For those interested in entering the oil & gas industry, or those who are currently in it, it is helpful to note the core values of a plant. To gain a better understanding of the processes and procedures that take place in a facility, Valve World Americas had the opportunity to speak with a Maintenance Director at a mid-size refinery in Rocky Mountain Region.
After gaining a wealth of past work experience in the industry and a unique perspective on best practices and innovation, the Maintenance Director was able to provide essential insights into the oil & gas industry. He indicated that his methods and practices are guided by five core values: do not hurt anybody, do not spill, do the job right the first time, give people positive work experiences, and an hour’s pay for an hour’s work.
By Angelica Pajkovic
Five Core Values
1. Do Not Hurt Anybody
The first of the five core values is simple: do not hurt anyone. The Maintenance Director noted, “There is a whole lot that goes into that statement, from good procedures and personal practices to the front line Supervision’s behaviors. We always want to mitigate risk to avoid injury.” To do the job right, it must be done safely.
One way to ensure safety is to have different safety programs for each department, such as electrical and mechanical. “It takes a lot of time to complete these training programs, but they are well worth the effort. Addressing actual skills and tangible techniques is one key way to ensure employees’ safety on the job.”
The maintenance director makes an effort to bring in specialists for training whenever possible, such as welders who can discuss specific troubleshooting techniques and the intricacies of metallurgy. All these training programs can ensure fewer workplace hazards.
2. Do Not Spill
In addition to human injury, workers need to be aware of how their actions might damage the environment, so the second core value that the Maintenance Director lives by, and tries to instill in his team, is to avoid spills. “I am a bit of an environmentalist, and I think in my position in a refinery, I can help the plant run as environmentally conscious as possible. I am in a position where if something spills, I can help get that cleaned up right away. We can minimize the risk of spilling products through our maintenance work practices and by reducing the number of times maintenance has to be performed, meaning fewer breakdown events and less rework.”
Preventive maintenance is common in many workplaces, but especially in refineries and chemical plants. “Preventive measures should be standard in every refinery, but unfortunately that is not always the case”.
3. Do the Job Right the First Time
Doing the job right the first time requires having the right tools, facilities, knowledge, time, and expectations. Craft skills training is a big part of the knowledge aspect. The Maintenance Director explained how the training process has improved and adapted over the years: “Years ago, we might have taken our newest employee and dropped them right in the deep end. Most people in the industry thought this was the most effective tactic for learning back then. Now, we realize that there are a lot of correct steps we need to take to ensure that Maintenance Crafts are properly trained.”
One key aspect of training is giving people the initial basic skills that they require to be involved in maintenance jobs. After those basics are covered, it is important to develop the person with more advanced knowledge and techniques. For a business to be productive and equipment to be reliable, effective craft training is important. “Training will reduce equipment downtime because it helps ensure the work is being done properly, and consulting experts on each training topic is a big part of that.”
In his line of work, the Maintenance Director has noticed that most training sessions and professional development are ineffective because they do not always consider how adults learn, and how it differs from how kids learn. “Trainers will provide a detailed rubric of all the steps and use it to train and test people. This is not the best method, because it is not hands-on enough. I went to one training session that was great because they had a lecture hall that was right next to a lab. In the lab, they had all the tools and equipment that one would have in a shop, so the craftsmen can do all kinds of demonstrations. The retention of knowledge after those sessions is just wonderful.”
The Maintenance Director incorporates hands-on training whenever possible. “We will have three people doing something at the same time, and the instructor will be watching. They might say, ‘Stop! What is he doing wrong?’ And continue prompting students until they understand best practices.” This kind of training really makes a difference, and therefore makes plants run better. The Maintenance Director’s top priority is that people go home safe, and they go home happy because they feel confident and satisfied with their work.
“Looking forward, the picture may look a bit different; with fast-changing technology, opportunities in the field may adapt over the years,” he added. In the past, the Maintenance Director explained that there were a lot more mechanics and pipe fitters, however recently, there are more instrumentation technicians and control engineers. “These careers will continue to change as the world changes.”
