Most valve manufacturers can perform modifications to end user specifications at the time of order at their manufacturing facilities. While advantageous, this turn-key manufacturing solution can often result in longer deliveries. Thus, it is common for end users to pursue aftermarket modifications from a distributor’s valve inventory.
Valve World Americas had the pleasure of learning about aftermarket midstream valve modifications and testing of API 6D trunnion ball, API 6D gate, and expanding plug valves, from MRC Global’s Greg Peterson, Vice President of Production & Transmission Infrastructure & Gas Utilities VAMI.
By Angelica Pajkovic and Greg Peterson, Vice President – Production & Transmission Infrastructure & Gas Utilities VAMI, MRC Global
Valve Modification Considerations
Valve modifications are a critical consideration when specialized features on standard factory-delivered valves are required. Properly executed modifications to midstream valves extend the life of the valve and ensure that valves function properly in critical applications. End user qualification of a third-party modification service provider is therefore as important as qualifying a valve manufacturer. Modification service providers should be qualified and routinely audited.
For example, midstream pipeline transmission companies, gas utility companies along with liquid pipelines, tanks, and terminals often require technical valve modifications. End users with transmission and storage assets routinely bury pipelines with valves that must be upfitted according to buried service specifications. As weld-end valves used for mainline pipeline applications are soft seated, most end users require that pipe transition pieces be installed to match the pipeline design bore schedule and yield strength. These transition pieces or ‘pups’ can be installed in the field, however, it is highly recommended to perform this installation in a shop-controlled environment to avoid damage to soft seats during the welding process.
Other buried service applications require various stem extension configurations and buried service gears. Liquid pipeline, tank, and terminal end users may require Differential Thermal Relief (DTR) systems to relieve internal body cavity pressure from the thermal expansion of liquids. DTRs prevent over-pressurization by relieving excess body cavity pressure to the upstream or downstream side of the pipeline, as determined by an end user’s configurations. Many DTR arrangements exist and can include drain valves or media test accessibility features. Once modifications are completed, the valves must be tested to specification using acceptable testing equipment and procedures.
Finding Reputable Distributors
In North America, valve inventory is heavily positioned in the distribution market. This process brings valve inventory closer to the customer optimizing the speed to market. However, this creates a situation where aftermarket modifications must be sourced and executed to end user specifications. The options to service the modification need to include reputable distributors and wholesalers with in-house modification capabilities and/or third party modification shops and providers.
End user specifications must be written around the modifications required in conjunction with a formally approved shop facility. It is critical that modification providers meet the quality expectations for welding procedures and the testing of valves after the pressure-containing component has been opened; this is due to the valve being upfitted with additional features. Additional valves and components are utilized in modifications and should be supplied as per the end user’s approved manufacturer’s list (AML). Along with welding and testing, blasting, and coating of the valves are required for buried service or locations with a challenging environment.
In addition to the specifications required when providing aftermarket modifications, there are environmental and safety requirements to be considered. There are proper use and disposal protocols for the disposal of valve wash-down fluids and used test fluids. Modification service providers should have standards to make sure employees have proper work environments and go home safely every day.
When supplying quality customer-specified modifications, there are critical welding procedures and hold points on which end users must sign off before the provider can progress with the modification. The following is a review of some common modifications and recommended compliance practices used to meet end user specifications.
