Digital transformation of field instrumentation can spark one’s imagination with new concepts, including the possibility of data harvesting from automated on-off valves. Automated on-off valves are typically used in a basic process control system (BPCS) or safety instrumented system (SIS). In these and other automation systems, they must function properly to optimize performance, availability, and reliability. The data provided by smart on-off valves can be used to increase uptime, reduce maintenance costs, and improve safety.
By Riyaz Ali, Senior Director of Instruments, and Girish Dalbhanjan, Director of Global Engineering – Emerson
Automated on-off valves are typically used for starting and stopping batch processes, routing process fluids to different locations, emptying and filling tanks, backwashing and blow-back of filters, loading and unloading, engaging automated safety shutdown functions, and other applications. These valves are usually referred to as final control elements.
Considering the long lifecycle of operating plants in which they are installed, the valves must operate reliably for years to enable continuous production without interruption.
To improve operations, new plants are now being built with intelligent on-off valves featuring microprocessors and digital communication capabilities. Existing plants are similarly being modernized by replacing traditional electrical accessories with digital valve controllers or similar new technologies (Figure 1) and manual valves are being automated to gain added intelligence from sensors and actuators.
The value of these smart valve technologies will increase further as digital communications, Internet of Things (IoT) capabilities, artificial intelligence, machine learning, and other advances are used for remote valve monitoring, data collection, analysis, and predictive maintenance.
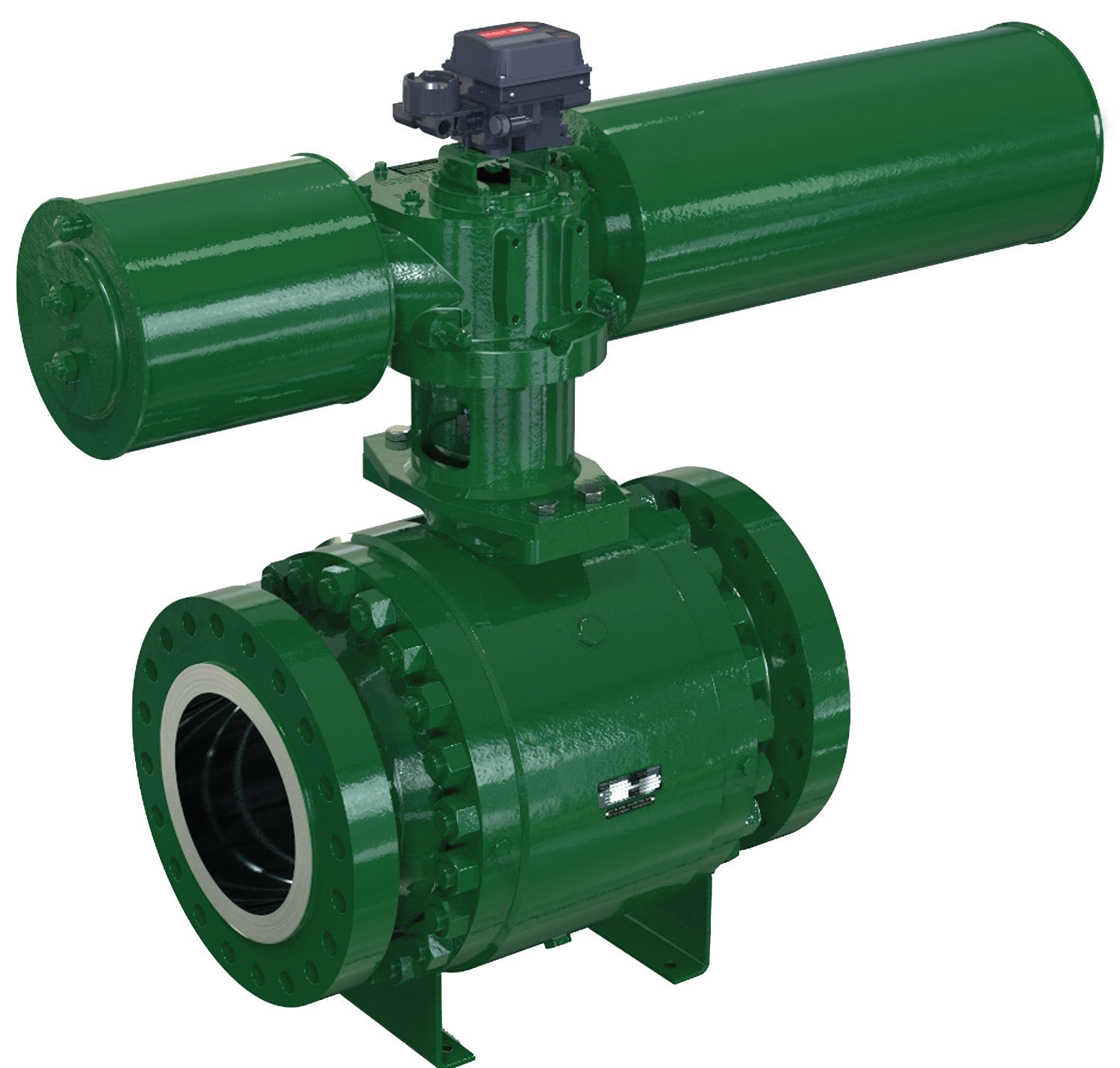
Issues and Risks
On-off valves are typically either air or electrically operated. Which operation system is selected based on requirements for flow rate, shutoff pressure, tight seating, fast stroking, leakage rate, and other attributes.
