Steam is one of the most forgiving utilities in the industrial complex. Its functional elasticity allows steam systems to be neglected and abused by organizations, ultimately increasing their carbon footprint. By taking a few simple steps to improve the steam system, carbon emissions, and utility costs can be cut dramatically.
By Travis Mosher, President – R.B. Mosher Co.
The steam system begins and ends with the boiler. At the heart of the matter, boilers and their respective steam system are akin to the heart and circulatory systems in a human’s body. They are even treated similarly when they begin to act up or break down. For instance, an honest doctor would take note of a person’s diet, blood pressure, lab tests, and exercise habits and then, suggest changes where possible before adding medication. This is true with boiler and steam system operation. While water treatment and chemicals (medications) play an important role, they cannot overcome poor boiler operation and maintenance practices.
Looking at the Boiler
When approaching a steam system for the first time, it is best to go to the boiler tag first to identify the maximum pressure design and compare it with the current operating pressure. Boilers are often turned down because ‘they do not need much steam’ or ‘it does not need it to be that hot’. These common practices do not consider how boilers are designed to operate.
Each boiler’s nozzle is designed to pass a specific volume of steam at a given pressure. Therefore, the more the boiler pressure is reduced, the greater volume of steam is formed and is trying to pass through the same size nozzle. This causes a dramatic increase in velocity through the nozzle which increases the number of water droplets in the line. This wet steam, along with condensate accumulation, can lead to the most dangerous and destructive phenomena within a steam system, water hammer.

According to, Energy.gov, “water hammer is caused by stream flowing over subcooled water [sending slugs of water down the line hammering into the nearest valve, is elbow, flange].”1 When the boiler pressure is reduced below 80% of the maximum design pressure, wet steam is created, reducing the overall efficiency of the steam system. Water hammer becomes inevitable due to the increased steam volume and velocities in the line. The small amount of savings that would be seen on a gas utility bill will be overshadowed by the cut valve seats, steam leaks, and increased water and chemical use. This in turn dramatically expands the overall footprint.
By adjusting the boiler pressure to >80% of the maximum design pressure, an operator can provide the facility with the most efficient production of steam. Once the boiler pressure and operation are addressed, it is best to assess the current maintenance and trap replacement program.
Adding a Steam Trap
For a steam system to run efficiently, the condensate that is formed when it begins to cool must be dealt with effectively. This can be accomplished through the addition of drip legs with pennant steam traps, steam separators, and condensate pump traps. A steam trap is a valve that only opens to allow the condensed steam out (or hot water). This maintains heating efficiency while preventing the accumulation of condensate inside the steam header and associated piping.
According to the Energy.gov, “In steam systems that have not been maintained for 3 to 5 years, between 15% to 30% of installed steam traps may have failed.”2 A failed steam trap can leak anywhere from 15-200lbs/hr of steam. Based on a steam study that Pennant and R.B. Mosher Co. performed in 2021 on a local tank farm, the average cost of steam (which includes gas, water, chemicals, and heat), along the Texas Gulf Coast is about USD 7.00$/1000lbs of steam. Then by utilizing the Napier Formula3, one can determine steam losses for a single low-pressure steam trap that is failed; a failed valve can cost a facility up to USD $ 1,000/yr. or more in steam losses.
When speaking with local facilities along the Gulf Coast, it was found that on average most facilities do not do steam surveys at all. Some can conduct them in-house but, most sites lack of manpower to implement changes or funding. The steam trap population in many of these facilities is in the hundreds or even thousands. For each year that a survey is not conducted, and the steam system is neglected, millions of dollars in steam, water, chemicals, and utilities are wasted, expanding the carbon footprint.
The solution does not have to be expensive training and hiring more engineers. It can be addressed using appropriate equipment. Recognizing the symptoms of underlying maintenance shortfalls and equipment failures is the first step. Failed steam traps, undersized steam or condensate headers, lack of pump traps on heat exchangers, low boiler operating pressure, poor piping design, and improper trap selection; each of these is a common problem in many facilities.

Implementing Solutions
Following the boiler house evaluation, there must be an initial walkthrough of the steam and condensate system with trained professionals. Any piping or design flaws are identified and logged. The walk through is then followed up with a steam trap survey where each trap is tagged, tested, and a report generated. Within days of making these changes, operators have seen wastewater costs reduced by up to 50%, heating and process times reduced, and most importantly, reduced water hammer. Steam surveys are a great way to identify steam trap failures and integral to any maintenance program.
Keeping steam traps in working order or even getting an annual survey can be a daunting task for many industrial tank farms and petrochemical plants. When taking steps to maintain a steam system, it is important to educate all parties in the facility on how to identify trap failures and potential steam hazards. Steam systems typically give off sight and sound clues when they begin to function improperly. If the proper training has taken place, these clues can be easily identified by onsite contractors and other personnel. While not every ping or steam plume necessarily means a failure has occurred, notifying the steam/maintenance personnel of these abnormalities, will allow them to be inspected, documented, and identified as a potential risk or in need of repair. These solutions keep everyone safe and save valuable heat, water, and chemicals.
Steam trap selection can be just as important as education and maintenance. If the wrong trap is installed for a particular application, it will not operate properly and can even cause water hammer.