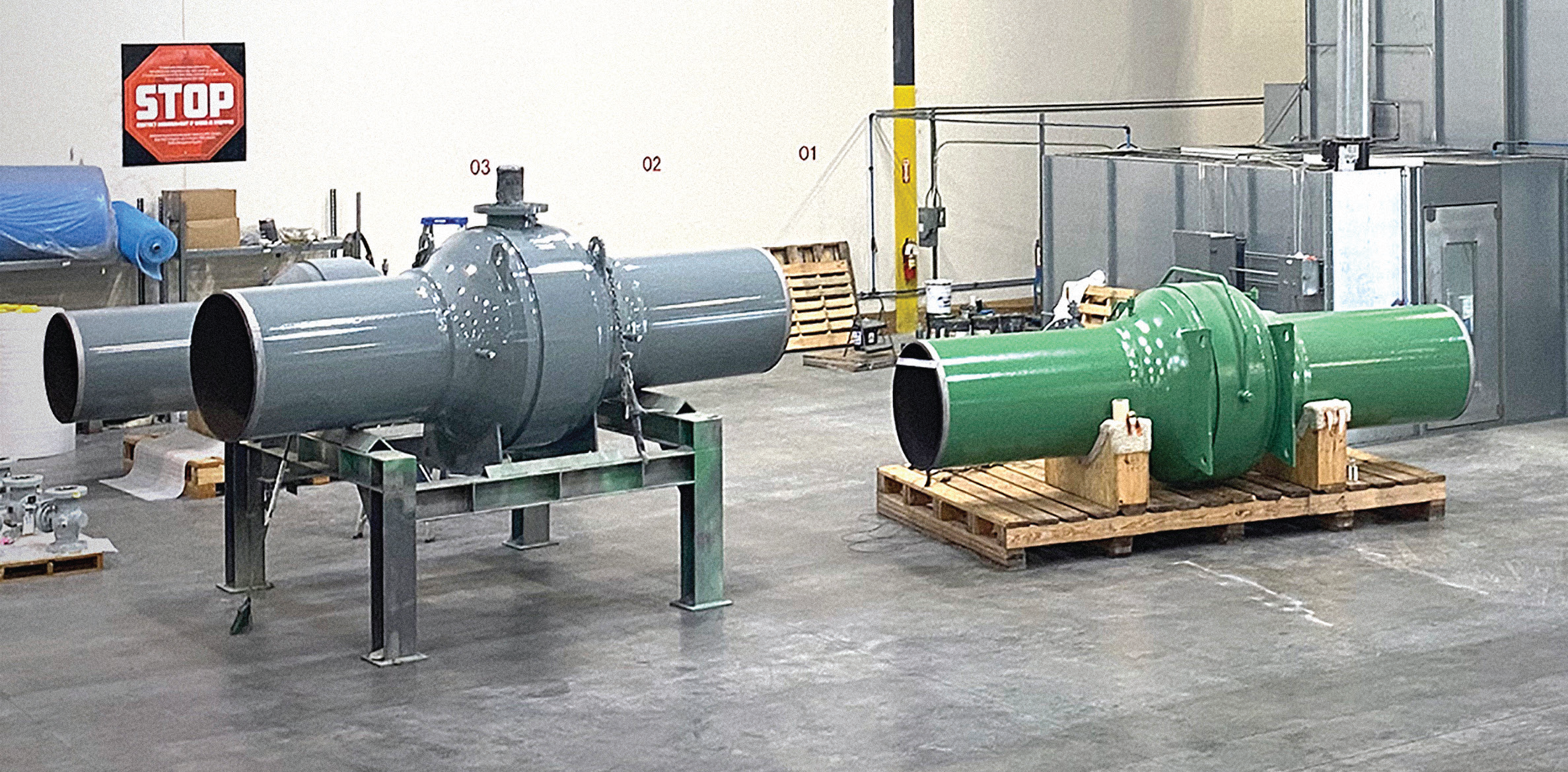
Common Midstream Valve Modifications:
- Pipe Pup Transition Pieces – Trunnion Ball, Pipeline Gate Valves, Pipeline Check Valves
- Stem Extension for Buried Service – Trunnion Ball, Pipeline Gate Valves
- Stub Up Modification – Trunnion Ball Valves
- Pinion Shaft Modification – Trunnion Ball Valves
- By-Pass or Pipe Away Configuration – Trunnion Ball Valves
- Differential Thermal Relief – Pipeline Gate, Expanding Plug Valves
- Blast and Coatings – All Valves
- Radiography or Dye Penetrant Testing
- Testing – Final Test and Inspection – All Valves Post-Modification
Pipe Pup Transitions Modifications
It is imperative to gather all information around design pressure, design temperature, design factor, bore schedules, and the yield strengths of a customer’s pipeline design. Critical hold points for the valve modification service provider should be identified in an Inspection Test Plan (ITP) to evaluate and provide this analysis prior to fabrication.
