With the effects of climate change making themselves known all over the planet, natural disasters and unusual weather events are slowly but surely becoming the norm, rather than the exception. One need only consider the recent deep freeze in Texas, the current unprecedented heat waves across Europe and the UK, and the increasing frequency of tropical storms, earthquakes, and flooding, to see that natural disasters are now a part of everyone’s quotidian lives.
In the industrial industry, more and more attention has been focused on mitigating the effects natural disasters, especially regarding flooding and chemical leaks. Valve World Americas had the pleasure of speaking with Jeremy Carroll, Global Project Manager at ITT Engineered Valves, about the effects of natural disasters on valves applications, the consequence of being ill-prepared, and how valves may be able to aid mitigate the impact on municipalities.
By Angelica Pajkovic
Preventative Measures
Wastewater, flooding, and other natural disasters can pose significant threats to refinery and plant applications; not only does it cause delays in production, but it can also become a serious safety threat. As damage can be widespread throughout both the plant and in the surrounding community, impact mitigation as it pertains to valves, pipes, and fittings is very important.
“We have seen more and more end users being cognizant of the threat to their surrounding communities, should a disaster take place. This is especially true for those working in a refinery or a chemical plant, as a lot of the chemicals that are run through the pipelines are very dangerous,” stated Carroll.
As the valves used in refineries and chemical plants are typically robust applications, there is not often a high concern that the valve itself will suffer significant damage. Operators instead focus their attention on the integrity of the pipeline they are connect to. If a valve should fail from external factors, it is very likely that pipe has been affected as well, and steps need to be taken to resolve the issue. Typically, the operator (possibly owner, business, organization) takes significant pains to protect the valve, and the fluids they are controlling, from disasters.
“It is very common for us to have a fail-safe system in place,” explained Carroll. “If a plant is affected by a natural force, such as a hurricane or tornado, and the facility loses power, there are systems that will automatically close valves. It is generally set up so that human interaction is not necessary; the valves open or close to prevent anything from leaking or spilling into surrounding areas.”
By ensuring that the correct materials are used and that failsafe systems are in place, operators can mitigate the damages caused by these types of events.
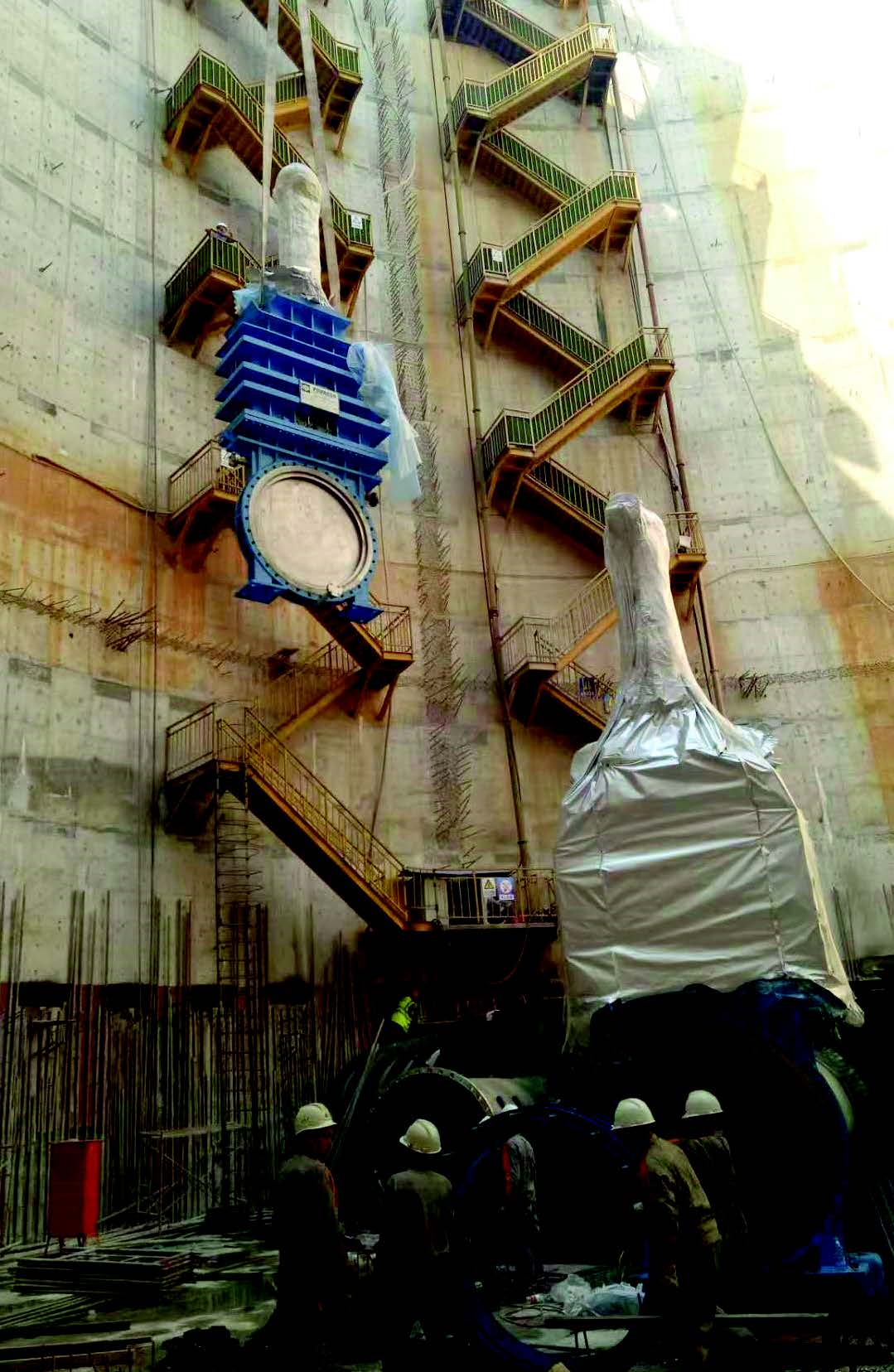
How Valves Can Help
