By engineering and manufacturing mounting kit components – the brackets, couplings, and hardware that connect valves and actuators – to exacting standards, VanAire has extended the quality, safety, and longevity of their clients’ equipment.
“Over the past 25 years, our clients have come to understand that having engineered mounting kits is essential for their reputation,” notes Steve Soderman, CEO of VanAire. “Even if they’re using a great valve and actuator, if they don’t give the mounting kit the same attention, their equipment may fail prematurely.”
VanAire partners with leading valve and actuator manufacturers and their distributors across North America and beyond. Producing kits that weigh from about a pound to over a ton, these components – which API and ISO classify as torque transmitting devices – are used in the oil and gas, power, mining, waste and wastewater, chemical, pulp/ paper, and food production industries, to name a few.
“In some cases, convincing manufacturers and their distributors to put the same quality and safety lens on mounting kits as they do their valve or actuator requirements isn’t easy,” states Soderman.
“Changing a paradigm takes time, patience, and facts; in some cases, it took equipment failure, or worse, for them to consider that an inadequately designed mounting kit may be the root cause of the assembly not functioning as expected,” says Tony Lambert, VP of Valve Automation Hardware. “VanAire is proud to be recognized as a global leader in valve automation hardware and a go-to source of mounting kit solutions because we adhere to application requirements along with industry and customer specifications.”
Because the mounting kit is truly an essential piece of the assembly, many of the questions asked when specifying a valve or actuator need to be addressed when designing a mounting kit. Process and ambient temperature, number of cycles, cycle speed, on/off or modulating use, and/or corrosion, to name a few, may all affect design