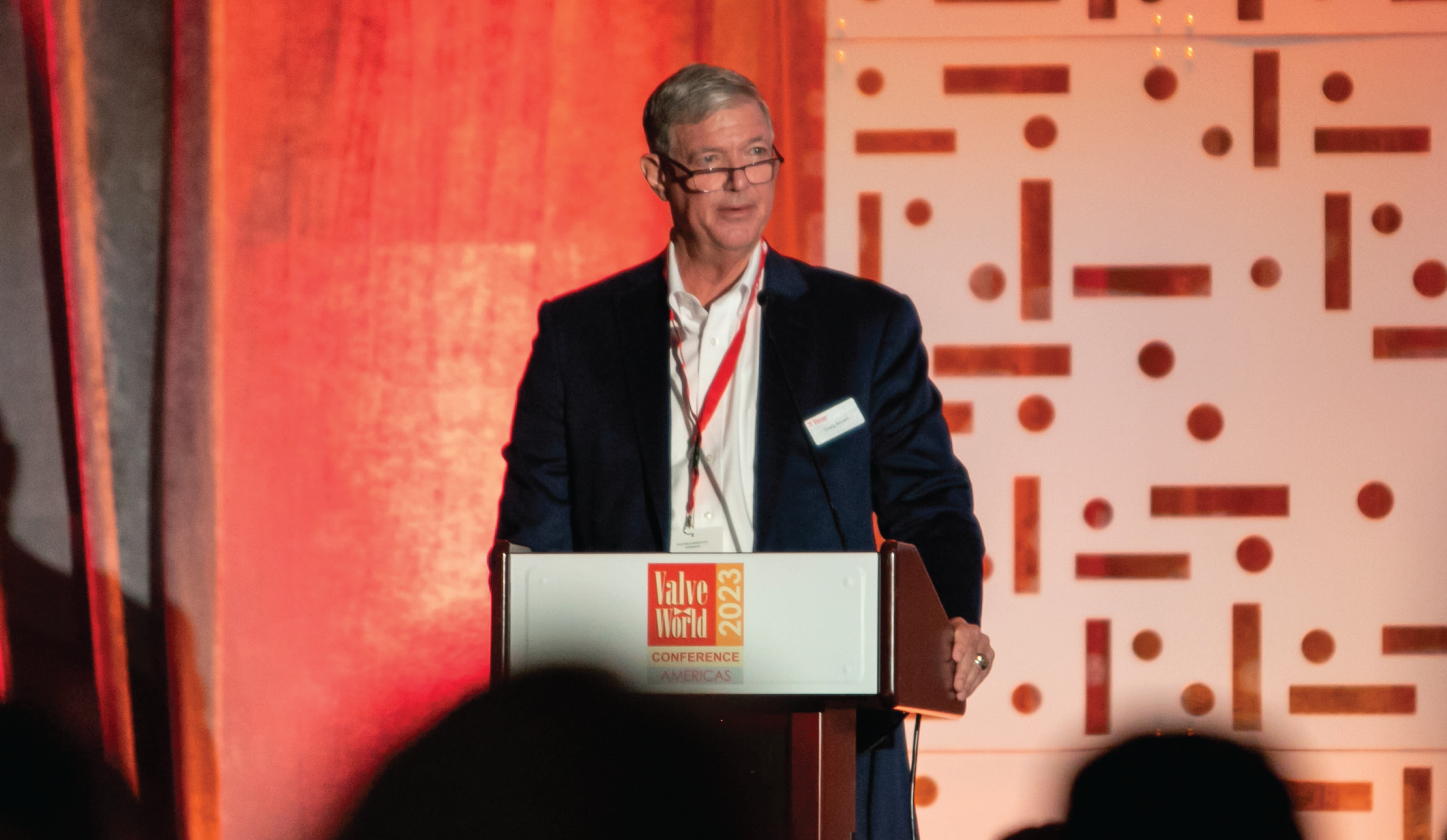
4. An Hour’s Pay for an Hour’s Work
The fourth philosophy to strive for is an hour’s pay for an hour’s work. Fair pay and motivation are key components of any workplace.
“I say an hour’s pay for an hour’s work because anything on either side of that is wrong. I will never ask somebody to work without pay, and nobody should expect to get paid without contributing honest work during their paid time.”
5. Give People a Positive Work Experience
Leaders in any work setting are in a unique position to be able to influence several people’s attitudes and experiences. “We can get the work accomplished and give people positive self-worth with a little conscious attention. Considering how to accomplish each job while giving people the most positive possible experience results in happier, more productive, and more loyal employees; it is just the right way to treat people.”
The Big Picture
Finally, the Maintenance Director emphasized the importance of the big picture. He considers KPIs, performance monitoring, personnel issues, and training programs, among other things, as essential aspects of this bigger picture. He discussed the importance of interdepartmental cooperation and strategizing together in order to ensure that everyone is on the same page. This kind of cooperation and teamwork also opens doors for improvements and progress.
“There are some important questions to ask in order to achieve big picture thinking: Where is the industry headed? What is lacking? What is needed to be successful? Once these questions are addressed, the next step is to implement technical training, people skills, and craft skills, all of which are necessary,” he concluded.