Hydrogen is trending. There are technological developments all around and a whole new industry seems to be emerging. Most would agree that it is a fantastic development for humanity as hydrogen is seen as the missing link to decarbonizing the world. Ironically though, hydrogen has been used in chemical processes for years. This leads some to question, what is different about it? Many suggest that the answer has to do with the fundamental purpose of hydrogen; decarbonizing the world at an unprecedented scale.
By Emiel Lechevallier, SME Hydrogen – Ventil
Hydrogen Valves Standards
Hydrogen is used in known for many different applications such as rocket fuel, chemical processes, welding gasses, and countless others. Generation plants have existed worldwide for some time, hydrogen valves have been in operation for years. These valves are considered as chemical service which means they are often subjected to the requirements of ISO 15848 and therefore tested for fugitive emissions.
ISO 15848 is to go-to standard for fugitive emissions in the valve industry, with only a few exceptions. A notable exception is the Shell MESC which is considered to be a more practical variant of the ISO. What they have in common is the principle of testing; both use tracer gasses to detect extremely small leakages to the environment known as emissions. Between these standards, the only allowed gases for testing are helium and methane. The use of these gases has purpose and benefits, but they also have some clear limitations; helium is a finite resource, and methane is flammable and a greenhouse gas.
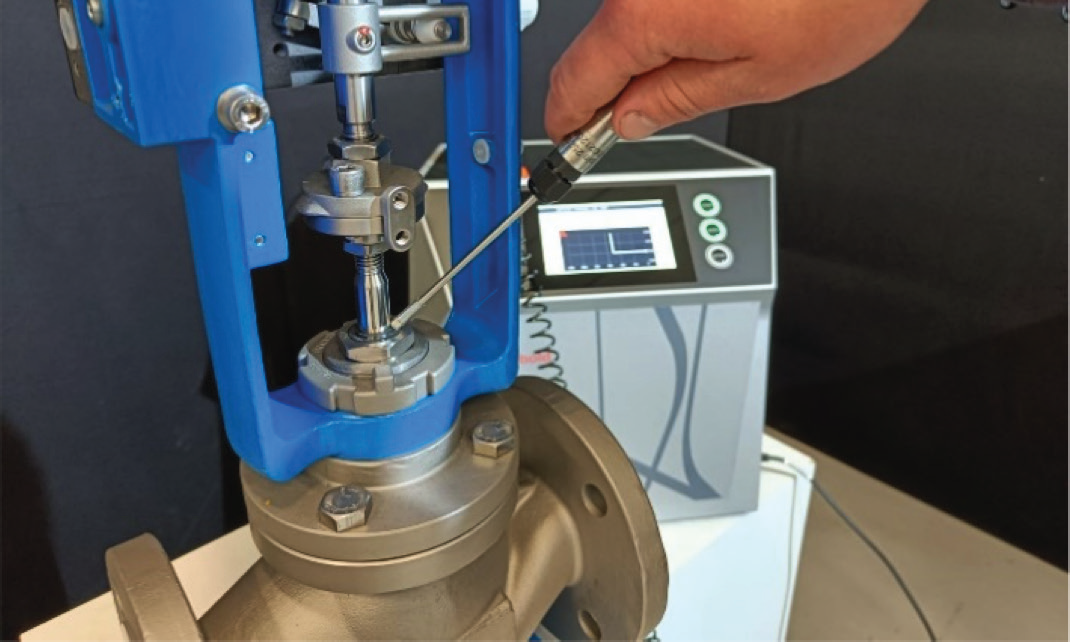
An Alternative is Needed
With the fundamental purpose of hydrogen in mind, one can expect that fugitive emissions will be a big subject in the future. As the number of valves produced will increase, so will the number of tests needed to ensure they comply with the necessary standards.
Many believe, therefore, that it will be inevitable that an alternative to helium and methane should be introduced on the grounds of cost, availability, and practicality. Many believe that hydrogen is actually very suitable as a tracer gas, as it has the properties to leak quicker than any other substance, even in comparison with helium. Using high concentrations is not suggested, but rather a low-concentration mixture of 5% hydrogen and 95% nitrogen. Coincidentally, this combination is readily available on the market and is known as forming gas.
Forming gas is often used as a backing gas for stainless steel welding, and contrary to popular belief, the gas is stable and will not ignite under ambient conditions. Safe concentrations of the gas are prescribed in ISO 10156 with a threshold of 5.5%. It is also commonly available in the market and roughly 1/10th the price of helium.
Testing with Forming Gas
Although a seemingly low concentration, hydrogen is still very much detectable using the right instrumentation. Depending on the situation, either a mass spectrometer or hydrogen sensor can be used to detect ISO’s level A and B emissions without the need for a vacuum. An accumulation method in the form of bagging may be appropriate in some cases; avoiding the vacuum method would simplify the process of testing.