and materials selection. For example, a mounting kit for an offshore drilling rig may require different materials or coatings than that of an onshore application; a kit subjected to a high number of cycles may have a different design than a kit operated only a few times a year; or a kit subjected to higher temperatures may require a different design than a kit operating at room temperature.
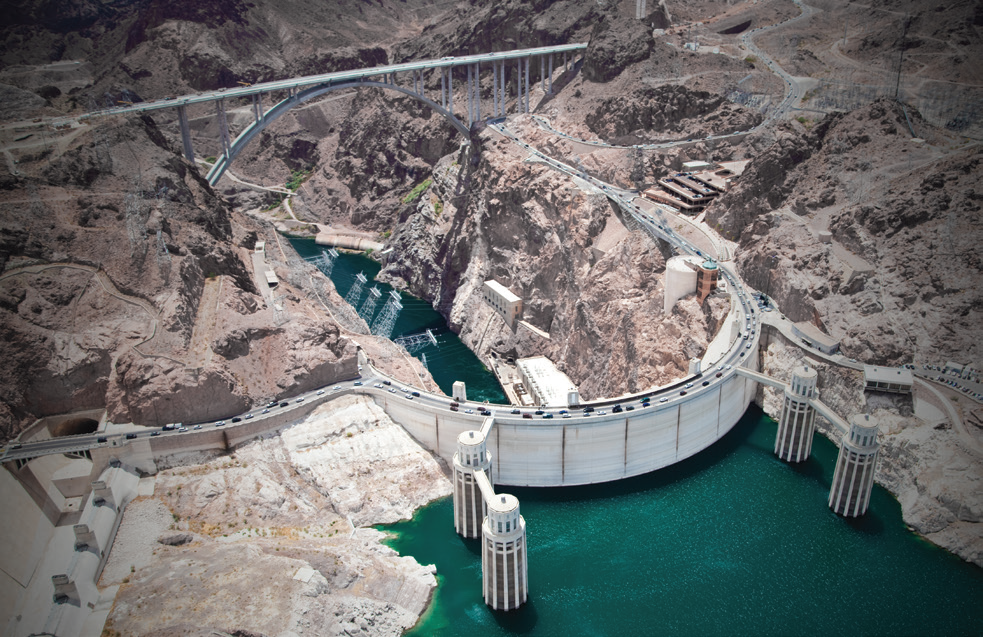
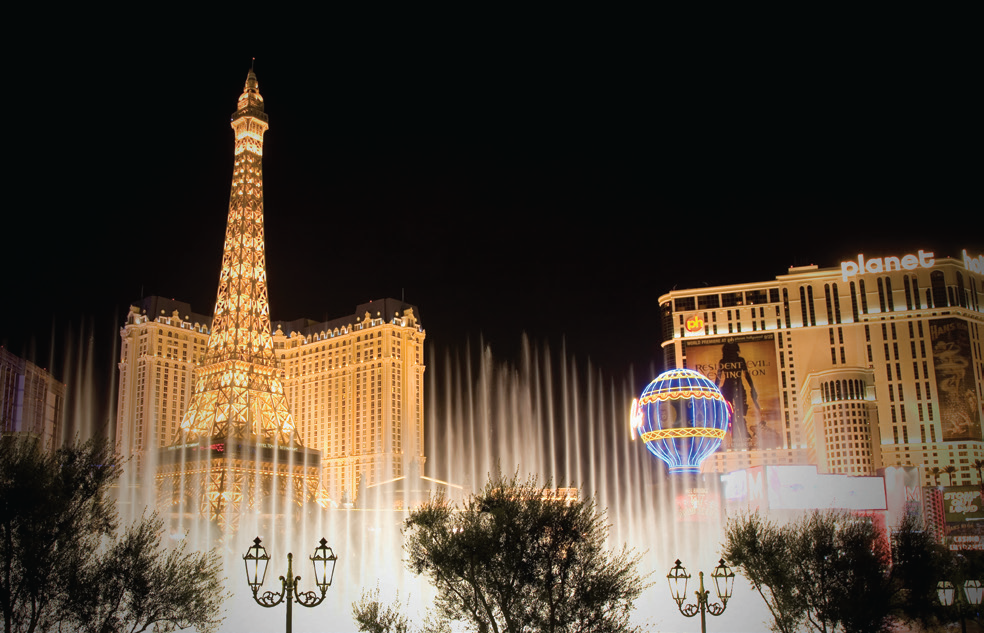
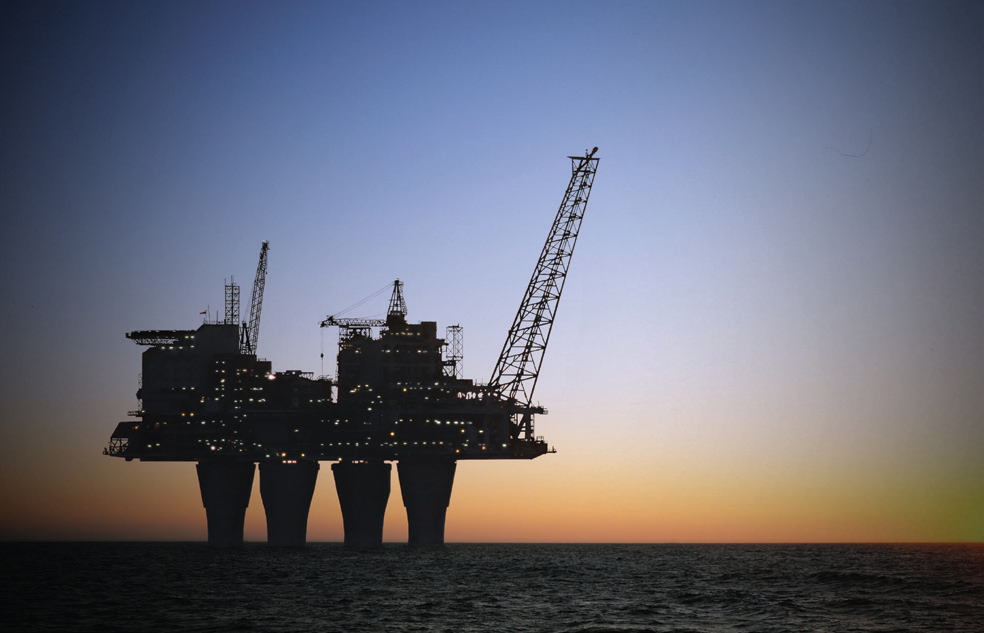
“Along with our experienced and ultra-efficient team, the design and manufacturing consistency resulting from our formal ISO 9001:2015 Quality Procedures and Work Instructions really set us apart,” adds Eric Miller, VP of Manufacturing. “These quality procedures have enabled us to increase our throughput, reduced our lead times and – at the same time – increased our on-time delivery to customers on a global scale.”
Within VanAire’s 45,000-square-foot facility in Gladstone, Michigan, visitors will find more than 75 skilled professionals including professional and mechanical engineers, certified solidworks professionals (CSWP), American Welding Society (AWS) certified welding inspectors and qualified welders, and American Society of Mechanical Engineers (ASME) section IX welders utilizing the following state-of-the-art resources: 15 3D CAD stations with FEA capabilities, more than 30 CNC machines including robotic welders, laser-cutting systems, machining centers, turning centers, press brakes, blind hole key seaters, and robotic machine tenders.

“VanAire’s success is not a result of happenstance or luck,” notes Miller. “Our strategy from day one was to be known as the engineering leader in this industry. We saw a need to take a product that was previously identified often in this industry as a commodity item or even an afterthought and set out to make a difference and help educate the industry that a mounting kit is indeed a critical part of the assembly.”