There are many different types of steam traps, such as Pennant Thermodynamic disc style trap and the Float and Thermostatic. The Thermodynamic trap is ideal for drip legs on steam mains and tracing applications. The Float and Thermostatic is designed for high condensate load industrial processes (< 350 PSI) such as reactors or dryers with continuous draining and a built-in air vent to assist during start-up. Traditionally Float and Thermostatic steam traps have been made from cast iron. Industrial facilities can be rough on equipment before it even gets installed. By changing over these traps from cast iron to carbon steel the number of accidental overtightening, drops, and freezing failures are tremendously reduced.
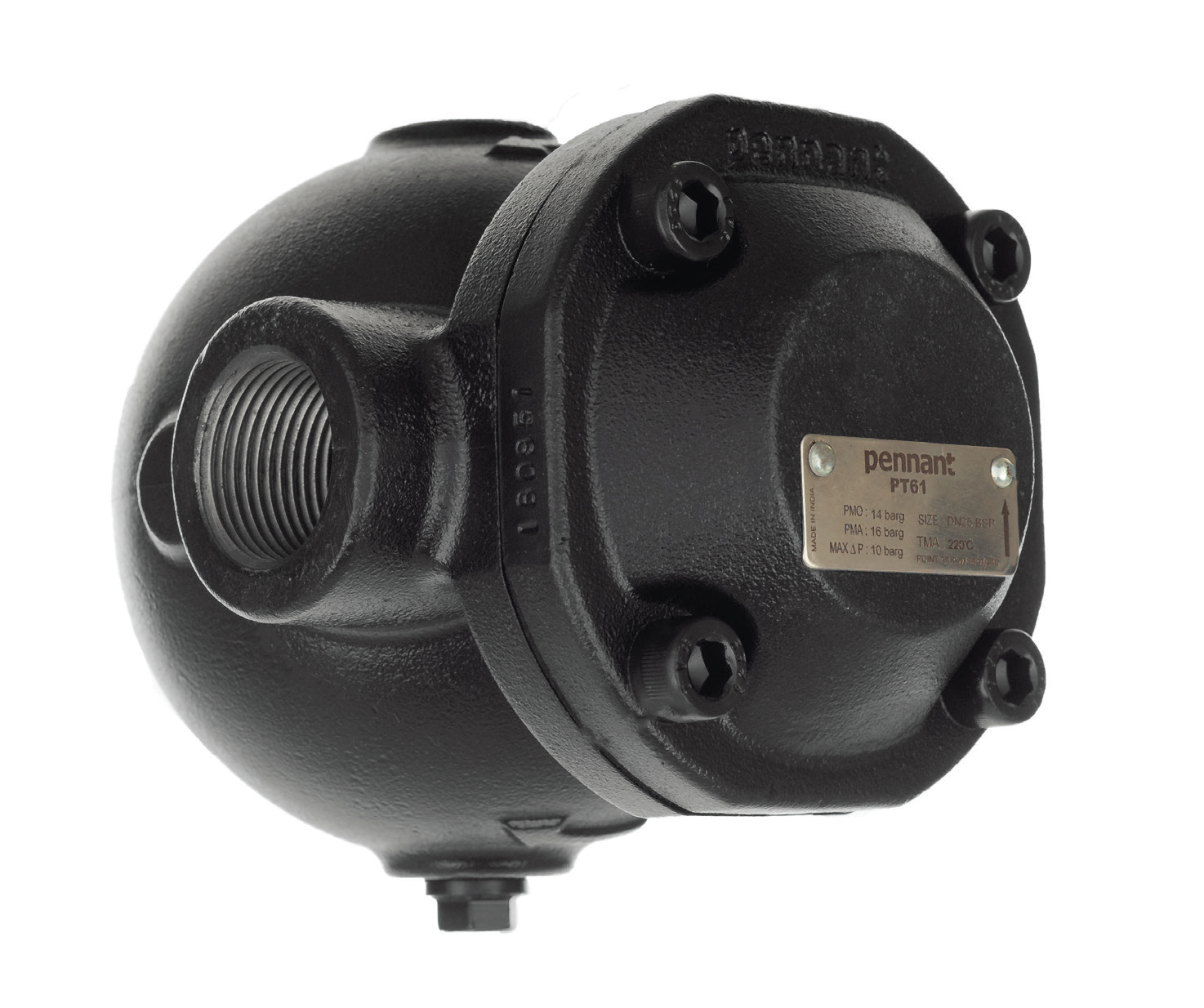
Final Thoughts
Steam is the most forgiving utility when neglected. However, the neglect comes at a high cost by dramatically increasing greenhouse emissions and utility costs while also destroying piping and equipment. By utilizing the correct valve and valve seating (steam trap), facilities can be assured they will have lower utility costs, increased heating efficiencies, less equipment failures, and a smaller carbon footprint.
References:
- https://ehss.energy.gov/oesummary/ oesummary2006/2006-11screen.pdf
- https://www.energy.gov/eere/amo/articles/ inspect-and-repair-steam-traps#:~:text=In%20 steam%20systems%20that%20have,into%20the%20 condensate%20return%20system.
- Microsoft Word – REDONE~1.DOC (invenoinc.com)