The first step to implementing this change is approving the modification of text in the standards used for testing. Shell Global Solutions, for instance, has indicated they will include forming gas into their standards for fugitive emissions testing on the grounds that helium will drastically increase in price due to limited availability. Changing the standards would be beneficial to reduce the cost of valve testing.
It is essential to keep in mind that the transition to a different gas may require different measuring equipment and procedures. In fact, if one looks at the theory behind leakages and emissions, it is clear that the physics behind a leak changes depending on the size of the leak.
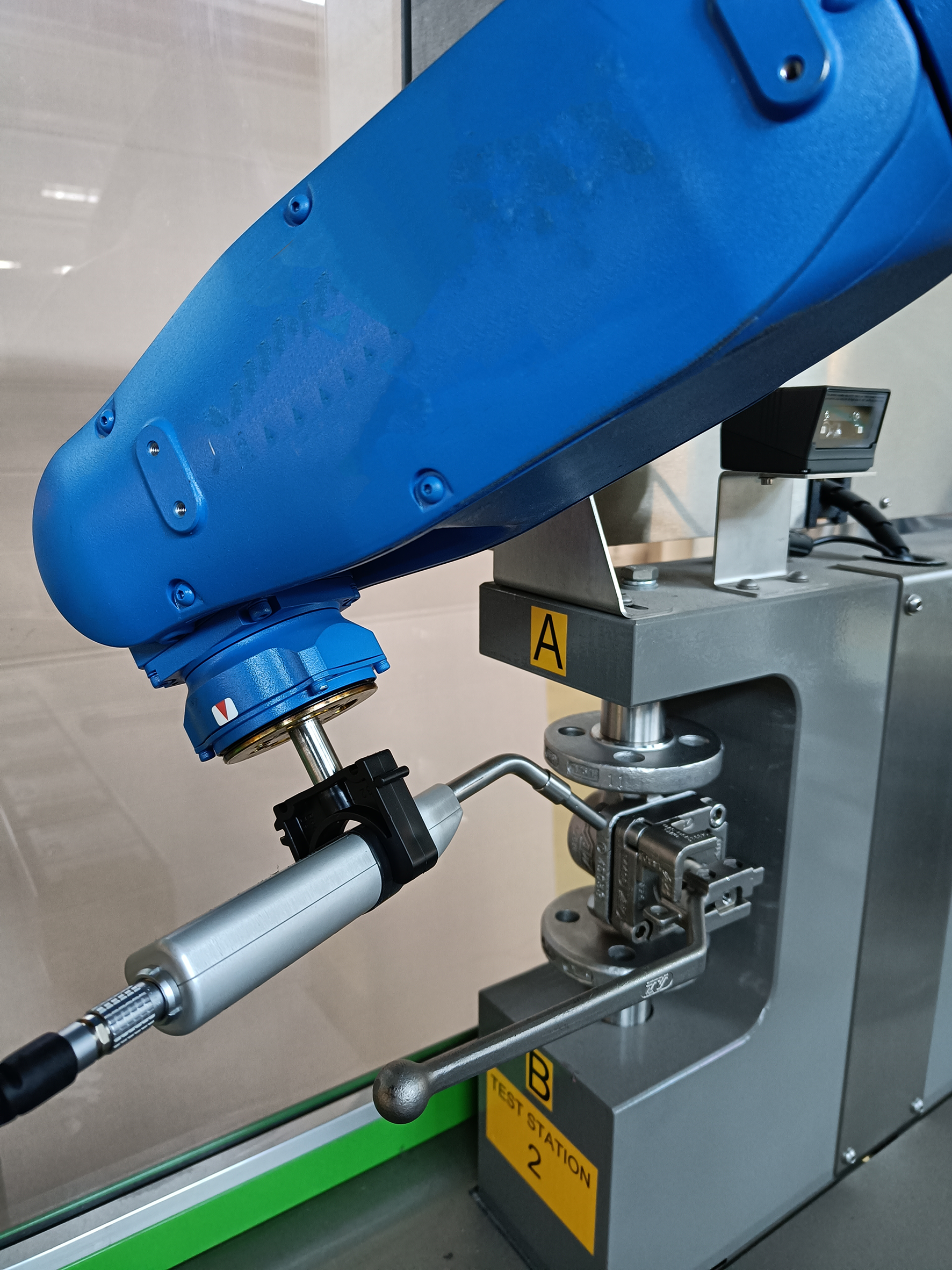
If, for example, the test medium is changed, one sees a difference between laminar and molecular leakages. Laminar flow is only influenced by the dynamic viscosity of the media, and molecular flow is only influenced by the relative mass of the medium’s molecule. Practically speaking, this means that hydrogen leaks quicker compared to helium and methane in both types of leakages. Surprisingly this also indicates that methane should leak quicker than helium in the laminar range, and helium leaks faster than methane in the molecular range. This shows that the dynamics of a leak are very important to understand when considering the test methods. It also shows that a common conception is incorrect: “helium leaks faster, because it has smaller molecules”. To be clear, that statement is not at all supported by scientific evidence.