What’s next for VanAire? Lambert says being a leader in this industry is a humbling, honoring, yet challenging position to be in. He knows VanAire needs to be constantly looking forward to ensure that it continues to take what it has learned and apply that knowledge in a way the team, customers, and industry as a whole can benefit from. “We feel that 2020 will be a milestone year for us,” says Lambert. “We are going through a process that not only refreshes our brand logo but also helps promote our mission and culture. One of the key parts to our continued success is to ensure that our team members know why VanAire does what we do and the way we do it. If your team doesn’t know the why, then it’s hard for them to take ownership and pride.”
VanAire is excited to launch a tool this year that will allow core customers to obtain kit numbers, prices, basic design drawings, and applicable engineering standards through a customer portal 24/7. The team believes this tool will revolutionize how it will interact with customers. Customers will also be able to track their personal quote history, tie that history to specific project names, and easily communicate with their favorite VanAire salesperson. Focusing on quality and continually improving processes has enabled VanAire to partner with leading manufacturers on noteworthy projects across the globe.
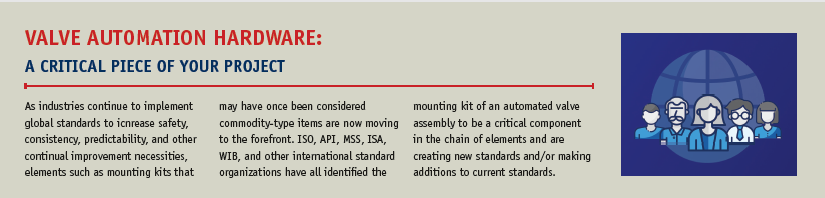
The Anatomy of a Locking Kit
Locking kits are used with automated valves to prevent valve rotation, i.e. “locking out.” This device is engineered to keep a valve in a locked position, either open or closed, even if an actuator is unintentionally engaged. This allows the maintenance team to safely and securely work on other parts of the system without concern that the valve will be accidentally engaged.
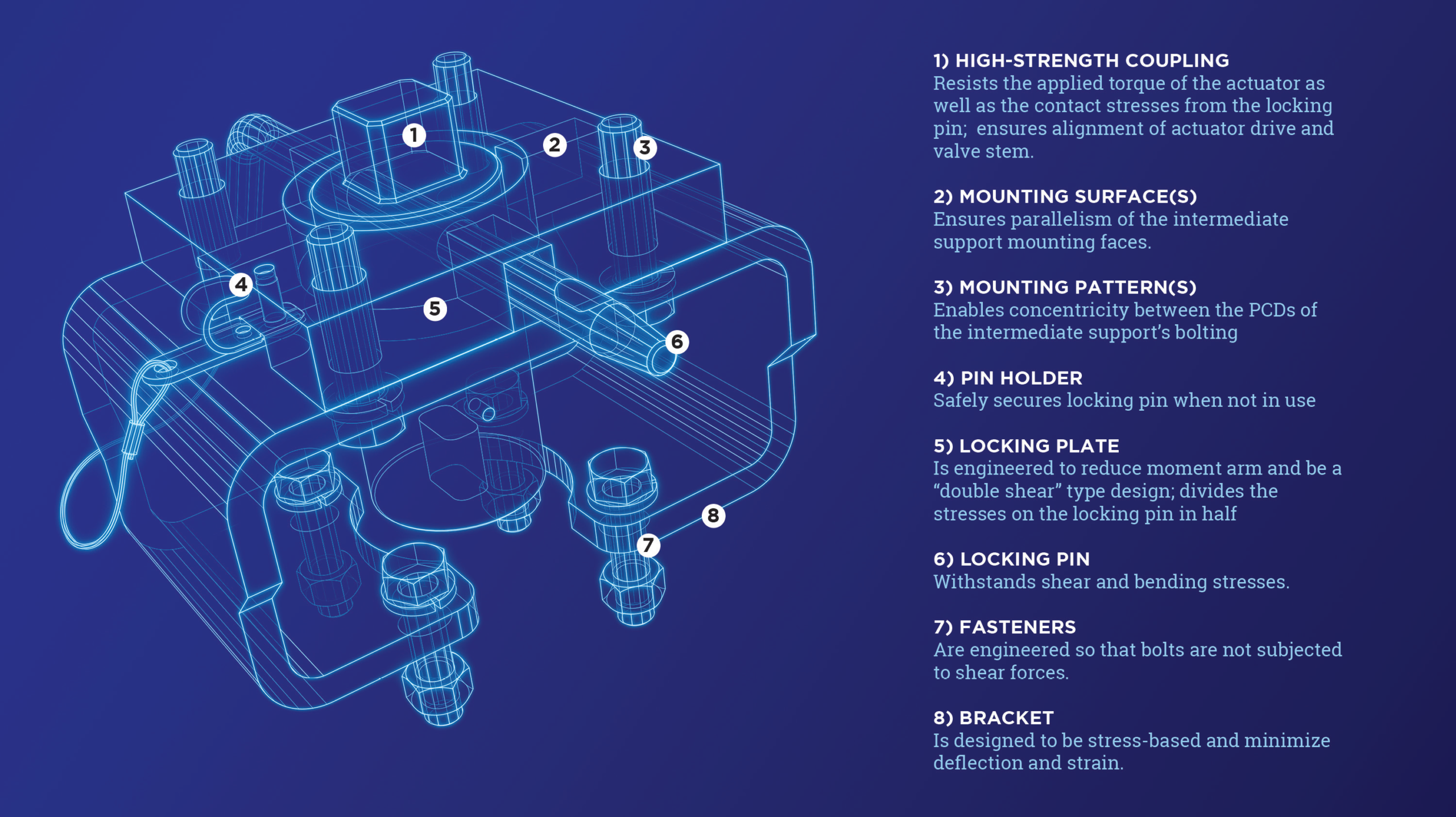
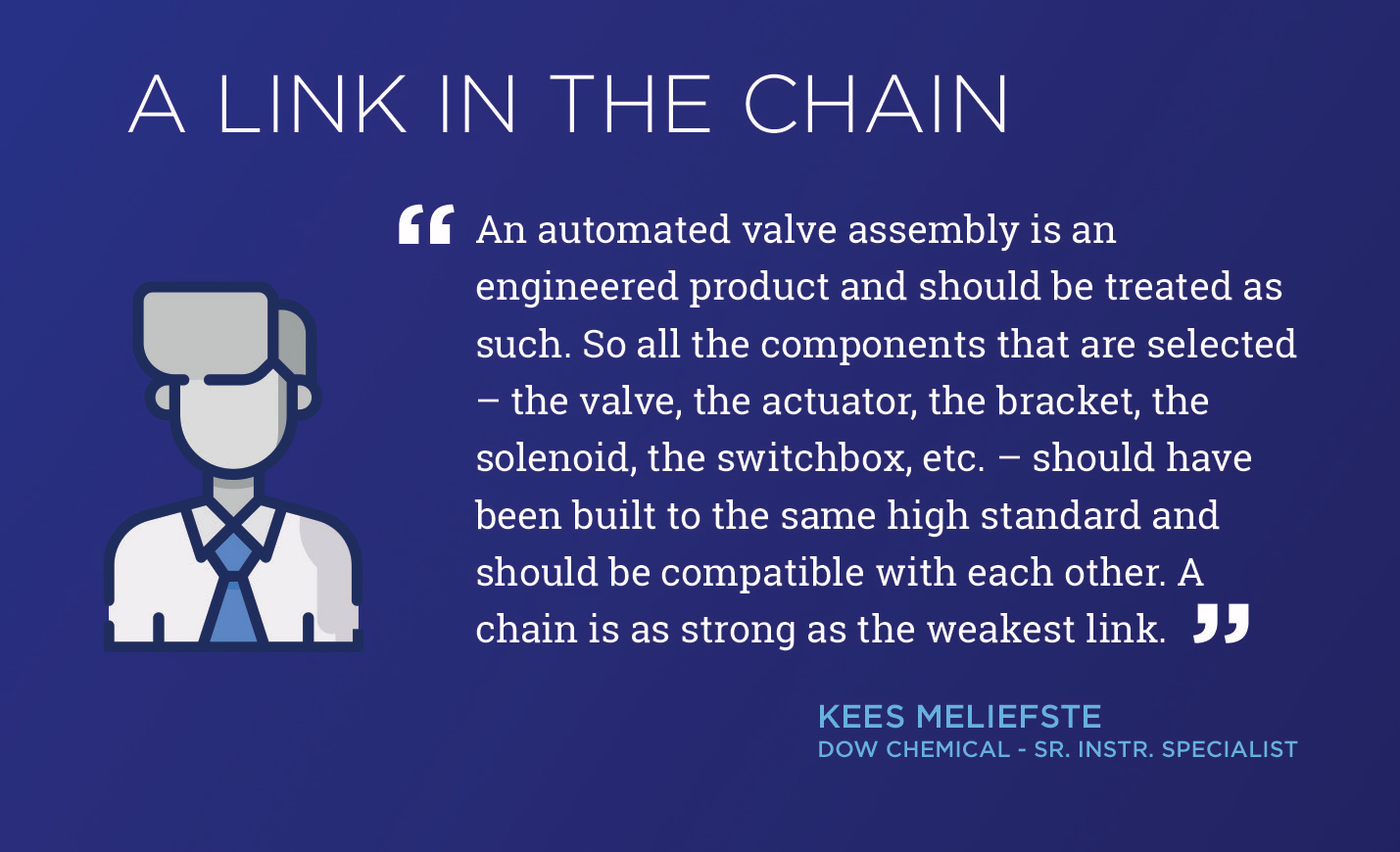
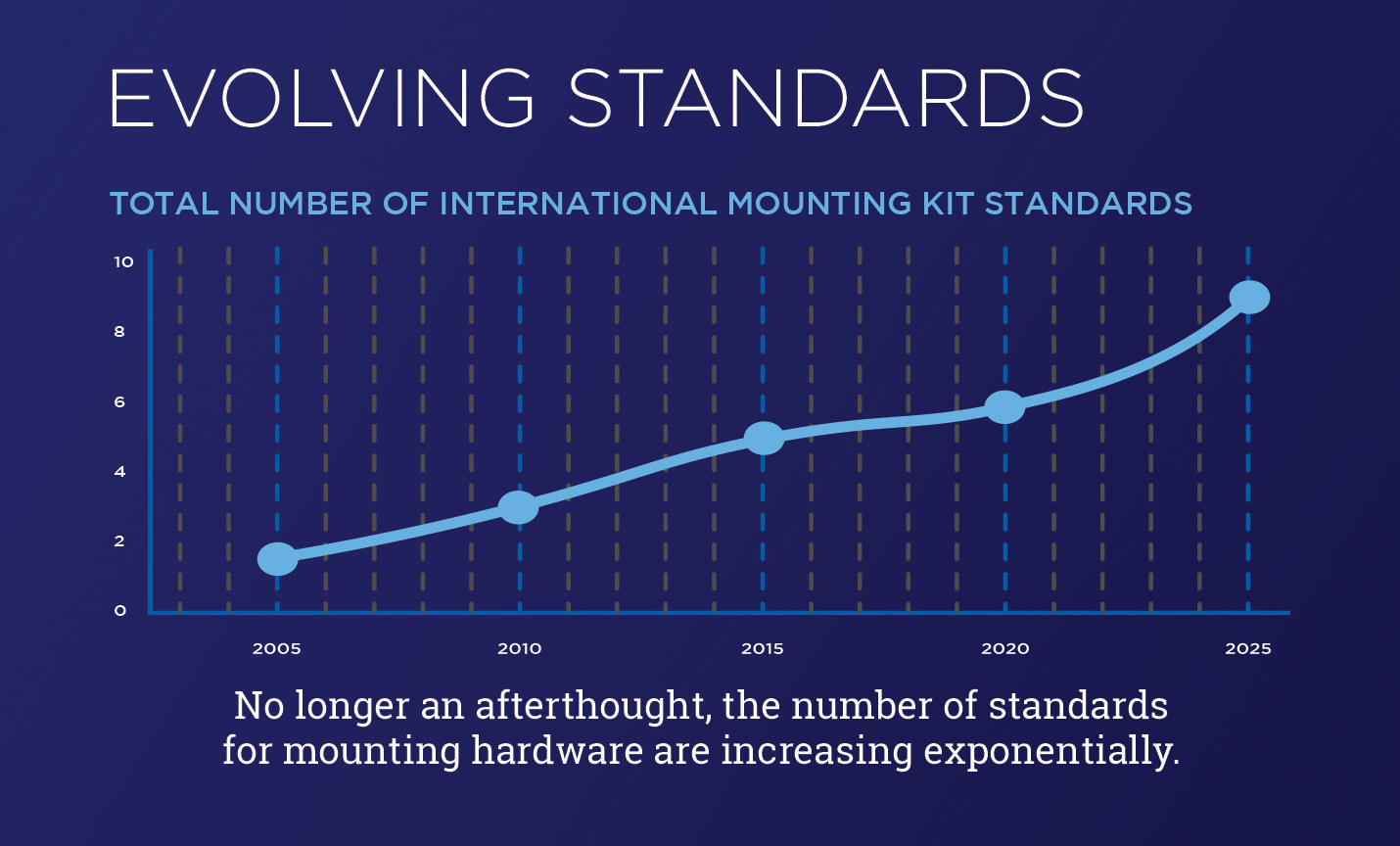