Traditionally, on-off valves were automated with a separate solenoid valve, two feedback limit switches indicating an open or closed position, and in some cases a position transmitter. The common challenge with the feedback limit switches and position transmitters was their significant alignment and mounting issues.
Now, if an on-off valve does not have onboard intelligence and communication capabilities, then regular preventive maintenance must be performed locally to avoid failures. Growing economic pressure and staffing issues make onsite preventative maintenance difficult, increasing the need to monitor valves remotely.
On-off valves are generally assembled by either the actuator or valve body vendor or by a third-party integrator. In some cases, this may result in an assembly that limits the ability of plant personnel to achieve operational excellence. Additionally, these valves often remain in one position for long periods of time, so there is always a concern that they will not actuate when called upon.
Typical issues seen over time include:
- Actuator failure.
- Insufficient shut-off pressure for actuator operation.
- Increased packing friction.
- Packing leaks.
- Valve body connection issues, such as shaft wind up, backlash, and stiction.
- Spring failure.
- Trim failure.
- Insufficient torque.
- Motor overloading.
- Problems related to excess temperatures and pressures.
Most of these issues are related to degradation over time, which is a mechanical phenomenon. These issues may accelerate and become more acute, depending upon the type of process fluid, pressure, temperature, operating history, environmental conditions, and other factors specific to each application.
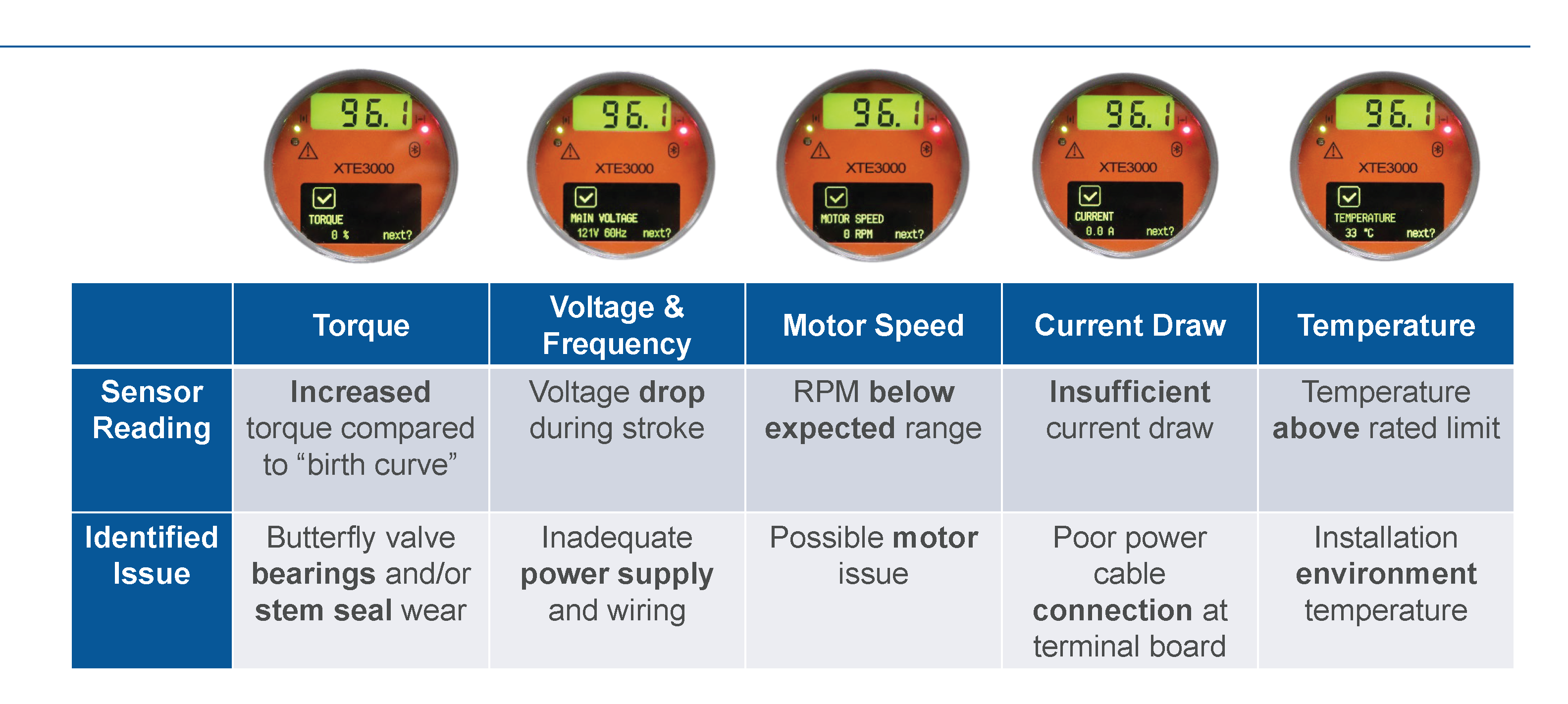
Addressing Issues with Digital Solutions
An on-off valve equipped with a digital controller can be used to mitigate or eliminate many of the common issues (Figure 2). These smart devices can be used with sliding stem, rotary, quarter- turn, and other types of on-off valves. The actuator can be single- or double-acting, with direct or reverse action.
Most digital valve controllers require only a single pair of wires for connection to and communication with a host—such as a BPCS, a SIS, and/or an asset management system—using communication protocol like HART®, FOUNDATION Fieldbus, or others. The HART two-wire connection also provides loop power, so there is no need for a separate source of electrical power.
