Smart technologies including smart solenoid valves, wireless thief hatch monitors, and advanced redundant control systems improve process control and safety for oil and gas operations.
By Anne-Sophie Kedad, Global Director of Marketing – Discrete Automation, Emerson
Across the globe, oil and gas production companies are investing in new processes and technologies to minimize greenhouse gas (GHG) emissions and advance decarbonization efforts in their production wells, tank farms, refineries, chemical plants, and pipeline operations.
Globally, oil and gas operations account for 9% of all human-made greenhouse gases, according to data from the Organization for Economic Cooperation and Development (OECD). Reducing those emissions in a cost-effective manner will be essential for both the planet and the long-term viability of the industry.
This significant percentage of GHG emissions by the industry’s operations has led to increased emissions regulations by multiple governments and agencies. As a result, the global energy industry is upgrading its processes and integrating new control and monitoring systems to comply with these demanding and necessary requirements.
One area being transformed by these new control and monitoring systems is the industry-wide effort to minimize fugitive GHG emissions. Fugitive emissions, in most cases methane, are either unintentional or undesirable methane leaks or discharges from working wells, pressure containing equipment or facilities.
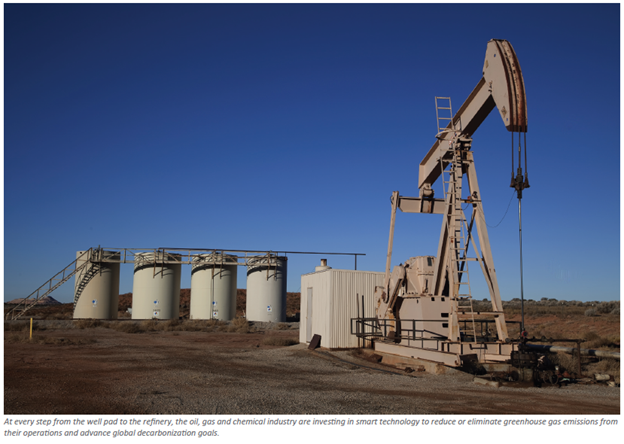
Technology to address fugitive emissions include smart, rugged solenoid-operated and electric valve systems for upstream oil and gas extraction designed to significantly reduce emissions at the well head and storage and separator systems. There are also reliable monitoring technologies that can help ensure thief hatches are locked on tank storage systems – a persistent source of fugitive emissions now subject to stringent regulations. Addressing fugitive emissions using these technologies can play a critical role in meeting the emissions reduction goals.
While preventing fugitive emissions is one-way companies are minimizing GHG emissions and meeting regulations, some are pursuing new opportunities altogether. Natural gas producers are using new solutions to safely ramp up blue ammonia production that uses more environmentally friendly blue hydrogen.
Through these technologies, oil and natural gas companies leverage smarter, simpler valve controls and monitoring devices at key “areas of opportunity” in the industry’s value chain, to identify, control and in some applications eliminate GHG emissions. Applying the right technology to these areas will ultimately have a dramatic cumulative impact on decarbonization efforts.
Significant New Regulatory Requirements
There are several recently adopted European Union and United States regulations designed to significantly reduce GHG emissions from oil, gas and coal mining operations. These new regulations have been developed by the U.S. and EU to fulfill their commitments to the Global Methane Pledge adopted by over 100 countries at the COP26 UN Climate Conference in 2021.
The Global Methane Pledge calls for the countries to adopt policies that will reduce their methane emissions 30% by 2030 compared to 2020 levels. As a result, the EU is drafting a binding 2030 reduction target aimed at cutting direct methane emissions from the oil, fossil gas and coal sectors, and from biomethane gas once it is injected into the network, as well as calling on EU member states to set national reduction targets.
The EU regulations envisage a complete ban on venting and flaring of methane from drainage stations by 2025 and from ventilation shafts by 2027 while ensuring safety for workers in coal mines. These stringent requirements would also obligate all affected operators to submit a report to authorities detailing the sources and levels of methane emissions for operated assets.