The connection between valves and flooding disasters is obvious. Knife gate valves can be used to either shut off or completely open the flow of fluid in a pipeline, thus transferring and directing it as necessary. While this can greatly aid with flood management, many believe that not enough research has been done on how these valves can be used to further mitigate disaster. Carroll cites two key examples of natural disasters that current existing infrastructure and technology were unable to withstand: Hurricane Katrina in 2005, and the ‘Tax Day’ flood in Houston in 2016. The flood in Houston left people basically swimming around, and it spurred on a new era of research and catastrophe prevention efforts in the valve industry, among others.
To prevent occurrences like contamination, researchers are looking at various methods to effectively divert water away from communities when flooding occurs. Although there are several ideas on the subject, there is one method that many believe could be very beneficial if implemented on a large scale. “There is ongoing discussion about using large diameter pipe and valves, instead of pumps, to divert the flow. This process would take advantage of natural gravity flow.
The issue with using large pumps is that they take a tremendous amount of electricity to run, which, as Carroll emphasized, “is not readily available during a natural disaster.” For this reason, valves might be more useful than pumps when it comes to mitigating disasters and coping with flooding. Ideally, an individual would be able to open or close the valve and allow gravity to take the chemicals, floodwater or wastewater downstream to a safe depository. If there is a pneumatic operator on the valve, it would have an accumulator tank sitting right beside it, which has a sensing system to indicate an upset condition downstream or upstream. It can then either open or close the valve automatically. More work needs to be done on this technology, but the potential for preventing, and coping, with disasters is evident.
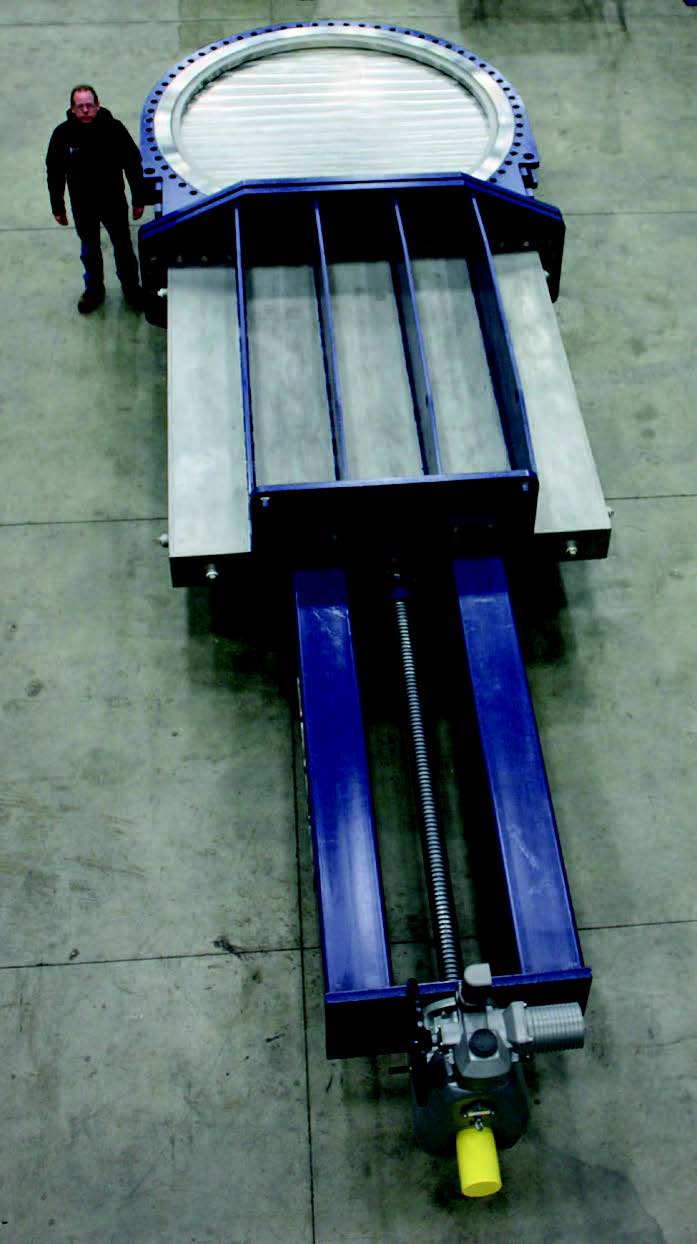
Innovative Solutions
Working with larger valves, spring cylinders, and accumulator tanks does not come easy or cheap; bigger machines, bigger cranes, more materials, and more complex manufacturing are all obstacles that the valve industry faces. Carroll explained that there are ongoing projects to make valves that can be assembled on site, to avoid transportation and installation obstacles, but noted that the availability of raw materials for these large valves is very limited: “In the valve world, most vendors are stepping away from carbon steel components in favor of some sort of stainless or special alloy material. This practice really narrows down potential vendors and makes sourcing more difficult,” explained Carroll. “While valves used to be considered large at 24” in diameter, engineers are now working on 120” diameter valves to address these natural phenomena that are becoming increasingly common.”
