The use of Enhanced Leak Detection and Repair Programs (ELPs) has been in practice for over two decades. Oil, gas and chemical companies dedicate significant amount of labor and capital investment in an effort to ensure that they are in compliance with the Clean Air Act regulations. Despite these efforts, many manufacturers are subject to enforcement actions, from the U.S. government, in the form of consent decrees, if a non-compliance situation should arise.
According to the EPA, as of 2012, roughly 95% of oil companies and 12 chemical companies have ELPs. Although prevention of fugitive emissions is the most cost effective solution to prevent ELPs, as paying fines for noncompliance and the requirements detailed in an ELP are expensive to implement, attaining regulatory compliance is challenging. Despite the implementation of rigorous work processes and a company’s best intentions, manufacturers can still end up with an ELP.
This process therefore raises the questions, what is the most cost effective way to manage this type of consent decree or ELP? And, can the solution to this problem be optimized, so compliance and committing the appropriate resources needed to be successful are balanced. For example, which functions are critical and how many people from each area of the critical departments need to be involved? How many from the plant, engineering, maintenance, purchasing, legal and Environmental, will make a successful team without over staffing it?

Processes to Manage ELPs
These questions can be answered based on successful key learnings and the manner in which a company decides to address it. One way in which to approach an ELP is to break it down the a into three phases.
Phase I
Phase I is primarily strategy oriented. Initially the ELP should be treated as any other project, with a step-by-step approach. Building an effective team is the first critical step, as assembling the appropriate personnel will set the stage for success. Converting the legal language of the consent decree into work processes and documentation everyone can understand is the second step. The third step, is to develop a communication and training plan. Finally, a comprehensive documentation system needs to be created which tracks who is accountable and where information is stored for audits and annual reports.
Phase II
Phase II is the most challenging. It is the implementation phase. A depth of experience with the EH&S regulations and low emission valve standards is critical for successfully avoiding non-compliance when low emission components are required. Engineers, maintenance personnel, and others who can purchase seals, valves, and gaskets should have a comprehensive understanding of low-e qualified technology and how it will function in the service in which it is placed.
Knowledge of low-e qualified technology is essential, as major issues can arise when there are qualified low-e products commercially identified and available that are not compatible, or do not perform, successfully in a certain service. This is an area where the probability of noncompliance with the ELP language is higher. The ELP will most likely force the company to search for qualified low emission components availability, such as valves and packing. Then a decision must be made to see if they can be placed into the specific service, based on good engineering principles and safety considerations. An ELP should have commercially unavailable provision language. Plant personnel must know the past successes and failures of a component so this exemption can be claimed and documented when applicable. For example, if a valve has been qualified to meet low emission standards, but the seating capability does not meet shut off sealing requirements, or the valve packing that was tested for low-e certification is not compatible with the service, then it should not be installed. If there is a non-qualified low emission valve that will suffice, then it can be used under certain provisions but, there must a record of why this non low-e product was put into service. Other design considerations that must be identified when comparing low-e standards and non-low-e standers are, valve styles, pressure drop through a valve, actuation performance, and product temperature rating. The important aspect here is to keep a record of the decision process and make it a permanent record. It is also required to document that low emission products were unavailable. Once actions are taken to ensure all of these potential issues are addressed, and resolved, it is equally important to ensure that the correct components are purchased and installed. Every individual who can order a component under an ELP must have access to the documentation so they know what to buy, and in some cases, the tagging and monitoring action associated with it once it is installed.
Phase III
The function of phase III is to ensure that these practices are in place and sustainable for long term. This can be accomplished by carefully ordering specified equipment and components and adding these requirements into the company technology standards documentation. The intent of an ELP is to make the improvements permanent. The new low emission requirements must be sustained before termination can occur.

Additional Steps to Consider
Prepare for personnel turnover. Consent decrees can last a long time, five years minimum, and most much longer than that. People will change roles. The experience and knowledge an individual develops working on an ELP is not easily or quickly passed to the next person. Proper planning and timing considerations will be required to get the next person up to speed, and ensure compliance and consistency. Management also must recognize the importance of the work being conducted by the employees who deal with these issues. ELPs are costly to a company, and a drain on resources. If management overlooks this work, or does not sees the importance of it, the ELP team will not be effective, and the program will continue until the government directed audits stop finding non-compliance issues. Leadership needs to put the best personnel on it, strive to finish on time, and reward the people who were successful at avoiding any additional costs.
Final Thoughts
This process is a proven methodology and identifying the key individuals for these roles will make an effective and efficient team. Complying with the extensive and complex legal requirements can be daunting, especially if it is new to your company. Fortunately a refinery or chemical manufacturer does not have to go it alone or blaze new trails.
