Water scarcities in Arizona, Taiwan, China and many locations where new semiconductor plants are being built have underscored the need for water conservation. Additionally, water reuse may be cheaper than bringing surface water to the ultrapure level.
By Bob McIlvaine, President & Founder – The McIlvaine Company
In industrial areas there are a number of containments, which present a challenge in the water industry. In agricultural areas, for example, water quality can vary considerably due to potential fertilizer contamination.
Water strategy has evolved from the original once-through concept to a reuse concept, which includes treating waste streams separately. Water needing moderate treatment are subject to different processes than water needing extensive treatment. Today, about 40% of the initial water extracted is treated and reused, however the percentage is steadily climbing.
For example, Gradiant has a unique reverse osmosis approach and is targeting 98% reuse. Ovivo has found that reuse is the most economical option when the quality of incoming water varies. In terms of flow quantity and pump investment, what is important is the quantity of water being circulated, not the quantity entering or leaving the plant.
Fabrication Projects and Water Requirements
In the U.S., there are a number of new fabrication projects which will require increases in recirculation of more than 100 million gallons per day (mgd). Intel alone will be adding 40 mgd.
Figure 1 covers projects underway, and those where sites have been chosen but no final commitment has been made. This table only includes major projects. The U.S. is presently behind three other countries in terms of recirculated fabrication mgd. The recently enacted CHIPS act will narrow the lead of others such as Taiwan, but there is a long way to go. The U.S. presently has 500 mgd of water recirculated at fabrication plants, compared to 950 mgd in Taiwan.
Treatment costs per mgd are very high in semiconductor applications. However, the quantities are modest when compared to other applications. A large municipal wastewater treatment plant may be treating more than 1,000 mgd, or the entire fabrication recirculated mgd in Taiwan.