In addition to this reporting, operators covered by the EU and member state regulations must create a leak detection and repair (LDAR) program for their assets, conduct periodic LDAR surveys and must repair or replace all components found to be leaking as soon as possible. Also, since imports make up over 80% of the oil and gas consumed in the EU, it is also being proposed that importers of coal, oil and gas will have to demonstrate that the imported fossil energy also lives up to the requirements in the regulation.
There are parallel methane reduction regulations being introduced in North America. The U.S. Environmental Protection Agency’s (EPA) 40 CFR Part 60 includes extensive regulation of offshore and onshore petroleum and natural gas production and transport emissions. Included in that regulation are requirements for reducing harmful air pollution from new and existing oil and natural gas facilities.
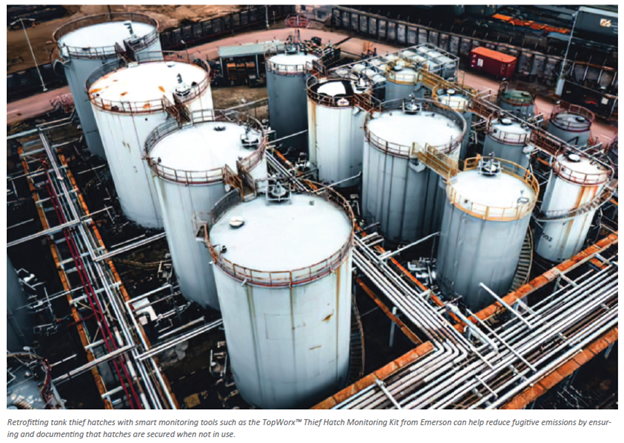
A significant part of that regulation directly impacts commonly used wellhead technology. It requires all new and existing pneumatic controllers at production wells and storage facilities have zero carbon emissions. Other North American emissions regulations at the state and provincial level are also calling for reducing the use of well gas-driven pneumatic devices and implementation of automatic pressure management and pilot light monitoring systems.
The industry is global, so regulations formulated in Europe and North America ultimately impact technology and infrastructure decisions in all production and processing regions. At the same time, oil and gas companies recognize that improving the monitoring and control of greenhouse gas emissions in their operations is essential if the broad goals of a net zero carbon future are going to be achieved.
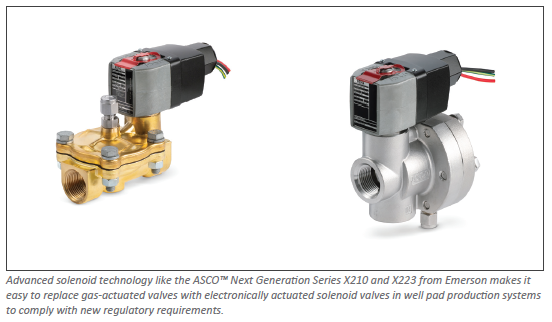
New Zero Emissions Valve Technology
A significant source of greenhouse gas emissions in upstream production has been essentially “built in” to standard operating processes at wellheads and oil and gas separator assemblies. It has been common to use the naturally pressurized methane produced by oil and gas wells as the media to actuate pneumatic components on wells and separators.
At one time, this made economic sense: rather than install and maintain electrically powered compressed air systems at these remote sites (where grid power is at a minimum), gas-actuated pneumatic valves offered a simple solution. However, gas-actuated valves come with an obvious environmental drawback: actuating the valves exhausts the methane into the environment. According to the EPA Greenhouse Gas Inventory, eliminating all gas-actuated pneumatic valves could result in a 25% reduction in all methane emissions related to oil and gas operations.
The oil and gas industry is exploring electrification to replace the gas-actuated valves at the well pad. Replacing these kinds of pneumatics with electrically actuated ones can help achieve targeted methane emission reductions and comply with the EPA regulations.
Leading valve technology companies are now offering solenoid valves that provide simpler and more reliable valve devices and have zero methane emissions. Some hybrid solutions use a three-way pilot valve that uses a generator to send compressed air to an actuator that opens and closes the valve.
Although this approach eliminates the methane emission, it requires multiple components and there are costs associated with running the compressor. Those costs can accumulate on well pad systems such as two and three phase separators and free water knockout drums with multiple valves. In addition, they typically demand more electricity than is available at many sites.
