Individuals today live in a highly industrialized world. Technology advances at such a rapid pace that it seems like new products and innovations appear almost daily. The foundations of modern society date back to the 18th century and the dawn of the Industrial Revolution. The invention of the steam engine in 1711 opened the floodgates to a world of machinery that led to the beginnings of industrialized manufacturing, farming, and transportation as it is known today.
By Chris Morris, Sales Engineer – Teadit
Need for Efficiency
As industry expanded, the demand for more efficient equipment grew. In 1867, George Babcock and Steven Wilcox patented the first steam-generating boiler. As boiler technology became more advanced, it became apparent that the key to increasing efficiency and productivity was developing effective seals to minimize energy loss and maximize steam generation. The idea of gaskets and seals was not novel, but the need for more effective gaskets led to the development of new and better materials.
In 1898, Austrian engineer Richard Klinger developed a calendared compressed fiber sheet. This material would go on to become the primary gasket material in the industry for over 75 years. Almost 15 years later, in 1912, the Flexitallic Gasket Company introduced the spiral wound gasket, manufactured from alternating plies of metal with fiber filler to meet increasing pressure resistance demands. However, early spiral wound gaskets were very different from the ones in use today.
Progressive History
In the first two decades after their introduction, the structure of spiral wound gaskets had already begun to change significantly. In 1930, patents for reinforcing the gasket both the inside and outside diameters with additional metal wraps, and early designs for guide rings appeared. Then in 1934, another design, which utilized multiple outer metal plies as a centering ring, was introduced. This was followed by the creation of the conventional metal outer guide ring in 1938, which very similar to those that are used today.
By the 1940s, the spiral wound gasket was the primary gasket for the U.S. Naval fleet. In 1941, designs for the use of ‘soft metal’ fillers were introduced for high pressure applications. 1942 saw early designs for an inner ring to reinforce the gasket against radial buckling. Then, in the 1960s, new materials such as PTFE and exfoliated graphite were introduced as alternative fillers in spiral wound gaskets.
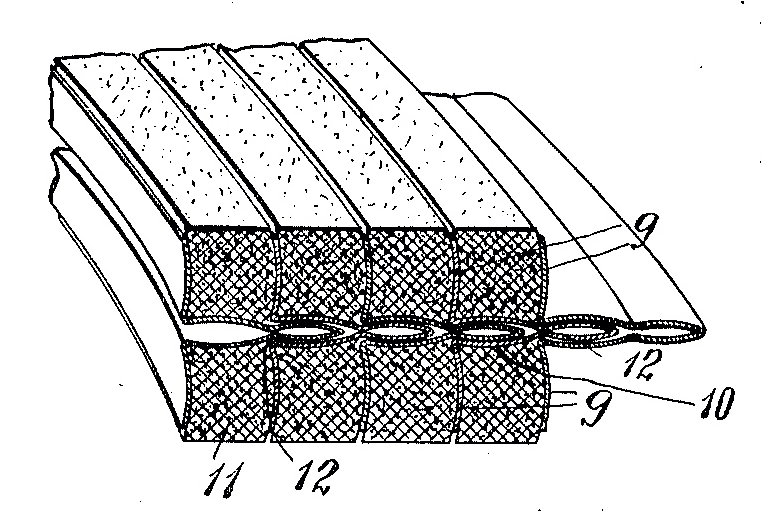
However, it was not just spiral wound gasket technology that was evolving. As boiler technology advanced in the early 19th century, the need for oversight and standardization also grew. Catastrophic pressure vessel failures were not uncommon, which posed a serious risk to workers and public safety. Many aspects of modern standards such as ASME B16.5 and B16.47 (pipe flanges), ASME B31.3 (process piping), and ASME Boiler and Pressure Vessel Code Section VIII (design and construction of pressure vessels) were first developed and codified at this time.
The Rise of Standards
As standards developed for boilers and pressure vessels, additional considerations were made for the gaskets that were so integral to their efficient and effective operation. An important modern standard, ASME B16.20 Metallic Gaskets for Pipe Flanges, has roots as far back as the mid-1930s in the early versions of American Petroleum Institute (API) standards. In the late 1930s and through the 1940s, the American Standards Association (ASA) worked to incorporate the existing API benchmarks into their own standards, culminating in the approval of a new standard, ASA B16.20, in April of 1952.