API 6D pipeline trunnion-mounted ball valves and API 6D pipeline gate valves, for example, are equipped with soft seats using materials like Nylon, Devlon, Viton, and other proprietary seating materials. When a valve is to be welded into a line, most end users require a pipe transition piece or ‘pup’ to be added to the valve in a controlled environment. The purpose of the pup itself is to allow for heat dissipation during onsite welding into the pipeline, which helps prevent heat damage to the soft seat material. Depending on the diameter and pressure class of the valve pipe, transition pieces can vary in length from two to four feet, with requests up to nine or 10 feet.
Barlow’s Formula relates the internal pressure that a pipe can withstand to its dimensions and the strength of its materials. The formula is P= (2*t*S/D), where:
- P = pressure
- t = wall thickness
- S = allowable stress
- D = outside diameter
Without proper engineering review of calculations, pup transition pieces could be installed with insufficient weld joint yield strengths thereby creating dangerous situations.
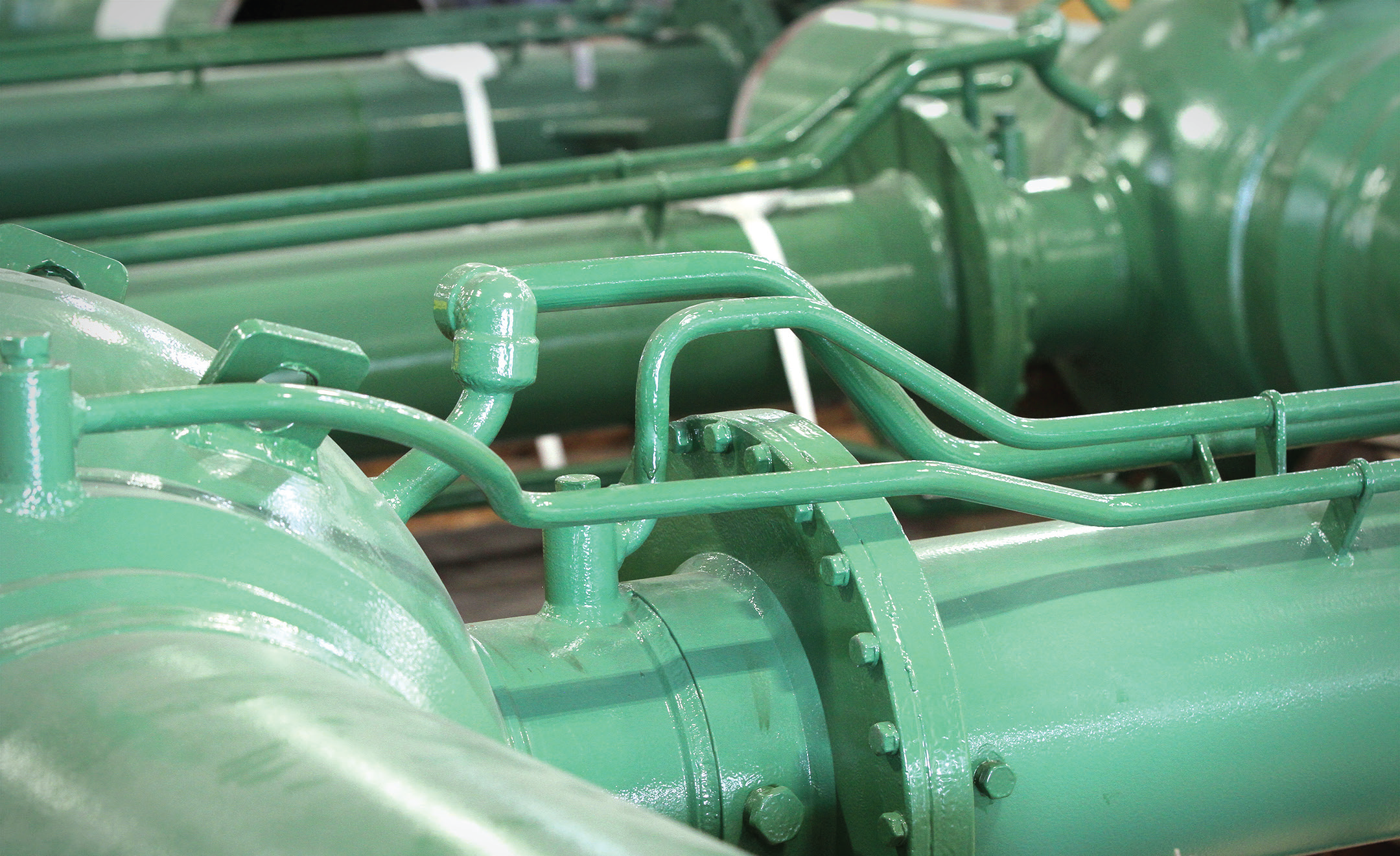
Once the pipe transition pipe welding is completed, the welds are radiographed (X-rayed) for defects confirming that the welding was executed properly. If defects are visible per the X-ray film, rework is required to eliminate the defects providing 100% integrity of the welding. Radiography must be executed in a quarantined area following strict guidelines.
After the pipe pup transition pieces have been installed, the valve can be tested per API 6D or extended duration testing as specified by the customer. This post-modification testing confirms the seat integrity assuring the valve will perform as expected once it is field welded into the line.
Stub-up Modification
There are often times when midstream or gas utility companies know they are going to need valves for buried service, but do not have the exact depth of the grade in which the valves will be buried. In these scenarios, they order valves with stub-up modifications. This modification includes piping the lube lines and vent/drain line to the top of the valve body and testing in a controlled environment. The valve is then shipped to the field where the stem extension is shipped separately), and field mounted to complete installation. This practice helps to keep the construction schedule on track.
