This article is intended to provide useful information for users such as valve design engineers, valve procurement engineers, and pipeline system design engineers, who are dealing with valve material selection in their daily work. Valve material selection includes material selections for the valve body, and valve trim (typically includes a ball, plug, disk, seat, stem, and sleeves needed to guide the stem). Valve material selection is a big topic to be discussed, however, this article is only focused on the material selection for the valve body.
By Dongcheng Li, Chief Engineer and R&D manager – FBV, and Gobind N. Khiani.,M.Eng.,P.Eng. – Fellow-Piping/Pipelines
Background
Valves are one of the most important components for a pipeline or piping system, because valves enable process engineers to open, close, and redirect the flow, control the flow rate, adjust the pressure of the system, release pressure, and more. Based on functions, working conditions (including type of media, flow rate, pressure, and temperature) and other requirements, proper valves need to be selected for each specific application.
In general, the valve body, bonnet or cover, and body joint, bolting shall be constructed of material as listed in the respective ASTM specifications referred to in Table 1 of the ASME code B16.34.1 Materials for different services proposed in this standard come from real world experience including failures and successes, therefore are tested and proven.
Criteria for Material Selection
Criteria for the selection of the materials are not detailed within the scope of the ASME code B16.34. The possibility of material deterioration in service and the need for periodic inspections are the responsibilities of the user, i.e., carbide phase conversion to graphite, oxidation of the ferritic materials, decrease in ductility of carbon steels at low temperatures, susceptibility to intergranular corrosion of austenitic materials, or grain boundary attack of nickel-based alloys, are among the items requiring attention by the user.
Among these factors, the most important factors are the operating conditions, and internal flow media properties.
Materials in Table 1 of the ASME code B16.34 are given in four groups. Generally speaking the materials can be grouped as: carbon steel, low alloy steel, alloy steel, stainless steel, and exotic metals. Considering service temperature limitations, Table 1 should only be used as general reference for commonly used materials.
Besides temperature, another factor in selecting the valve material is the internal flow media chemical properties. Some applications require the use of stainless steel or exotic alloys to withstand the extreme corrosive properties of the flow media. But, for applications handling non-corrosive flow media at room temperature, carbon steel provides the most cost-effective solution.
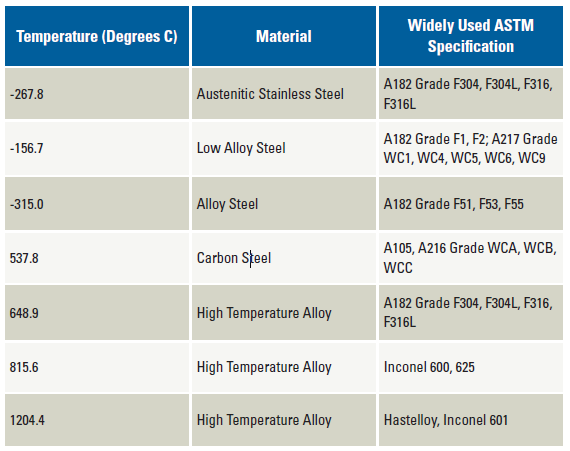
Commonly Used Materials
Carbon steel is a type of steel that, as the name suggests, has a higher concentration of carbon than other types of steel. Most types of steel have a relatively low carbon content of about 0.05% to 0.3%. In comparison, carbon steel has carbon content of up to 2.5%. Carbon steel is stronger than stainless steel and is resistant to wear. Valves made of carbon steel can withstand high pressure, but are susceptible to corrosion, and can also be brittle due to the hardness of the material.
Some commonly used carbon steel materials for valve body are: casting steel ASTM A216 with grades WCA, WCB and WCC, forging steel ASTM grade A105/ A105N, and low temperature carbon steel (ASTM A352 LCB, LCC, ASTM A350 LF2). Among the three casting steel grades WCA, WCB and WCC, WCB is commonly used in oil & gas industries for regular temperature applications, and it is the casting version of forging steel ASTM grade A105.
When selecting material for the valve body, based on the material processing methods, there are both forged and casted steel. For a particular specification and grade of forged steel, there is a corresponding casted steel with same chemical components. These can be used equivalently for chemical and mechanical properties. However, forging steel provides better uniformity of composition and structure than casted steel.
Forging leads to metallurgical recrystallization and grain refinement due to thermal cycle and deformation process, which strengthens the resulting steel products, especially in terms of impact and shear strength. Forged steel is generally stronger and more reliable than casting and plate steel, since the grain flows of the steel are altered, conforming to the shape of the part. Forged steel valves are mainly used in long-distance oil and natural gas pipelines, and other high-pressure industrial pipelines.