Factors to Consider
The proposal to use forming as a test gas does raise an interesting question: if forming gas is affordable, it leaks quicker compared to water and air, and the leakages can be recorded digitally, can it then be used it for non-hydrogen applications as well?
The answer is yes. The business case to reduce test times on the grounds that forming gas leaks quicker than water and air, is very easy to make. In fact, being able to detect extremely small leakages in seconds with digital instrumentation is the only way to automate a pressure test fully and reliably. It has the potential to drastically reduce test times and eliminate the need for human intervention.
This in turn shows potential applications for API 598 and EN12266 valves on the grounds of productivity and cost efficiency. Acceptance of alternative mediums for testing by companies is the first step to allowing the hydrogen industry to sustainably grow. A second step would be to critically evaluate the procedures which the industry follows for fugitive emissions testing.
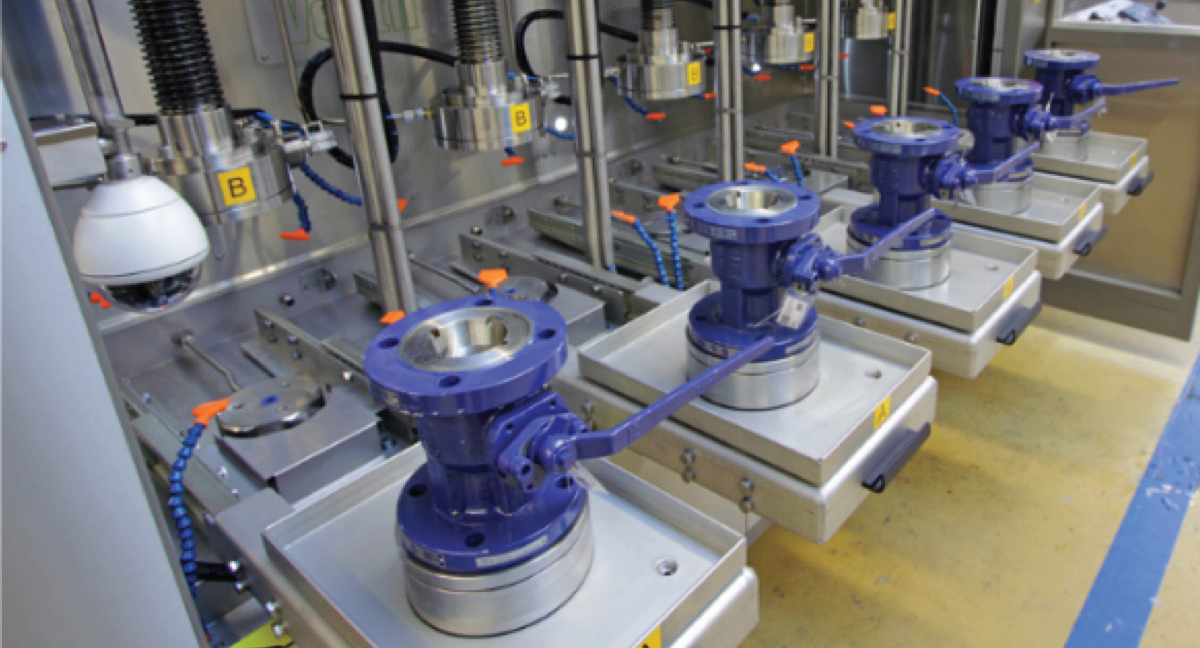
For example, industry professionals often hear that inspectors are careful with excessive lubes and grease on a valve being tested. The argument is that the substance may temporarily clog the leakage path which hides the actual emissions. There are examples of situations where a previously performed hydrostatic pressure test hide relatively large leakages, which are then easily detected after hours of operation. Obviously, these effects are subject to different parameters, but these effects do occur with water and even compressed air.
It is therefore important that there be some form of guarantee that particular steps have or have not been performed during the manufacturing and repair of a valve, as these are just as critical as the test results.
Although this may seem excessive, it has been predicted that the political pressure to decarbonize and justify emissions will result in more stringent rules. It is not unthinkable that today’s batch testing for- mat for fugitive emissions will turn into 100% testing with a mandatory emission certificate as the output.
Final Thoughts
In conclusion, the dynamic of the hydrogen industry will be very different from the hydrogen activities that have taken place so far. Hydrogen’s scale and purpose will ultimately change the requirements for valves, and many believe that as an industry, those changes should be considered today.
Although the first steps to change have just been set in motion, many foresee an acceleration coming up in the next three years. A key challenge is to avoid major misalignments between the new products being developed and having the appropriate equipment and processes in place for production and testing. Failing to develop both at the same rate is a major concern for quality assurance, and a major incident waiting to happen.
The irony is that the knowledge and technology to solve tomorrow’s challenges are already developed. They just need to be accepted into the current industry standards and production processes.
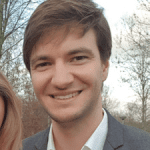