Both the ASA and API standards continued to undergo developments and revisions over the next 30+ years. Then, in 1973, ASA B16.20 was granted approval by the American National Standards Institute (ANSI) as a national standard. Soon after, API requested that the American Society of Mechanical Engineers (ASME) convert their standard, now designated API 601, into a national standard as well. With the help of ANSI and ASME, these national standards saw greater acceptance and influence within industry.

By its final edition in 1988, the API standard had expanded to include spiral wound and jacketed gaskets, along with ring joints. These gasket styles were therefore also included in the newly developed ASME standard. In January 1993, the new ASME B16.20 standard was first introduced and in 1998, it was approved by ANSI as a national standard. Since then, however, the standard has continued to evolve.
The earliest version of the B16.20 standard, dating back to its API days, was for the most part entirely a dimensional standard. In other words, the primary concern was that spiral wound gaskets be dimensionally consistent, but little to no direction was provided for how they were to be constructed. This meant that individual manufacturers were on their own to determine how the winding element (the primary seal of a spiral wound gasket) was to be made to effectively seal. This led to vast differences in winding performance across the industry. Still, positive developments, such as a color-coding system for the outer guide ring that allowed for easy identification of a spiral wound gasket’s materials of construction while in service, improved identification markings, and the addition of compressibility requirements were all significant advancements.
Further Progressions
In the later part of the 20th century, as companies looked for ways to reduce costs, mass importing goods from the population-rich nations of Asia became a popular means for reducing labor expenses. Workers in nations like China and India were plentiful and economic compared to American labor. Manufacturing centers for toys, clothing, electronics, and more were relocated overseas.
Gasket manufacturers also looked to take advantage of these savings. The increasingly popular spiral wound gasket was a perfect candidate for outsourcing and manufacturing them in China soon became the obvious option. Manufacturers were not the only ones looking for savings as demand for lower-cost options increased from end users as well. This led to significant reductions in spiral wound gasket prices as manufacturers battled for market share. However, forward-thinking critics within the industry recognized that a ‘race to the bottom’ and increased commoditization of spiral wound technology, was short-sighted and in many ways opened a potential Pandora’s Box of long-term implications.
The dawn of the 21st century brought with it increased scrutiny of the direction of spiral wound gasket technology. More resources were being devoted to research and testing to investigate what primary factors contributed to optimal spiral wound gasket sealing performance. In 2007, the long-standing problem of inward radial buckling of windings was finally officially addressed, as the formerly optional inner ring was made a standard industry specification, when not otherwise requested.
Then, in 2011, a team led by the former Global Technical Director of Teadit, Jose Veiga and the former S.M.E. of bolting and sealing for Chevron, David Reeves, published a research paper for the ASME Pressure Vessel and Piping (PVP) Conference entitled, “The Influence of Winding Density in the Sealing Behavior of Spiral Wound Gaskets” (PVP2011-57556). Their research showed convincingly that without careful control of the winding density (the ratio of metal to filler and the number of wraps) across different sizes and pressure classes, spiral wound gaskets would allow for over-compression of the winding, which in turn would allow the flange mating surface to contact the outer guide ring. This would effectively eliminating the winding element as the primary seal and transfer the sealing load to the outer guide ring (a non-sealing element).
Veiga and his team continued their work and at the 2017 ASME PVP Conference, they again presented research entitled “ASME B16.20 Spiral Wound Gaskets Performance Testing” (PVP2017-65371). This work was adopted into the 2017 edition of the ASME B16.20 standard and for the first time for any gasket technology there was an established performance requirement within the standard.
This performance standard was derived based on industry fugitive emissions requirements, which implies that standard ASME B16.20 spiral wounds, regardless of size or pressure classification by the standard, are designed to function as low leak technology. Spiral wound gasket users can request that the test data from manufacturers that show that their facilities are capable of meeting compliance thresholds for flange connectors with ASME B16.20 spiral wounds.