With the advent of digitalization, microprocessor-based digital valve controllers aid in predictive maintenance by providing the information needed for valve health analysis. This is especially important for critical on-off valves in control and safety applications because the information provided can be used to increase uptime and optimize maintenance.
A digitized on-off valve with an intelligent valve controller can communicate information related to valve health, including:
- Valve seat integrity.
- Erratic valve performance.
- Worn valve components.
- Actuator problems.
- Overall integrity of valve assembly.
- Friction data, from which packing condition can be inferred.
- Leakage in the pressurized pneumatic path to the actuator. Valve sticking.
- Incorrect bench settings for diaphragm or piston actuator springs.

- Buildup of process fluid material on a shaft.
- Seizure of the shaft.
- Fracturing of valve shafts or stems.
- Actuator stem/shaft bending.
- Corroded bearings.
- Actuator spring rates.
- Broken springs on the actuator.
- Springs setting permanently in one position.
- Dented spring return actuators, which do not allow valve travel.
- Ball seal breakaway friction.
- Slow air exhaust.
- Blocked air exhaust paths.
By digitizing the actuator on a pneumatic on-off valve, advanced diagnostics can be provided to supply additional information, including the following online information:
- Travel odometer.
- Time closed/open.
- Time near closed.
- Stick slip.
- Spring range.
- Error offset.
- Rms error.
- Obstruction detection.
- Calibration error.
They can also provide the following offline tests and results:
- Ramp Test: hysteresis, deadband, accuracy, and linearity.
- Step Test: overshoot, response resolution, and dead time.
- Signature Test.
How They Function
Online diagnostics for electric actuators refer to the process of monitoring and assessing the performance and health of electric valve actuators remotely (Figure 3). It involves using advanced sensor technology, data analysis, and secure communication systems to gather real- time data from the actuators, and then analyze it for diagnostic purposes. This allows for early detection of potential issues—such as overheating of motors, increased torque, voltage drop, motor speed issues, abnormal behavior, wear and tear, or malfunctions—without the need for local physical inspection. These online diagnostics offer several benefits, including:
Early fault detection:
By continuously monitoring the performance of pneumatic and electric actuated valves, any anomalies or deviations from normal operation can be identified promptly. This enables timely intervention and maintenance, reducing the risk of unexpected failures and downtime.