ASTM A105/A105N steels are suited for fluid flow requiring assured performance, tight shutoff, constant torque, and no maintenance. ASTM A105 is the most used carbon steel forging material grade in manufacturing forge piping components such as valves. This carbon steel grade is used for ambient and higher temperature service in pressure systems. The ‘N’ in A105N stands for ‘normalization’ of A105. The normalizing heat treatment will ensure the forging has superior properties to the ‘as forged’ material.
ASTM A350 Grade LF2 is a low temperature carbon steel suitable for lowest temperature of -46°C in piping systems when there is a possibility of process fluid temperature falling below -29°C during operation.
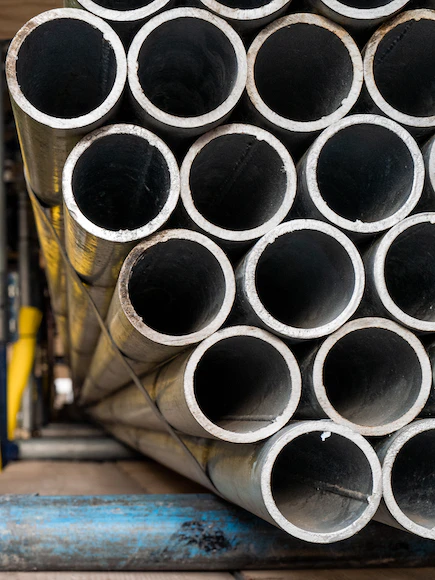
Stainless Steel Specifics
Among the forged steel grades mentioned, the ones covered in points 3 and 4 are stainless steels. Stainless steel is a group of ferrous alloys that contain a minimum of approximately 10%-20% chromium, a composition that prevents the iron from rusting, and provides heat-resistant properties.
304 stainless steel is the most standard used alloy of this type. Essentially, 304 is an austenitic chromium alloy which is also known as an ‘18/8’ stainless as the make-up of the steel is 18% chromium and 8% nickel.
304L is an extra low-carbon variation of 304 stainless steel with a 0.03% maximum carbon content, that eliminates carbide precipitation due to welding. As a result, this alloy has better weldability comparing to 304 stainless steel. It often eliminates the necessity of annealing weldments except for applications specifying stress relief. It also has slightly lower mechanical properties than 304.
Grades 304 & 304L stainless steels have strong anti-rust and anti-corrosion performance, and show excellent resistance to a wide range of atmospheric, chemical, textile, petroleum, and food industry exposures. They are non-magnetic and non-hardenable, except by cold working, and are appropriate in fi eld working applications, however are susceptible to chloride stress corrosion cracking.
The maximum temperature to which 304 stainless steel and 304L ball valves can be exposed continuously without appreciable scaling is about 1650°F (899°C). For intermittent exposure, the maximum exposure temperature is about 1500°F (816°C).
Grades 316 & 316L stainless steels are valve industry standard stainless steel body material. Comparing to 304, the addition of molybdenum increases the general corrosion resistance, and the resistance to pitting by chlorides. It has the widest temperature range of any standard material: -425°F (-254°C) to 1500°F (816°C). The alloys are used in mildly acidic and alkaline conditions and for handling citric, oxalic, and phosphoric acids.
F50 and F51 are duplex stainless grades, they are called duplex grades because their metallurgical structure consists of two phases: austenitic phase and ferritic phase. They are designed to provide better corrosion resistance, particularly chloride stress corrosion and chloride pitting corrosion, and higher strength than standard austenitic stainless steels such as Type 304 or 316. The main differences in composition, when compared with an austenitic stainless steel, is that the duplex steels have a higher chromium content, 20–28%; higher molybdenum, up to 5%; lower nickel, up to 9% and 0.05–0.50% nitrogen. Both the low nickel content and the high strength (enabling thinner sections to be used) give significant cost benefits. They are therefore used extensively in the off-shore oil & gas industry and petrochemical industry applications including valves. Duplex stainless steels also have greater toughness than ferritic alloys, especially at low temperatures.
F53, F55, F60 are super duplex stainless grades, which are high grades of duplex steels and have all of the good properties of the duplex steels. Comparing to the lower grades of duplex steels, super duplex steels have higher chromium and molybdenum content1, which makes them extremely resistant to uniform corrosion by organic acids like formic and acetic acid. Super duplex also provides excellent resistance to inorganic acids, especially those containing chlorides.
Discussion
The materials mentioned in this article cover the most commonly used materials for industrial valves. In addition to them, for valve applications that handle non-corrosive fluids, at low pressure and room temperatures, cast iron is a very cost-effective option, and for very corrosive fluids, more exotic alloy grades higher than super-duplex stainless steels could be needed. To conclude, the decision needs to be made based on material-fluid compatibility.
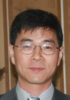
