The world’s natural gas use is increasing at 2% per year largely due to expansions in LNG production. Valve sales for gas turbine systems are slated to grow at 4% per year due to the continuing replacement of coal and the prevalence of combined cycle systems.
By Robert McIlvaine, President & Founder – The McIlvaine Company
Gas turbines provide electricity and steam for electricity-generating plants, but also for oil rigs on floating platforms and food processing plants which create the biogas used by the turbines. Recent developments relative to fuels promise to accelerate growth. Gas turbines are now operating with 25% hydrogen and are being adapted to use 100% hydrogen. The advantage is the elimination of any discharges of CO2.
To eliminate the expense of shipping hydrogen long distances, ammonia is created and then converted to hydrogen at the turbine location. Also, ammonia can be combusted directly.
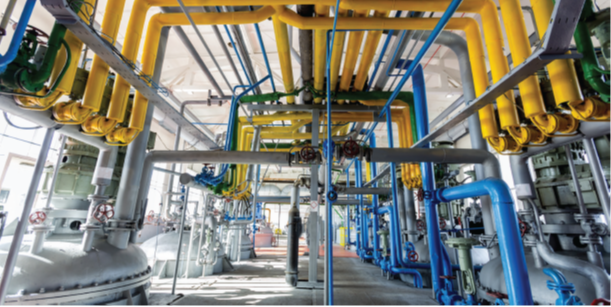
Another development is the sequestration of the CO2 formed during combustion. This makes the gas turbine process carbon neutral. In the case of food or other biomass waste from an energy plant, the turbine becomes carbon negative if the CO2 is sequestered.
All these developments require special valve designs. Valve manufacturers need to understand the ramifications of these process developments along with other increasingly popular options such as using treated municipal wastewater effluent for cooling and other purposes.
The value added by the valve manufacturer varies with the service.
The processes using valves can be segmented into the turbine combustion system, steam cycle, water and wastewater use, and air pollution control. The high temperature plus the criticality of valves in maintaining safety and performance result in 30% of the valves warranting a higher price due to the added value.

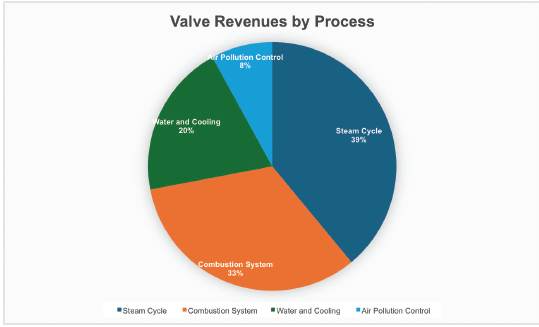
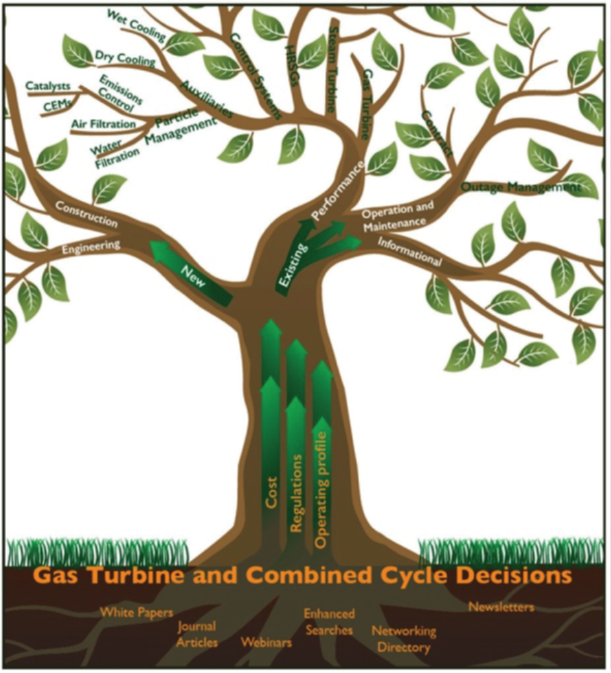
The valve suppliers also must understand the operator, hardware supplier, and consultant structure.
