It is clear from the outset that Rajan has had an interesting career. After completing his Masters’ degree he began working for the Atomic Energy of Canada, but with the recession that was occurring at the time, life in the United States appeared far more appealing. He relocated to New York, where he spent 9 years working for a nuclear and conventional power plant EPC, before eventually moving to the Middle East in 1978 to begin working for oil giant Saudi Aramco. Rajan acquired 20 years of experience working as a Valve Subject Matter Expert (SME) and while he joined the company during the early days of the oil boom, by the time he left Saudi Aramco were producing almost 10 million barrels per day. “It was a great experience working in Saudi Arabia,” says Rajan. “It felt like what it must have been during the California Gold Rush of 1848. There was a shortage of all materials and one had to scramble to even get a TV. Nevertheless, watching Aramco and Saudi Arabia develop and grow by leaps and bounds was unforgettable.”
Now, Rajan has decided to use his expertise to assist other companies and organizations. Currently, he has two consulting agreements, one with Forum Energy Technologies/PBV Valves in Stafford, Texas, and one with Process Industry Practices (PIP), a standards development organization (SDO). Rajan describes his typical working day: “I work at PBV four days a week from 8 to 12 noon and then fit in my PIP assignments (about 6 hours a week average) at home wherever I can – between my social and volunteer activities. Right now, I am helping PIP to develop and update their piping and pipeline valve specifications. The organization has about 70 members who participate in harmonizing their standards. In this sense, companies can minimize expenses on their own standards as they can use PIP standards and add or subtract to them.”
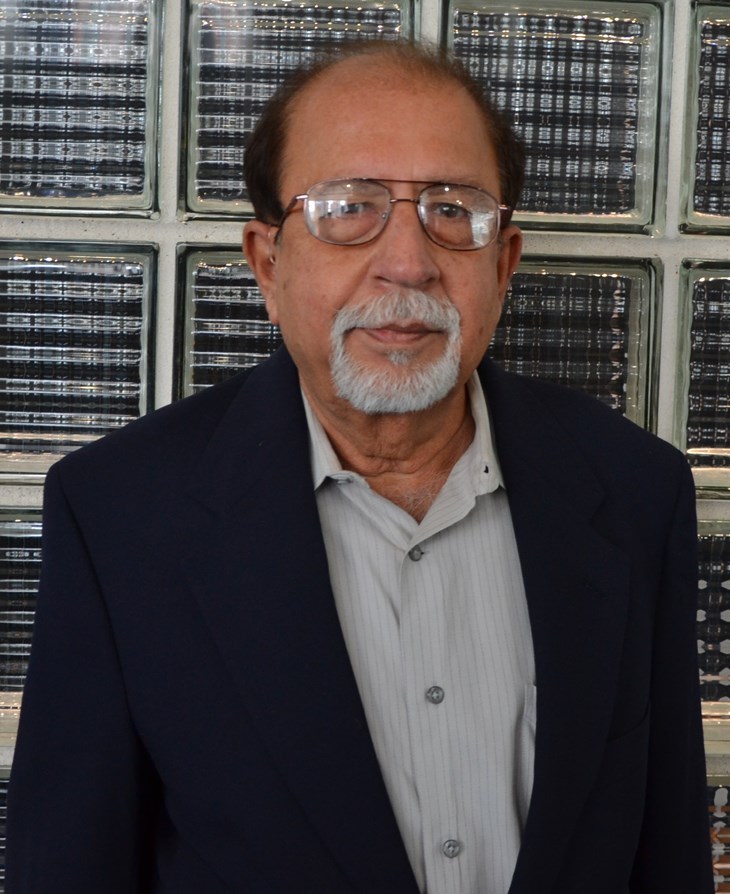
With his role as a consultant, it is evident that Rajan has to keep up to date with new trends and innovations. PIP already has 1200 valve descriptions, but as Rajan explains, one of the main priorities is to ensure that they are current. Just like other SDO’s, PIP has to take a look at a at all specifications every 5 years on a rotating basis in order to maintain their relevance and accuracy. “There is a member company review cycle and a steering committee review cycle before any changes or additions can be published,” adds Rajan.
At PBV, his assignments are varied and range from reviewing client specifications to providing support to a new valve manufacturing facility that is in the process of being built in Saudi Arabia. The facility will manufacture ball valves ranging in size from NPS 2 to 36 and will serve the needs of Saudi Aramco, SABIC, SADARA, ADNOC, KOC, PDO and other companies in the Gulf region. “It is very exciting to actively participate in such a creative worthwhile project virtually from the ground up. It is a win-win proposition because it will provide opportunities for local employment and serve the valve needs of the Gulf region, as well as provide a path of growth for PBV. Saudi Aramco has welcomed the project and is providing strong guidance as is their policy for new local start-ups. I’ve got my fingers crossed that this project will be up and running soon, and will be a role model for others contemplating investment in Saudi Arabia” says Rajan.