Pinion Shaft Modification
For buried service applications that include pipelines underneath streets, parking lots, or concrete, a pinion shaft extension is often selected. Pinion shafts are used to make the valve operable from a utility access hole or valve vault. This modification includes affixing the gear operator with a pinion shaft at 90°, therefore extending the 2” square operating nut to a point where the valve can be operated at the desired installation orientation in the pipeline. Again, the lube and vent/sealant injection lines need to be manipulated for accessibility.
Valve By-Pass or Pipe Away Modification
API 6D trunnion ball valves are generally fitted with three different seat configurations such as double block & bleed (DBB), double isolation & bleed (DIB-1), and DIB-2. DBB is self-relieving (SPE) by self-relieving (SPE), DIB-1 is double piston effect (DPE) by double piston effect (DPE), and DIB-2 is self-relieving (SPE) by double piston effect (DPE). The variety of seat designs can be used to accomplish different levels of double block and bleed functional capabilities.
The modification associated with the DPE seat design, specifically downstream of flow, is a by-pass or, as they say in Canada, a ‘pipe-away’. A DPE seat configuration isolates body cavity pressure and does not self-relieve, thus a bypass is installed to manage an overpressure situation. The overpressure can be directed to a variety of locations including downstream. An inline relief valve can be installed and set to relieve at a specified pressure. This modification includes tapping the body or closure outside of the ball and seat area, then running a by-pass between the two with an inline check valve to relieve at a set pressure. Small diameter valves can be installed as well for seat integrity check functionality. Once the modification is complete, testing of the valve and by-pass is required.