Predictive maintenance:
Online diagnostics provide insights into the condition of the valve actuator assembly, allowing for predictive maintenance scheduling. By analyzing data trends and patterns, maintenance activities can be planned proactively, optimizing equipment performance and minimizing costly unplanned shutdowns.
Remote troubleshooting:
With online diagnostics, experts can remotely access and analyze the data from on-off assets, facilitating remote troubleshooting and support. This can save time and resources by eliminating the need for on-site visits, especially for valves installed in remote or inaccessible locations.
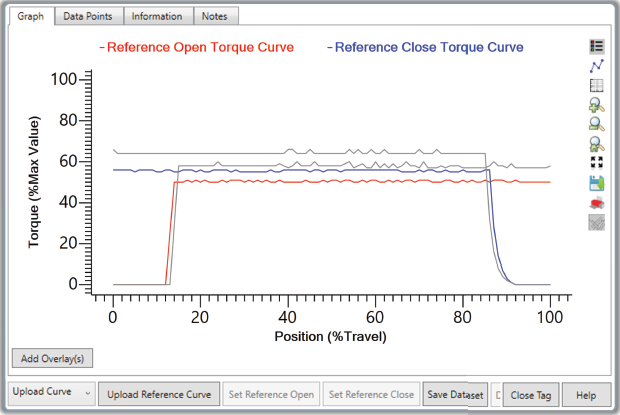
Performance optimization:
Continuous monitoring and diagnostics empowers operators to identify potential performance optimization opportunities. By analyzing data trends and identifying inefficiencies or suboptimal settings, adjustments can be made to improve the overall performance and energy efficiency of the actuators.
For example, Figure 4 shows a divergence between the reference and actual torque curve for both opening and closing, indicating a possible issue associated with actuator and valve assemblies. The degradation in torque while opening and closing can be an indication of valve, actuator components such as (electric motors, gearbox, drive train, etc.), or other issues. This type of chart can help trigger service or maintenance in advance of damage or failure.
Data-Driven Decision-Making
Online diagnostics generate valuable data that can be used for analysis and decision-making. The insights gained from the diagnostics can help in optimizing processes, identifying potential areas for improvement, and making informed decisions regarding maintenance, replacement, or upgrades.
Overall, online diagnostics of valves and actuators provides enhanced reliability, reduced maintenance costs, and improved operational efficiency by leveraging data and technology to monitor and diagnose the performance of valves and actuators in real time.
Digitized on-off valves also provide benefits during turnarounds, a period when time and resources are typically limited. Digital valve controllers can provide a valve signature without the need to pull the valve. This data provides the information required to decide if a valve needs to be pulled, or if the required maintenance and repair can be done while the valve is installed.
A valve signature performed on a new installation provides end users with a tool for future comparison of performance degradation over time, and it can also be used to create a benchmark for a rebuilt valve after a turnaround.
Future Trends
Most traditional on-off valves do not support digital communication protocols, but the trend is for them to eventually share the same digital communication network as control valves, motor operated valves, and other field instruments. On-off valve and other asset monitoring will eventually be performed via a two-wire network connecting multiple assets and sharing the same new protocol, such as Ethernet-APL.
Many plants have already invested in process historians, which record and report historical data from field devices and processes over time. Also, most commercially available process historians support Open Platform Communications (OPC) Historical Data Access (HDA). OPC-HDA allows real-time data to be gathered directly from the historian, with no additional load on the control network. Additional diagnostics also may be available from an alarm management or condition monitoring system.
Field device diagnostics are a key element in optimizing plant performance, which is directly related to productivity, efficiency, throughput, product quality, and optimal use of maintenance resources. These diagnostics can help turn a reactive/preventive on-off valve maintenance philosophy into a predictive one that will improve plant avail- ability, increase uptime, lower maintenance costs, and improve safety.
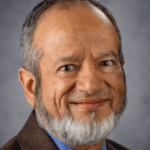
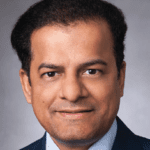