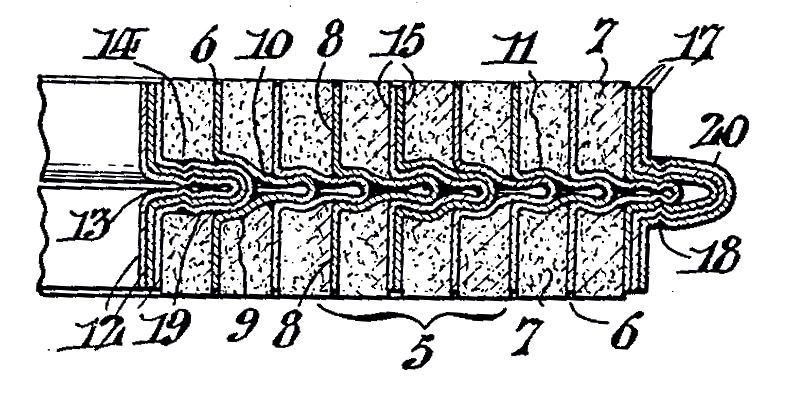
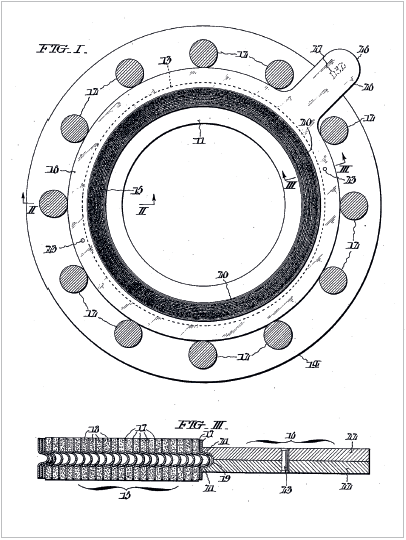
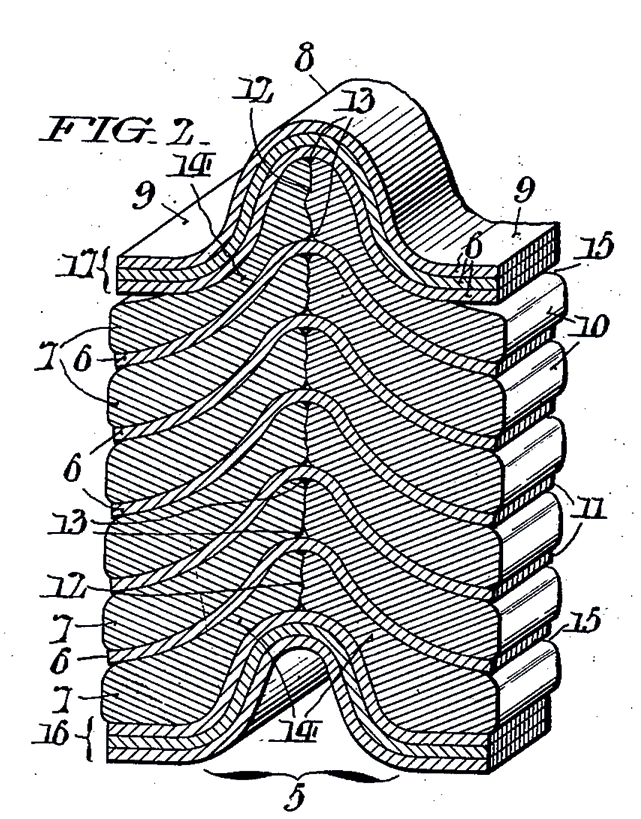
Looking Forward
As industry regulations push for a “net-zero” carbon footprint, technologies that offer emissions compliance benefits will inevitably see increased adoption among end users and may soon be required as a part of EPA consent decrees.
While spiral wound gaskets have a long and storied history, recent advancements show that in many ways, they are still an emerging technology. As the industry pushes for improved performance and reliability, the future of the spiral wound gasket has yet to be written.
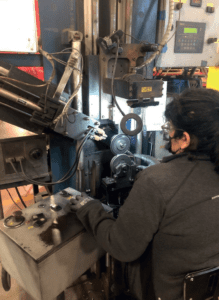