Most new valve purchases are replacements.
The largest turbine suppliers also provide O&M services which include valve supply.
Valves can cause fugitive emissions. Suppliers must understand some strange environmental rules. For example, a turbine operating in a non-attainment zone in Southern California must discharge air cleaner than the intake.
There are millions of useful facts and factors needed to guide valve manufacturers. This task is overwhelming and absent a systematic approach.
A systematic approach has been made available in the form of a knowledge or chard. First, one must locate each tree. Then one must locate the right branches, and finally, locate the low-hanging fruit.
Valve requirements are shaped by the decisions relative to all the main components.
The dependence of one component on another is illustrated by the combustion of hydrogen. NOx levels are increased, and selective catalytic reduction (SCR) is likely to be required. A number of valves are needed for reagents used in the catalytic reactor.
The advantage of organizing all the knowledge requirements as an orchard is the pollination from tree to tree.
For example, when MHI introduces a CO2 absorber with 99% capture instead of the currently considered limit of 90%, it impacts the valve outlook.
Parameters for the heat heavy recovery steam generator also dictate choices.

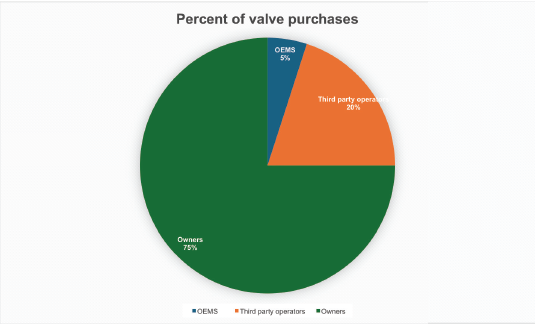
Over the last two decades, dry cooling has become popular in arid areas, but the energy requirements are substantial. Water reuse is increasingly popular. In addition to the lower consumption, it eliminates the time and effort to obtain water discharge permits.
The location is also a factor in valve selection. The cost of a service engineer flying out to an oil rig is substantial. As a result, at least one valve company offers more expensive but more rugged designs for these applications. Corrosion is another factor of concern on oil rigs.
Fuels introduce additional variables. What type of standby fuel will be made available? What degree of purification will be needed on-site for the alternate liquid fuel?
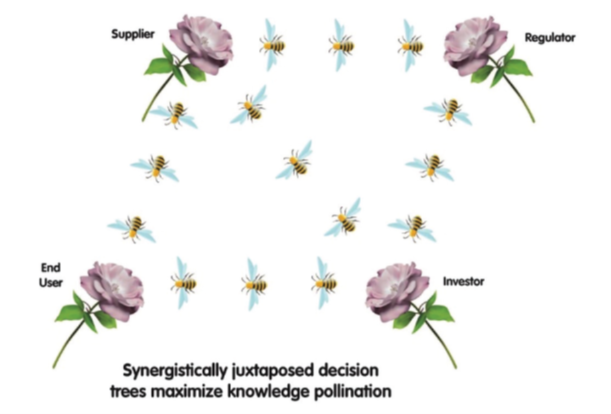
Gas turbine manufacturers frequently buy the valves used with the new systems they sell. For example, MHI, Siemens, and GE are the top three suppliers worldwide.
Heat Recovery Steam Generator (HRSG) suppliers also buy valves. Suppliers include turbine manufacturers along with HRSG specialists. Intake and exhaust system suppliers also include valves. Zero liquid discharge systems can be elaborate and may even include evaporators.
If valve suppliers systematically organize all the relevant facts and factors, they can pick the low-hanging fruit. They can add sufficient value to their offerings to warrant prices sufficient to achieve 30% EBITDA and 40% market share.