Influencing an Industry
In addition to influencing industry standards through current active participation in the API Subcommittee on Piping & Valves, Rajan influenced development of company valve standards when he first went to work for Saudi Aramco in Saudi Arabia. As the Middle East were still in the early stages of growth, Rajan had the opportunity to upgrade standards and educate young engineers. “When I first began working at Saudi Aramco, valve specifications were either non-existent or ”over-burdened”. We had a lot of work to do to make the standards more cost-effective,” explains Rajan. “I also had a number of trainees over the years, and this was the company’s number one priority – to train young Saudi engineers, so that one day they could take over, and which gradually happened over a period of many years. Not only this, but back in 1978 there were no valve manufacturers in Saudi Arabia. Now, there are about 10.”
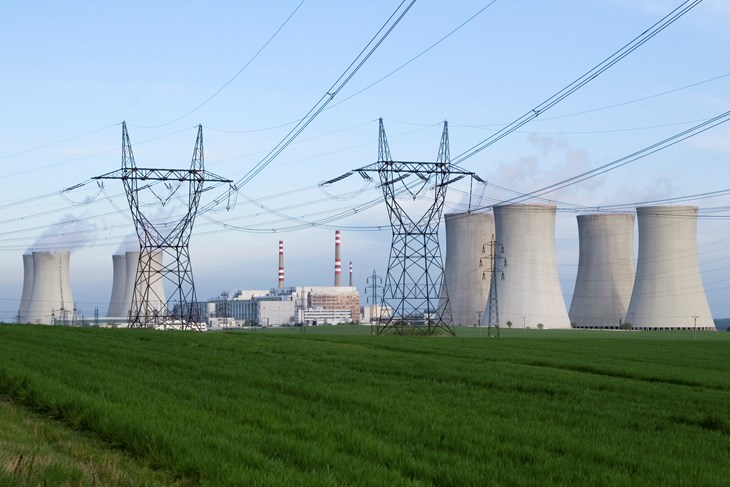
While it is clear that Rajan had a lot of responsibility while working for Saudi Aramco, he further describes the extent of his duties: “Saudi Aramco is a fully integrated oil company starting with exploration right up to shipping of the final product. Therefore, I was able to work with every kind of valve in midstream as well as downstream processes, starting from NPS 1⁄2 to NPS 60 in pressure classes up to API 10,000.” Again, he has used his previous experience to influence the industry, by proposing to “increase the scope every time an API standard comes up for revision.”
Keeping with the topic of ‘influencing’, we asked Rajan about the issue of transferring knowledge from experienced industry experts to newer engineers and how he had encountered this issue in his career. From Rajan’s experience, this did not appear to be a problem in Saudi Arabia, as one of his main reasons for being there was to educate a younger generation. There was a shortage of jobs and promoting local industries was a priority. How- ever, in the U.S., Rajan believes, the “boom/bust cycles” discourage people from returning to the industry. “It is an issue that needs to be addressed because we need to nurture these young engineers. I think most companies are beginning to appreciate the importance of doing this. When I was with Aramco in Houston, I trained a young engineer for 2 years before my planned retirement date.”
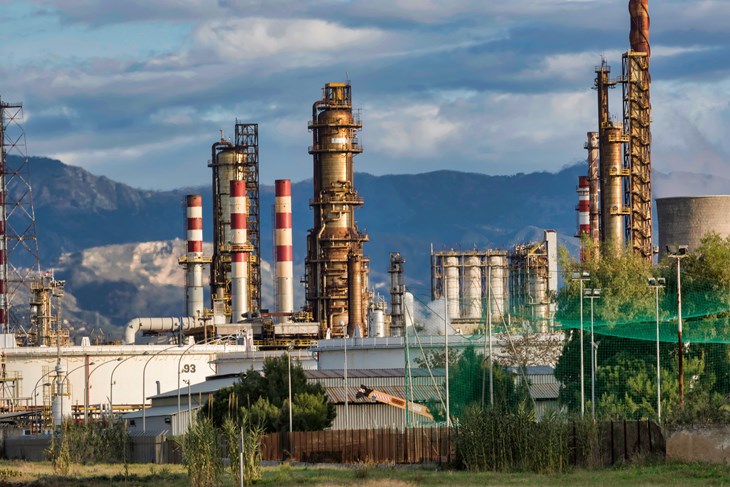
Quality Concerns
Rajan believes that quality has always been a major problem when it comes to valves. In fact, he states that 80 per cent of the time, if there was an issue with a valve, it was related to quality. “We would take it apart and find that it was not built the way it was supposed to be built. Or, it was built with such inferior quality that it was only a matter of time before it was going to fall apart.” With his work so revolved around standards, it is evident that Rajan believes quality is a key factor which must be maintained in the valve industry. If manufacturers denied responsibility for a poor quality product, they were no longer deemed suitable for the approved manufacturers list (AML). This issue of quality proves a huge concern for Rajan. With many customers wanting valves quick- er and at a cheaper cost, some unscrupulous valve manufacturers are willing to cut corners. “One of my fears is that the quality will get worse. I have seen a lot of poor quality in the field and I believe that what we need is a central organization that we can depend upon to govern quality,” says Rajan.