Differential Thermal Relief (DTR)
Pipeline gate or trunnion ball valves and DBB pipeline plug valves require differential thermal relief systems installed to withstand thermal expansion in the body cavity. When liquid media, including crude oil and refined products, is trapped in the body cavity it can expand when temperatures rise through the course of a day. These overpressure situations are relieved through piping and a relief valve plumbed to a determined location including downstream of the valve setting. Pipeline gate valves are generally tapped and set up with a standard configuration from the factory, however, varieties of other configurations can be specified by the end user and supplied by an after-market modification provider. Once the DTR is retrofitted the valve must be tested for fitting leaks and valve functionality.
Testing and Inspection
Once a modification is complete the valve goes to testing and inspection. Many end users utilize a company inspector or a third-party inspector to witness test and inspect the valves post-modification. It is critical that radiography and pressure testing procedures are followed utilizing properly maintained equipment and tested to industry standards.
Valves with injection fitting extensions and drain extensions welded to the factory drilled tap in the valve body require dye penetrant be applied and visually inspected. Valves with pipe pup transition pieces require radiography and inspection with the x-ray results included in the documentation package provided upon completion of the valve assembly.
API 6D test standards are required as a minimum for hydro-testing and low-pressure air seat tests. Flanged valves can be tested utilizing test flanges or set-up in a test fixture specifically designed for the testing of valves. Final testing of a modified valve is critical and the difference between pass or fail can be down to the leakage of one or two bubbles.
Blasting and Coating
The final steps in the valve modification process are generally blast and paint. Reputable modification providers have tasked specific booths for blasting and painting/coating to control the environment where these services are accomplished. Valves prepared for buried service require blasting and the application of the customer-specified coating.
While blasting with sand or steel beads to remove factory primer, rust, or other unwanted surface materials seems like a straightforward process, it is important to prepare and protect vulnerable areas. The stem, packing journal, or stuffing box must be protected from the intrusion of blast media.
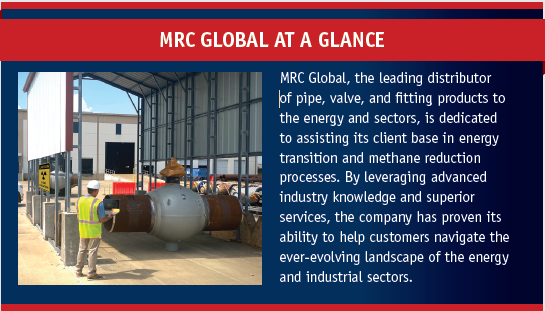
If a stem or packing area is accidentally blasted, the damage caused can be catastrophic to the operation and sealing capability of the valve. Flange surfaces must be prepped and protected from blasting as damage to a flange face surface can result in sealing issues. Even the valve manufacturer nameplates with the details of the valve should be masked to protect from blasting and damage-creating issues.
Once the valve is properly blasted, the coating or paint can be applied with proper adherence to the valve surfaces. Common coatings used for buried service applications require expensive specialized spray guns to properly apply the coating.
Application speed and the temperature of the material applied are also important factors for proper application assuring the required thickness and adherence of the coating.
Conclusion
The facility executing modifications to standard valves should be audited/ evaluated and approved by an end user to verify quality expectations are met. Along with a focus on quality, environmental and safety responsibilities should be evaluated for practice and implementation. Valve modifications are as important to qualify as the valve manufacturer itself.
Many valve distributors and third-party providers claim they have the capabilities to provide modifications, but providing quality modifications takes more than a welding machine and tube bender. Welders must be qualified, and test machines must be assessed and maintained for accuracy. Setting up and maintaining a reputable qualified modification shop takes expertise and expensive equipment.
Midstream end users should be conducting quality assessments and maintaining an approved ‘Modification Facilities’ category on their valve Approved Suppliers List.