Manufacturing, Distribution and End Users
Manufacturing
Since most valve manufacturers are not brick and mortar factories today, the majority of manufacturing is done by offshore production factories. Some of the manufacturers do not own the factories, but only contract out their production to low-cost producing countries in Asia.
In contracting out production, manufacturers usually do not have their own teams of people on the ground in the factories. This is where the important role of a third-party inspection company, comes into play. A third-party inspection company becomes the manufacturers’ “boots on the ground”.
A true third-party valve inspection company specializes in valve inspections – they do not inspect any other industrial products, thus becoming experts in the field.
For the manufacturer, this brings value added quality on all aspects of their valves, all the time. In addition to inspecting, the third-party inspectors also give direction to the factories on how to make a quality valve. They also advise the factory where to source many items such as packing, gaskets, soft seat material, etc. As experts in the process of valve manufacturing, third-party inspectors have knowledge on ways to optimize the manufacturing process. Having the inspectors in the factories make for a win-win scenario. Valves produced are of the highest quality, and factories be- come more efficient and profitable.
Typically, a third-party valve inspection company for a manufacturer performs the following within the manufacturing process:
1. Closely inspects integrity of incoming castings.
2.Closely inspects the complete machining process and the assembly of the valves.
3. Witnesses chemistry testing by PMI of the major valve components.
4.Complete witness of API 598, 6D and any additional testing that the customer requires.
5.Conducts a thorough final visual inspection of the painting, packing and loading of containers.
In addition, the third-party inspection company qualifies subcontractors for the manufacturer, for the supply from foundry, forge masters and parts suppliers for the packing, gasket, ball, stem, stud and nut.
Distribution
The in-house inspectors from the distribution companies around the globe perform factory audits of manufacturers prior to that manufacturer being added to the distributors list of qualified valve manufacturers.
In many cases, after the first audit is completed, there are no follow up audits to verify that the audited factory is still qualified and keeping up with their Standard Operation Procedures, (SOP’s). There are no checks on whether or not factories are current on all of their ISO, API, etc., certifications.
Unfortunately, it is quite common for factories to pass important audits and then slip back into their old habits, undetected. Unbeknownst to the manufacturer, distributor and end user, factories on the distributors list of qualified valve manufacturers may not be qualified at all. A third-party inspector does the continuous follow up inspections to make sure the producing factory is following their quality manual and SOP’s to maintain being a qualified valve manufacturer.
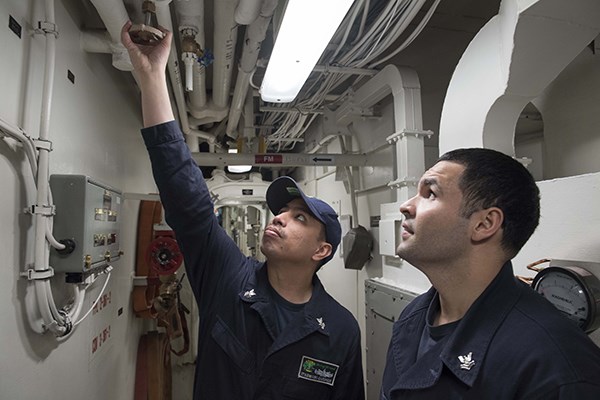
End users
End users perform audits at the producing factory of the manufacturer to determine if the producing factory is qualified to be added to the end users Approved Manufacturers List (AML). AMLs are factory location specific.
The end user sends engineers from their offices in other countries or con- tract out to one of the big inspection companies that inspect various industrial products. Typically they are not experts in the valve industry.
Once the audit is completed and the manufacturer and their factory have been added to an end user AML, that end user may not perform a follow-up inspection for some period of time, if at all. Some end users will not do follow-ups unless a situation arises that makes them question the manufacturer or the producing factory of the manufacturer. Having a third-party inspection company is important to do follow-up audits to verify that the factories are maintaining the proper procedures and maintaining the quality of the product. A third-party inspection company ensures that the factories are up to date and keeps the manufacturer, distributor or end user updated on the details of the manufacturer/factory significantly averting valve performance failures and also ensuring that the manufacturer/factory stay’s qualified and pass any re-audits.
AML audits are not only on the manufacturer/factory, but also their foundry, and forge masters. AML approvals are factory, foundry and forge master specific.
Factories will often sub-contract to have the castings produced at two or three different foundries. The third-party inspection company oversees and ensures that the producing factory is using only the approved foundries and forge masters. A third-party inspection company will have inspectors at the producing factory to ensure the castings are being made by the approved foundry and each casting is properly marked with the right foundry markings. This is to avoid any confusion when the castings arrive at the producing factory for machining.
Working with a third-party inspection company that specialize in valves, removes the risk in offshore production. They increase the status and attractive- ness of the manufacturer to its distributors and end users because the third-party inspectors oversee the entire manufacturing processes. The third-party inspection company monitors and confirms that all procedures and defined testing along with specific processes are followed every step of the way. This invaluable service provides all parties involved the quality assurance they are looking for in a quality manufactured valve.
About the authors
Gary Davis’ comprehensive and tenured business experience encompasses diverse industries that enabled him to develop fundamental business, management and leadership skills to compliment his entrepreneurial initiatives. With 30+ years in both the commercial and industrial business sectors, Gary is an entrepreneur willing to take calculated risk through applied management science yet grounded in common sense. In 2001, he launched a valve manufacturing business, Beric-Davis Companies International. Gary is co-founder of Industrial Manufacturing Verification Services.
Jordan Finn was first introduced to the PVF industry as a young boy, sweeping floors at his father’s warehouse. By the end of high school, he had worked his way through every aspect of the warehouse operation including receiving, filling, packing and shipping of orders and learned about machining, packing, gasket, and API 598 testing for gate, globe, check, and ball valves. He and his older brother took over the family business, which originally functioned as a master distributor of PVF products and ventured into manufacturing their own label – Warren Valve. Jordan co-founded Industrial Manufacturing Verification Services (IMVS) and works closely with domestic and international valve manufacturers on sourcing and qualifying foundries.