There are companies and individuals, with lots of experience, available to help guide you through this enhanced regulatory process. Many of the companies providing these services are active and accessible in industry symposiums and conference.
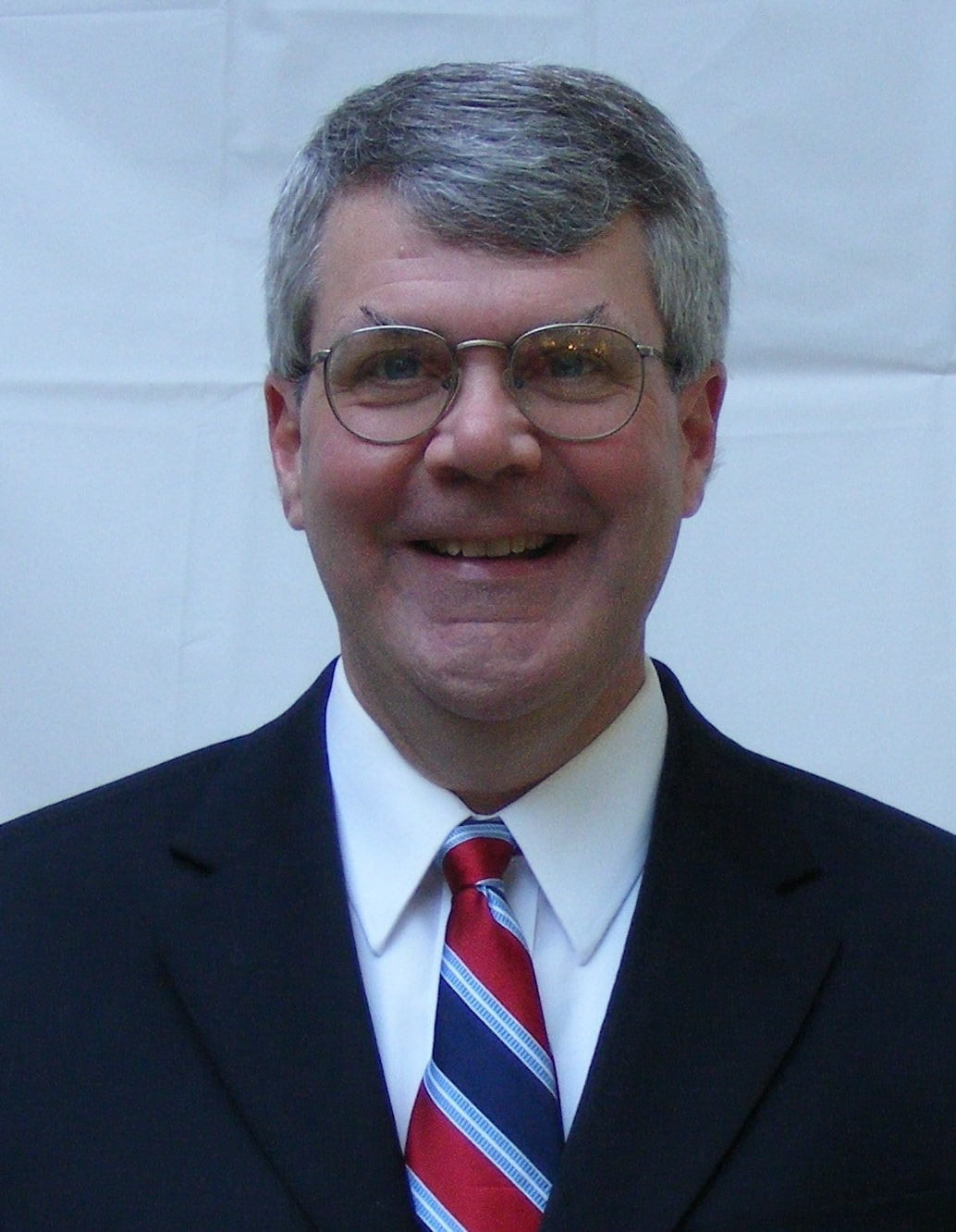
Dan DeVine began his career in 1987 working for the Union Carbide Corporation after graduating from the University of Iowa with a Bachelor of Science degree in Chemical Engineering. He joined The Dow Chemical Company in 2001 through the acquisition of Union Carbide. Dan recently retired from DowDuPont and is now working in a valve and piping consulting engineer role as an independent contractor through Midland Engineering, Ltd. He has worked in multiple chemical manufacturing industry roles including production, chemical distribution, with the majority of his time spent in engineering design and project functions dealing with valve, piping, and pressure vessel technology. He was the Valve and Sealing (Packing) Technical Resource Leader at The Dow Chemical Company, when he successfully implemented a low emission valve and packing program for an ELP at the Midland Michigan Operations Site.