A 4,000 MW coal fired power plant can circulate as much as 1 million gallons per minute of FGD slurry or 1,440 mgd. The conclusion is that this a challenging but relatively small market for stainless steel. Nevertheless, it has been shown that the most profitable suppliers are ones who have obtained market leadership in high performance niches.1
The semiconductor market is unique in that much of it consists of small valves used in discrete as opposed to process applications. Ultrapure water is used to wash chips and to deliver various chemicals for chip treatment. A fabrication project can require hundreds of tools, and various gases and liquids are used to treat each chip. Because of this, large numbers of small valves are needed for each tool.
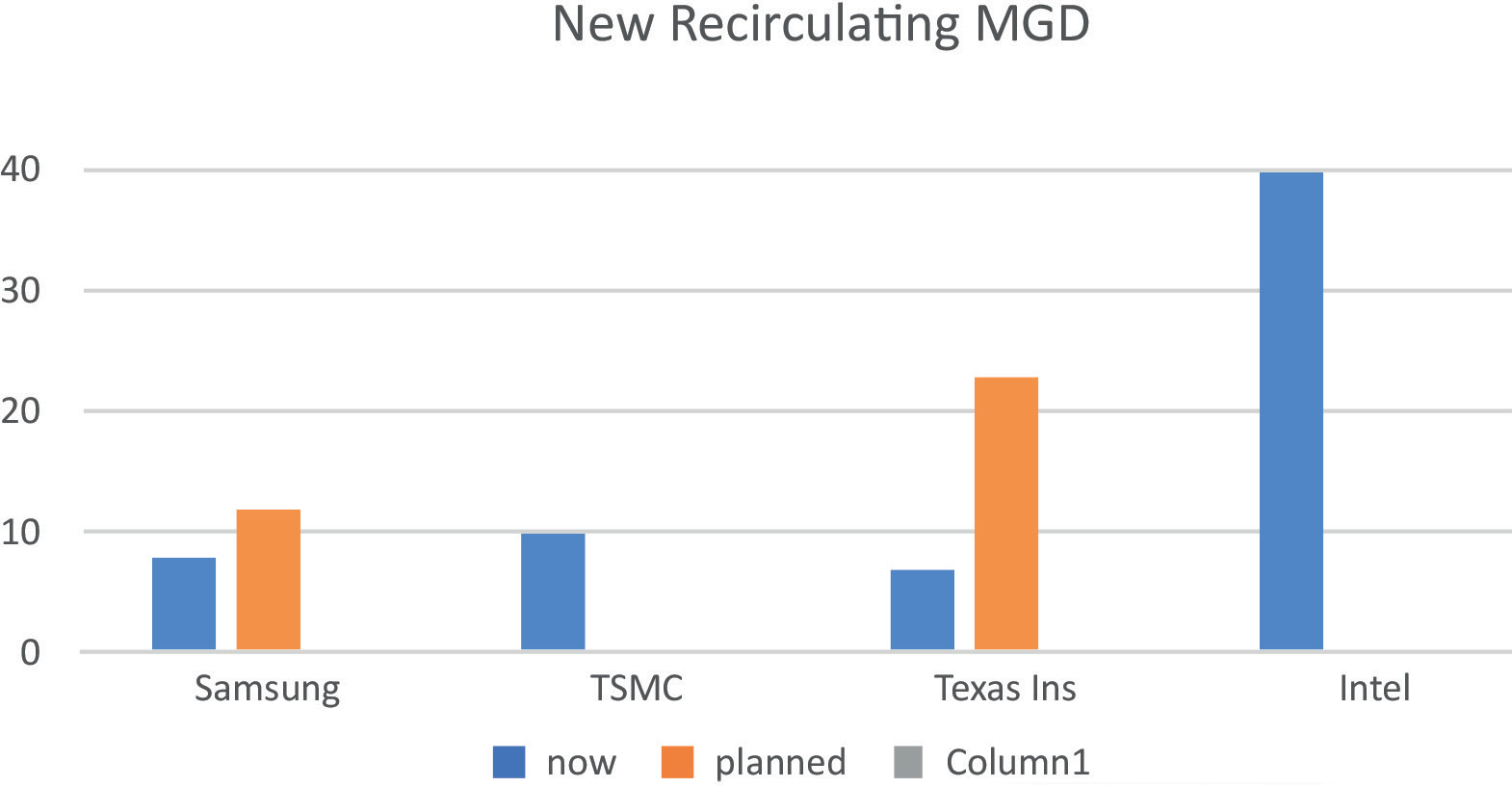
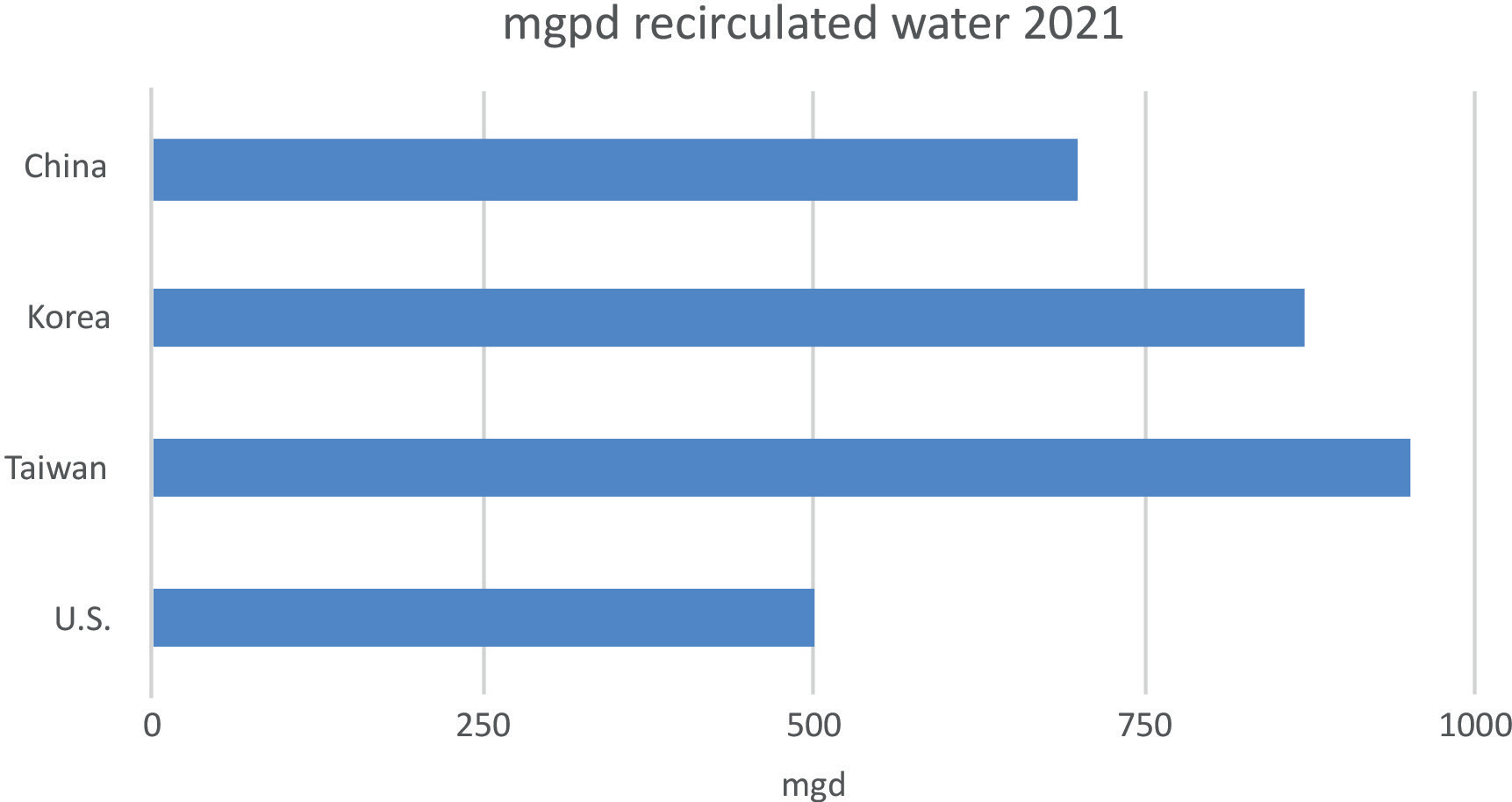
Supplier Profiles
International companies generate most of the valve sales in semiconductor applications. However, some of these companies are small. The largest suppliers of discrete valves such as Parker Hannifin and Swagelok are not the suppliers of the process valves. Examples include:
AGRU Kunststofftechnik GmbH, a manufacturer of high-purity, thermoplastic piping systems for transportation of pure liquids. The materials of PVDF, ECTFE, PP-Gray, PP-Natural are offered with a wide range of pipe sizes, fittings, valves, vortex flow meters and semi-finished products.
Asahi/America manufactures and distributes a full selection of corrosion resistant thermoplastic fluid flow solutions including valves, actuators, single and double wall piping systems, wet process solutions and specialty components. Festo’s semiconductor manufacturing products include more than 15 types of pneumatic rotary and linear actuators, end-effectors, and compact pneumatic valve manifolds with DeviceNet interface for ‘front-end’ and ‘back-end’ tool applications.
FITOK high purity diaphragm valves are mainly used in the semiconductor, natural gas, photovoltaic solar, microelectronics, liquid crystal panel, chemical, pharmaceutical and other industries. They are applicable to conditions with ultra-high purity gases, corrosive gases, toxic gases, flammable and explosive fluids. GEMU high-purity valves are applied for ultra-pure chemical supply systems, ultra-pure water treatment plant and ultra-pure water distribution installations in the semiconductor field. They are produced under cleanroom conditions at the manufacturing site in Switzerland. Both diaphragm and globe valves are supplied.
