The “blowdown effect’ refers to the process of using blowdown valves to remove accumulated debris, sediment, or dissolved solids from Y strainers, steam traps, or boilers in a steam system. By relieving differential pressure and clearing blockages, blowdown valves maintain system efficiency, prevent equipment damage, and extend operational lifespan. In this article, I will address the importance of blowdown valves on Y strainers, steam traps, the role of Y strainers, and how they maximize steam system efficiency.
Travis Mosher, President – R.B. Mosher Co.
Blowdown valves are critical for maintaining steam system efficiency by enabling periodic and continuous removal of debris and other contaminants. The importance of blowdown valves in a system is derived from their ability to remove debris and maintain system cleanliness as well as prevent and relieve backpressure, which protects equipment, maintains system efficiency, and retains cost savings.
Case Study
An end user has a steam trap with an integrated Y strainer, such as a Pennant PT11 or a Watson McDaniel TD700S thermodynamic steam trap, which is backing up with water. If a blowdown valve is not installed, this steam trap may be damaged and will need to be replaced. The clogged strainer may also go unnoticed creating a 10 to 20% pressure drop, forcing the boilers to produce more steam and waste unnecessary energy. As a result, the user will see an increase in operational costs of 5 to 10% annually.
The solution is to add a blowdown valve for less than USD$100 per strainer. This will allow the debris to be removed from the system, relieving the pressure drop, reducing the strain on the boilers, and creating cost savings by salvaging the steam traps and eliminating expensive replacement costs. Regular Y strainer blowdown prevents screen damage, especially for delicate steam system screens (e.g., 1/32” or 20 Mesh). Blowdown valves are a low cost addition (when compared to potential damage or downtime) that prevent catastrophic failures.
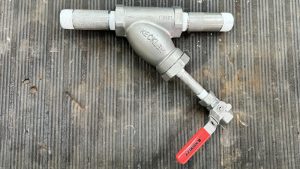
Why use Y Strainers?
Y strainers are essential components in steam, liquid, and gas systems, which are designed to protect equipment and maintain operational efficiency. This is accomplished by their flexible customization capabilities for nearly any application and ease of maintenance. They can also protect critical equipment and maintain system reliability. Y strainers are used for equipment protection on a wide variety of valves and equipment.
For example they can prevent diaphragm damage and seat erosion, protect small orifices in steam traps, and help pumps avoid impeller or seal damage from cavitation. They can also prevent tube blockages in heat exchangers and ensure accurate readings on flowmeters.
It is common for valve and equipment manufacturers to recommend or require Y strainers on the inlet side of their products, which prevent debris from damaging vital components. It can even be a condition to maintain equipment warranties. However, the blowdown valve is often left off during the initial installation. As the strainer fills up, the cleanout becomes a much larger task that requires isolation and complete screen removal that can increase maintenance costs and downtime.
Utilizing a blowdown valve to clear the screen will take a few seconds while a complete isolation and strainer disassembly may take half a day. The time savings alone pays for the initial cost of the blowdown valve and the lifetime savings can be many times greater.
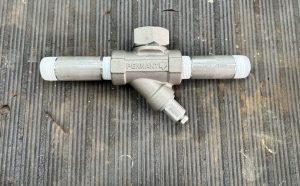
Screen Materials and Designs
The strainer screen material and design are as important. They determine the size of particles that will be allowed downstream. Being too tight or too open can be problematic. All pipeline strainers, valve integrated or stand alone, have the capability to modify the internal screen. This flexibility allows Y strainers to be customized for practically any application.
The strainer screen can be modified by changing the material, the opening size, and weave type. All strainer screens are standard in 304 stainless steel construction (1). Screen opening recommendations are based on pipeline media. Standard liquid systems typically require a 1/16” perforated screen whereas a steam or gas system requires a much smaller screen of 1/32” perforated screen or 20 mesh.
The size of the screen opening is based on downstream equipment and its sensitivity to foreign debris. Steam systems typically contain products that have smaller orifices than liquid systems. Therefore, they require a 1/32” to capture this debris and prevent orifices in the system from clogging and damaging the equipment. As the size of the screen opening gets smaller, the screen material becomes more delicate.
As a result, increased maintenance will be required to maintain its operation. Blowdown valves become more important for the lifespan of these delicate screens and mesh. It is recommended that Y Strainers installed on a steam system be blown down at least once per quarter to prevent increased backpressure or debris buildup. Blowdown valves are not standardized, and each type has it owns pros and cons.
Types of Blowdown Valves
Three main types of blowdown valves are available across a couple of applications. The most common are manual and automatic (or intermittent), and lastly, continuous. They can also be utilized outside of the strainers for boiler blowdown. Manual valves are the most common type of blowdown valves found on Y strainers, and they are typically ball valves, gate valves, or with steam traps – a screw type. The ball valve is the preferred choice and is the recommended type of valve for stand-alone Y strainers for its quick opening capabilities utilizing a quarter turn handle.
