clean Air Act, 42 U.S.C. §7604, authorizes citizens to bring suit in federal court to enforce the Act. This CAA “citizen suit provision” authorizes citizens to obtain an injunction and civil penalties of up to USD $37,500 per day (almost USD $14 million per year) for each violation. This fact has environmental groups and attorneys lining up to bring suit against any company that is a potential target.
And remember, even if the suit fails, there is the high cost of defending against it. If it succeeds, the defendant still has to fix the root cause that lead to the suit and decision on top of paying the penalties.
2) Avoiding Plant Shut-downs
Plant shut-downs or even single process line downtime can be very costly. The added investment of incorporating modern valve designs to limit fugitive emissions and/or alert to stem seal leaks is well worth it if even a single breakdown is prevented.
3) Avoiding Increased Insurance Premiums and Workmen’s Compensation Costs
When high emissions are found to be present, regardless of the cause or method of detection, insurance premiums will no doubt rise when the insurance provider becomes aware. Additionally, when these emissions cause any employee to take leave from work, your workmen’s compensation costs naturally will increase.
4) Regulations – International, Federal & State
The oil and gas sector is upgrading lines in their upstream and downstream operations that process natural gas, 90% of which is composed of methane. The oil and gas industry makes up the largest source of non-combustion emissions.2
Although the federal government recently rolled back some methane regulations for the oil and gas industry, much of the energy policy decisions are made at the state level. For example, California, like 34 other states, has a renewable portfolio/clean energy standard. Some of these regulations include international ones such as TA-Luft, a German air pollution control regulation, and federal regulations such as EPA Method 21.
5) Industry Standards Compliance
The industry standards are evolving to meet the challenge of restricting fugitive gas emissions. Such standards are being developed and modified by organizations such as:
- API (American Petroleum Institute)
- ISO (International Standards Organization)
- MESC (Material and Equipment Standards and Code)
- ANSI (American National Standards Institute)
- TA-Luft (German: Technical instructions for keeping the air clean)
6) Market and Industry Protection
With the political and social focus on climate change at an all time high, many industries are under the microscope like never before. Legislators and the government agencies are under ever increasing pressure to impose even more strict regulations than those in place now. Calls to ban coal, fracking, oil, and gas are now commonplace. The public is becoming more and more aware that methane is far worse for the atmosphere than carbon dioxide. For that reason, Methane leaks threaten entire natural gas industry.
In an effort to combat these movements and ease concerns of man made climate change, many individual corporations have committed to limit methane emissions on their own, regardless of federal directives.4
For example, Duke Energy Corp. aims to achieve net-zero methane emissions from its gas utility business by 2030 by reducing fugitive emissions from their compressor stations and valves.5 BP has set 2050 as a goal for their net-zero initiative.6 These two and many more of the largest energy companies can afford the related costs of such efforts and believe that protecting their reputation, and that of their entire industry, is well worth it. They realize that the appeal of cheaper energy will not outweigh the fact that it is considered “dirty energy”.

Case Closed! It is Time to Upgrade – What Can Be Done?
Well, why not start with the largest contributor of emissions – Valves!
A great place to start is to install or retrofit valves with multiple levels of fugitive emissions containment devices, and superior stem sealing that reliably perform – even during extreme thermal cycling. Emission reducing valves of all types have recently been and continue to be developed by the leading valve manufacturers in the world.
Quarter-turn Valves that get the Job Done!
This article focuses on the three main types of quarter-turn valves which are prevalent in most process industries, ball valves, non-lubricated plug valves, and butterfly valves.
Ball Valves: One of the simplest yet most effective and versatile solutions for ball valves is the addition of a secondary containment unit. These mount directly to the top of the valve stem with a gasket between the two flanges. They are essentially stem extensions with a backup stem packing on their top end which will contain any emissions that escape through the valve’s primary stem packing.
In addition to providing this backup sealing, there are other functions that these devices can perform using a port in their side which is simply plugged for standard use:
1. A gauge can be installed in that port for local visual indication that the primary stem seal is leaking. A pressure transducer can also be used to monitor pressure remotely, and alarms can be set to alert when the pressure rises.
2. A sniffer sensor can be installed permanently to for constant monitoring to detect leakage of hazardous emissions.
3. A full port ball valve can be installed either directly to the port or at the end of a short pipe nipple to prevent them from being swept away by the wind or diffusing into the atmosphere and the ball valve allows for quick and easy access for sampling.
4. A button head check valve (similar to a zerk grease fitting) can be installed to act as a plug, but also allow for easy injection of sealant if and when a leak occurs.
5. A pressurized air line can be attached that has a higher pressure than that of the line. This will prevent any leakage through the stem seals.
6. An exhaust air line can be attached to route any emissions to detection, collection, or analysis devices.
This simple and economical addition can be retrofitted onto many ball valves that are in the field whether they are manual or actuated. They can also be ordered as an integral part of new installations.
Plug Valves: Common non lubricated sleeved plug valves are now available that pass all four thermal cycles without any stem packing adjustments. In contrast to the ball valve solution that can be retrofit, these valves have a unique plug and body to work in conjunction with a special containment bonnet that eliminates any leakage possible through the standard plug valve stem packing. The plug/stem assembly features a live loaded stem cartridge to deliver world class low-E performance.
Butterfly Valves: As with the plug valves, unfortunately this is not an easy add-on to existing valves. High performance butterfly valves are available with Low-E stem sealing in both double and triple offset varieties. The stem sealing is compressed under load either by live loading through Belleville or spring washers or through the use of adjustment bolts.
In summary, you can greatly reduce your fugitive emissions through all quarter-turn valves in two ways: Using valves with specialized stem sealing options or adding a containment device with backup sealing to existing valves.
REFERENCES
1. https://assuredautomation.com/news-and-training/fugitive-emissions-valve-regulations/
2. https://www.desmogblog.com/2020/04/25/new-satellite-data-confi rms-scale-methane-leaks-permian-region
3. https://www.nytimes.com/2019/12/16/climate/methane-leak-satellite.html
4. https://www.sierraclub.org/sierra/why-epa-really-repealing-methane-emissions-regulations
5. https://www.spglobal.com/marketintelligence/en/news-insights/latest-news-headlines/duke-energytargets-net-zero-methane-emissions-at-gas-utilitiesby-2030-60679269
6. https://www.hydrocarbonengineering.com/the-environment/17082020/bp-america-comments-onmethane-policy-rule/
ABOUT THE AUTHOR
Brian Booth is Vice President of Sales and Product Manager for quarter turn valves at Assured Automation. His product lines include plug valves and ball valves with emission containment bonnets. Assured Automation is a value added distributor of actuated valves that “Makes Valve Automation Easy” for customers by building complete actuated valve assemblies including accessories such as positioners, limit switches, and solenoid valves. Brian and his team at Assured Automation would be happy to assist you in suggesting valve solutions to reduce fugitive emissions at your facility.