Flooding Effects on Municipalities
The effects of flooding extend beyond the valve world, and in fact encompass all of society. It is often municipalities that are hit hardest when disaster strikes, and regular people whose daily lives are interrupted.
Constant population increases in many metropolitan areas has led to a situation where there is often more wastewater than the city’s water system has the capacity to deal with. When a disaster inevitably occurs, such as an earthquake or flood, responders face significant complications ensuring that harmful contaminants are not leaked into urban areas and water systems. Although there are currently no solid solutions to this problem, there are many ideas in the works. Engineers in China, Singapore and Dubai have started working on a system of deep tunnels to move wastewater. “One interesting practice that is taking place in some areas is the creation of a deep tunnel into the ground, that acts as a reservoir,” relayed Carroll. “Response crews will pump all the waste into the deep tunnel, and then in the middle of the night, they will start processing it during non-peak hours, to mitigate the risk of contamination. There has been some talk about implementing something similar in the United States; we could bore deep tunnels vertically because there is no way to expand horizontally. This type of project would require the use of several specialty valves, which I believe would be very beneficial for this type of project. The US is a long way from making these tunnels a reality, but you can imagine the positive effects that such a system might have on flooding.”
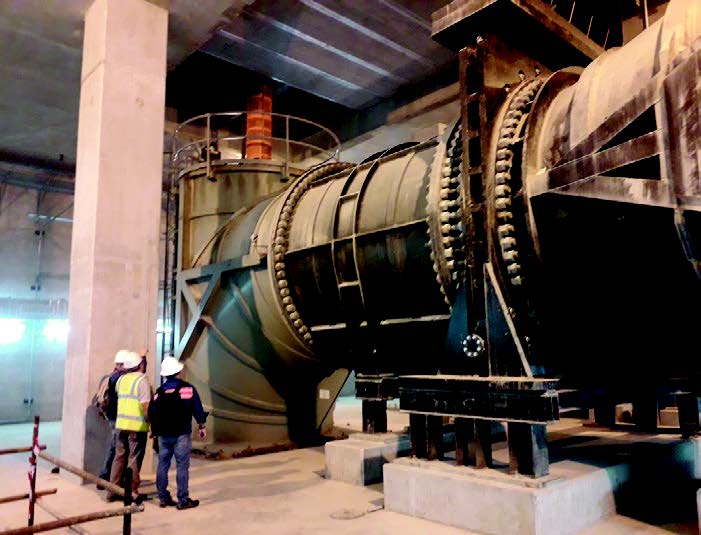
Looking Forward
Carroll had some insightful remarks regarding social governance in the valve industry, and the importance of safety: “The world that we are living in now is becoming more and more complex with specifications and certifications. There is a lot of focus around safety, and not just during disaster, but day-to-day as well. 50 years ago, people, unfortunately, were considered expendable. That is the sad truth. Nowadays we are taking more care of our employees and I think that is a good thing. The challenge, especially when you are trying to be a global supplier, has therefore become being able to meet all the different specification. There are so many different designs and design criteria to be able to sell, say, into Australia versus the United States versus even Canada, and a lot of those specifications contradict themselves and each other. I think there probably needs to be some work around global standardization, and that is going to take years and years to develop. With safety in mind and disaster mitigation in mind, I think that would be a step in the right direction.”
REFERENCE
https://www.eco-business.com/press-releases/singapores-advanced-wastewater-treatment-technologies-wins-globalrecognition/#:~:text=The%20DTSS%20uses%20deep%20tunnel,effluent%20discharged%20to%20the%20sea