However, the ball valve is typically the second choice for most end users (when compared with the use of the gate valve). This is due to the common use of gate valves throughout most of these facilities. Even though the gate valve tends to leak and have a shorter lifespan, they are the most common type stored in maintenance supply rooms.
By standardizing gate valves, maintenance managers believe they can simplify their inventory and reduce stocking costs. However, increased steam leaks and failures are much more costly. Integrated strainers found on steam traps typically have their own special screw type of blowdown valve that is specifically designed by each steam trap manufacturer.
The screw type is a more durable design created to withstand the turbulence and temperature of steam trap strainer blowdown. Automatic blowdown valves can be extremely effective at maintaining the efficiency of a steam system as long as the condensate discharge is clear of any hazards.
An actuated ball valve is commonly utilized along with differential pressure indicators or RTDs that will send readings to a PLC where it will be interpreted and open the valve when the parameters are met.
These systems are costly on the front end but are safer and more efficient overall as they minimize personnel exposure and keep backpressure and debris to a minimum. Apart from blowdown valves on strainers, they are also present on the boiler. According to instrumentationtools.com, “Boiler blowdown valves’ primary function is to control concentrations of suspended and total dissolved solids (TDS) in the boiler”(2).
This is done with either an intermittent blowdown valve that utilizes an actuator like the automatic valves on Y strainers or a continuous blowdown valve. The intermittent blowdown valve is the most efficient. It will operate at predetermined intervals or when certain conditions are met. Continuous blowdown valves are designed to continuously discharge hot condensate and solids into a flash vessel to maintain the desired TDS in the boiler drum. These valves are less common on Y strainers due to constant media loss.
Boiler blowdown valves have a rugged design to manage the turbulent nature of 2 phase condensate discharge. They typically operate at least once per hour and as often as every 10 minutes. Boilers are the heart of any operation, but the surrounding steam piping can have a significant impact on overall water quality and system efficiency.
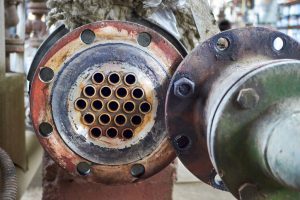
The Role and Importance of
Steam Systems
Industrial and commercial steam systems that require temperature control and mechanical work are becoming more commonplace for nearly all manufacturing, blending, and packaging processes.
These systems function at their highest efficiency when the steam is dry, saturated, and clear of any debris. Steam Systems are vital to numerous industrial and commercial processes. They play a critical role in sectors like power generation, food processing, petroleum refining, and chemical manufacturing.
Steam is commonly used for mechanical work like spinning a turbine for a power plant or heat transfer for use in steam tracing and chemical reactions. Steam is the most efficient media for heat transfer.
Steam allows for precise temperature control. When steam is dry and saturated, the pressure directly correlates to temperature. Less pressure, less temperature. Mechanical work and heat transfer both require steam that is clean and clear of any debris or moisture. Heat exchangers, steam traps, and control valves are easily damaged when debris or
water makes its way into the steam supply.
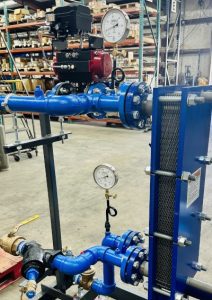
Clogged strainers can backup condensate, reduce header pressure and temperature. This makes Y strainers, whether stand alone or valve integrated, a critical line of defense as they protect more expensive and operation-critical valves and equipment from contaminants or debris, which can lead to premature failures and reduced heating efficiency.
For example, when a pipeline Y strainer on a steam system becomes clogged or begins to fill up with debris, a few changes begin to occur within the steam system and equipment surrounding the strainer.
As the pipeline strainer fills with debris, the differential pressure across the strainer begins to rise, reducing the pressure on the strainer outlet. The reduction in pressure lowers steam temperatures and increases the volume of steam in the line.
The increase in volume will cause velocities to increase and can reduce heat exchanger efficiencies by 5 to 10%. It also puts more strain on the boilers as the need for steam increases to overcome the additional back pressure.
This back pressure can cause water to accumulate in low points and elevation changes leading to water hammer. The lower steam pressure and temperature increases the steam system condensate load causing steam traps to cycle more frequently, heating times to increase, reducing their lifespan, and reducing overall system efficiency.
Blowdown valves on Y strainers and steam traps are indispensable for maximizing steam system efficiency. They prevent debris buildup, reduce backpressure, protect equipment, and ensure dry, saturated steam for optimal heat transfer and mechanical work.
Y strainers are critical for filtering contaminants and safeguarding vital components like control valves and steam traps. However, their effectiveness hinges on blowdown valves for easy maintenance. There are several benefits of incorporating manual, automatic, or continuous blowdown valves. For steam systems, quarterly blowdown, and proper screen selection (e.g., 1/32” for steam) are best practices.
If you’re designing or maintaining a system, prioritize blowdown valves to avoid costly failures and maintain peak performance.