Georg Fischer supplies piping systems and components for liquid conveyance, measurement, and control. Products include plastic pipe, fittings, valves, actuators, rotameters, fusion machines, tank linings, heat exchangers, secondary containment, flow monitoring and process control instrumentation. KITZ-SCT manufacturers ultra-high purity fluid system components for all phases of semiconductor and FPD manufacturing. Products include valves, fittings and substrates that support both conventional and next generation systems.
Mega Valve is the distributor of high purity bellow valves, diaphragm valves & ball valves, kuze high purity stainless steel tubes, pipes & fittings, ultra-high purity fittings, and metal gasket & face seal components. Parker Hannifin manufactures a complete line of Ultra High Purity fittings, diaphragm and bellows valves, bulk gas valve components, high purity cylinder connections, regulators, TEFLON fittings, valves and tubing, Instrument quick couplers, stainless steel filters, ceramic filter elements, membrane filter cartridges, capsules and electropolished filter housings, pneumatic and liquid valves, digital and proportional valves.
Swagelok Company is a provider of fluid system products, assemblies, and services for the semiconductor industry. Swagelok specializes in a variety of critical semiconductor applications including cleanrooms air filtering, process chemicals piping systems and process gas handling. White Knight manufactures high purity chemical, solvent, and slurry pumps that are entirely free of metal and O-rings. In addition, White Knight offers a full line of accessories including electronic enhancements such as fiber optic stroke and leak detection, translators, programmers as well as pulsation dampeners, and pre pump wafer guard filters. White Knight also provides a full line of normally open and normally closed valves for chemistry, solvents and slurry.