Simpler and more effective solenoid pilot valve solutions are also available. There are now solenoid valves that support a proof pressure of 5000 pounds per square inch (PSIs) and flow of 22.5 Cv with a maximum 1.2 watts of power. The combination of low power requirements and increased pressure and flow capabilities of new solenoid technology, provides an advantage over more complex three-way pilot valves with a single assembly, simplifying installation, providing quicker actuation, and eliminating possible points of leakage.
The low power design provides another important advantage: power can be supplied via solar cell, making it easier to implement the changeover from well gas pneumatics and providing a reliable pilot valve replacement that oil and gas producers can more rapidly implement to meet methane reduction goals and regulations.
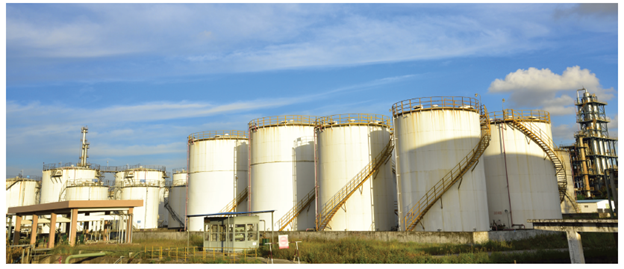
Smarter Monitoring to Control Thief Hatch Emissions
It is estimated that close to half of all greenhouse gas emissions in major oil producing basins are from oil storage tanks. In response, equipment companies and producers are installing better designed and tighter sealing thief hatches, which are points of entry that allow personnel to access the tanks for maintenance and other tasks.
While tighter sealing hatches are a good first step, even the best, most secure hatch will not seal if it is not closed.
Similar to well pads, most storage tank batteries are in remote locations where days may pass between site visits, and a manual visual inspection of the tank top to verify that hatches are closed and sealed is time-consuming and inefficient.
Regulatory attention is now focusing on unsecured thief hatches as a significant emission source that can be solved with the right tools. For example, regulations in place in Colorado and California require constant checking and documenting that each thief hatch is closed and latched – with some sites being fined up to USD $25,000 for every day an operator is unable to verify that all hatches are secured.
At the same time, the pressure in these storage tanks is subject to change, due to factors such as external temperature change or liquid level change from filling or removing liquid content. In order to maintain a safe tank pressure, special valves are utilized which are able to sense small changes in tank pressure. This kind of emission is permitted for safety reasons.
The challenge for tank farm operators is how to monitor tank farm emissions and confirm that they are from permitted venting and not from unsecured thief hatches – and how to do so in an automated and efficient manner.
Technology suppliers now offer wireless monitoring systems that can be retrofitted easily onto existing thief hatch and tank vent systems to accurately monitor both kinds of devices in real time. These reliable monitoring systems, engineered for use in outdoor environments, give tank farm operators the data they need to ensure that thief hatches are secured and are not the source of fugitive emissions.
With the wide range of thief hatch and latch configurations installed across the industry, it is important to select monitoring devices that feature modular designs that can reliably retrofit hatches using simple tools. This also minimizes the risks that false positives showing an unsecured hatch is fully latched.
Adding wireless monitoring to pressure safety valves complements thief valve monitoring by providing documentation that any emissions that do occur are the result of necessary safety release events. The data makes it easier for facilities to satisfy documentation regulations.
Ultimately, this kind of data can also provide oil and gas companies with valuable insights into the health and performance of these widely dispersed and sensitive storage systems. Many highly automated manufacturers in multiple industry segments are pursuing extensive digital transformation programs that leverage smart technology to improve their ability to capture and better utilize manufacturing and process data from across their operations to improve efficiency, productivity and return on investment.
This Floor to Cloud™ approach combines new sensors and smart valve systems to generate critical performance data. That data is aggregated and processed by edge computing systems for real-time reporting on production machine and line data; that same data is then shared in cloud-based analytics platforms for in-depth analysis and process improvements.
Insights on the condition of thief hatches, how often they are opened and closed, as well as data on pressure relief valves can be correlated with other data to help improve preventative maintenance practices, guide investments in tank farm replacement and upgrades, and contribute vital data on fugitive emissions reductions programs that oil and gas companies track for their decarbonization efforts.