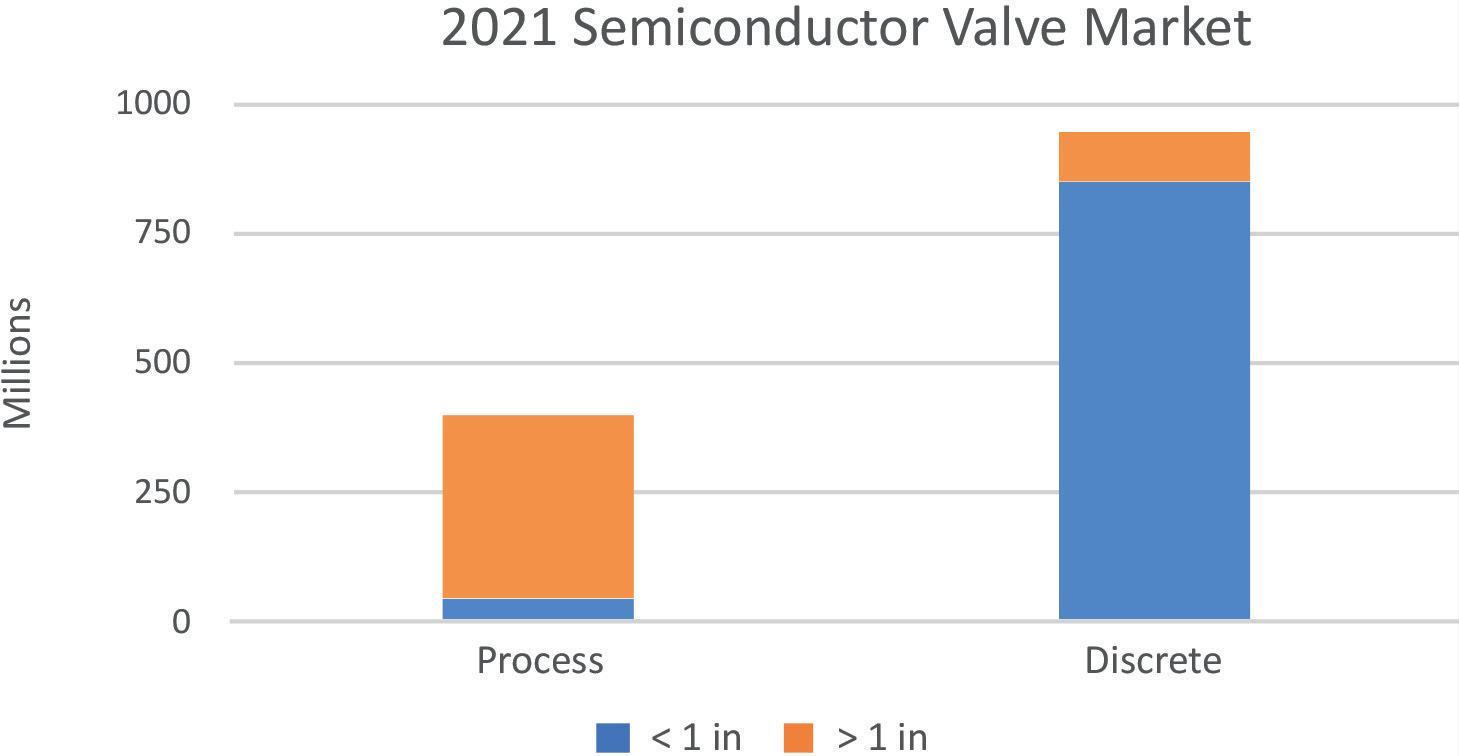
Technology Development
The semiconductor industry is advancing at an unparalleled rate. Relevant valve technology needs to develop along with it. Four subject areas are:
- Product quality
- Energy consumption
- Water consumption
- Cost
Product quality: Ultrapure water valve suppliers need to reduce contamination potential. Discrete valve suppliers need to keep improving the accuracy of their products.
Energy consumption: There can be thousands of valves in a semiconductor plant. The energy consumed by the valves is minimal but valve performance impacts energy efficiency.
Water consumption: Valves play an integral role in water reuse systems which minimize total water consumed. The potential for a 98% reduction is dependent on additional loops with additional valves.
Cost: The potential is not to decrease purchased cost, but to decrease the total cost of ownership of the valves.
Valve technology needs to develop at the same pace as the production technology. As the linewidth decreases, the damage from smaller particles increases.
Valve suppliers need to keep up with technology advances. Many valve companies are members of SEMI and have direct contact with users. Semiconductors are a challenging and important market for valve manufacturers. The high growth rate and willingness of purchasers to pay for performance are attractive features.
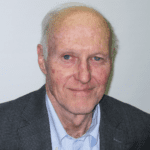