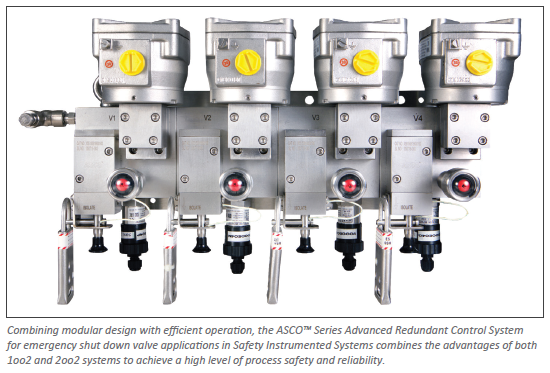
Safely Expanding Blue Ammonia Production
One of the key methods to help the oil and gas industry meet critical decarbonization goals is carbon capture, utilization and storage (CCUS). Carbon capture is the process of capturing carbon dioxide (CO2) emissions at the source, or directly from the air, preventing it from entering the atmosphere. Once captured, CO2 is then purified, liquefied, and utilized in other marketable industrial and commercial products.
A major marketable opportunity for this captured carbon is “blue ammonia”. Ammonia is manufactured by combining hydrogen and nitrogen. “Blue” hydrogen is produced from natural gas using a process called steam methane reforming (SMR) which has a much lower carbon footprint than traditional methods of producing hydrogen from methane.
Ammonia is heavily used in fertilizer production globally, so using blue hydrogen can help reduce ammonia manufacturing’s carbon footprint and help contribute to global decarbonization goals. In addition, with the surge of interest in hydrogen as a fuel, ammonia is an easily transportable to store and ship hydrogen. Hydrogen can be obtained by reconverting ammonia into hydrogen for use in applications such as fuel cells for cars.
Ramping up blue ammonia production presents technical challenges, particularly associated with safety. These facilities feature hundreds of critical solenoid valve systems. If those valves malfunction, operators may be forced to shut down processes with major cost impacts in lost production and time.
Chemical plants such as ammonia manufacturers must have Safety Instrumental Systems (SIS) with sensors, controllers and emergency shutdown (ESD) block valves that, combined with other plant monitoring and control systems, provides a multi-layered approach to operator and plant safety.
In many SIS applications, the solenoid valve remains energized in the open position during normal operation. To ensure the valve actuates in an overpressure or other hazardous event, valves need to be periodically actuated or “exercised.”
However, to exercise the SIS valve block can require downtime on a production line, and plant owners may resist this vital safety step. Fortunately, there are now advanced solenoid valve blocks that feature multiple valves in one block, so that each solenoid can be tested separately without taking the entire SIS system offline.
These advanced redundant control systems are now available in 2oo3 redundant solenoid valve piloting configurations. They combine the advantages of both 1oo2 and 2oo2 systems to achieve a high level of process safety and reliability.
These advanced valve blocks feature a direct valve-to-valve design that eliminates pipework and fittings that could be points of failure. They also provide visual status indication and feedback to facilitate maintenance and bypass options to allow easy online maintenance.
Expanding production of blue ammonia can help reduce ammonia production’s carbon footprint and advance the use of blue hydrogen in both fertilizers and hydrogen fuel applications. This expansion needs to be done safely and efficiently. Equipping these new plants with safety systems that can be used and tested without undue impact on normal operations can help spur the value of these new plants.
Decarbonizing Key Oil and Gas Processes
The oil and gas industry will continue to face major challenges as it seeks to meet worldwide decarbonization goals, satisfy regulatory requirements and still remain a profitable and valuable part of our modern industrial infrastructure.
The application of smart new technologies such as low wattage solenoid valves, thief hatch monitoring systems and advanced redundant SIS platforms offer valuable tools at key points from well head to tank storage to refinery and chemical plants.
Working with technology suppliers with deep understanding of the industry’s operations, process technology and sustainability challenges can help provide insight and proven technologies to keep finding innovative ways to help reduce emissions and sustain competitive value.