Plant and personnel safety is a central focus for socially responsible and safety conscious companies. Following a series of fatal accidents across the globe, regulation now mandates certain minimum technical precautions in many industries. As a result the ability to isolate lines and ensure absolute downstream flow shut-off is essential.
By Marc Soucy, Product Applications Engineer – Armour Valve
Many different types of valves are used to isolate pipelines. However, valves can and do leak. Downstream valve leakage can occur without the knowledge of plant personnel as there is often no visual indication of failure. This scenario can at best lead to product waste or contamination; at worst to the escape of toxic substances or a potentially explosive fire hazard.
Line blinding is a process which ensures the total isolation or ‘blinding’ of the downstream flow within a pipeline. It is a common procedure in industries that store, forward, or process hazardous chemical or petrochemical substances, or where the media may become unstable or potentially dangerous during part of a process. Line blinds often complement conventional valves used for isolation, in that they guarantee absolute and positive shut-off to the downstream. Additionally, they provide a clear visual indication of their actual open or closed status. A line blind is permanently installed into a pipeline and often referred to as spectacle blinds, figure of eights, or blinding systems. They are frequently found in the petrochemical, steel, pulp & paper, maritime, and oil & refinery industries.
In the past, changing line blinds was considered an onerous, time consuming and often dangerous task. Traditional line blinding methods such as inserting metal plates with a gasket between flanges ensure safety, but are time consuming to open or close. Larger size blinds require numerous people or expensive equipment such as cranes to change.
In traditional methods, rotating the blind requires three workers – two workers to loosen the bolts and spread the line and the third to raise and rotate the heavy spectacle plate. It could take up to four hours to rotate one blind – particularly when nuts and bolts are rusted. For larger size blinds above 12”, the changing process can take between four and 12 hours by a team of up to six workers. As such, traditional line blinding techniques represent a significant time, cost, and safety factor.
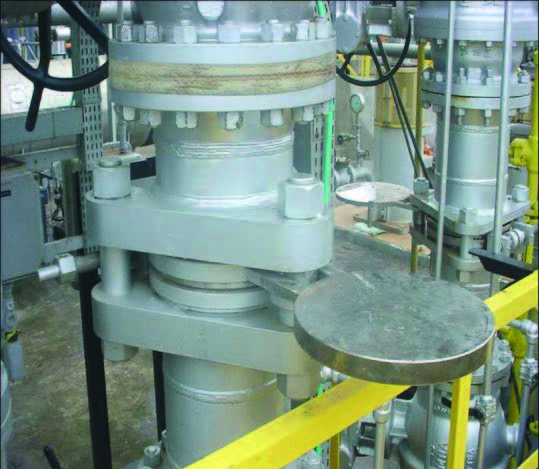
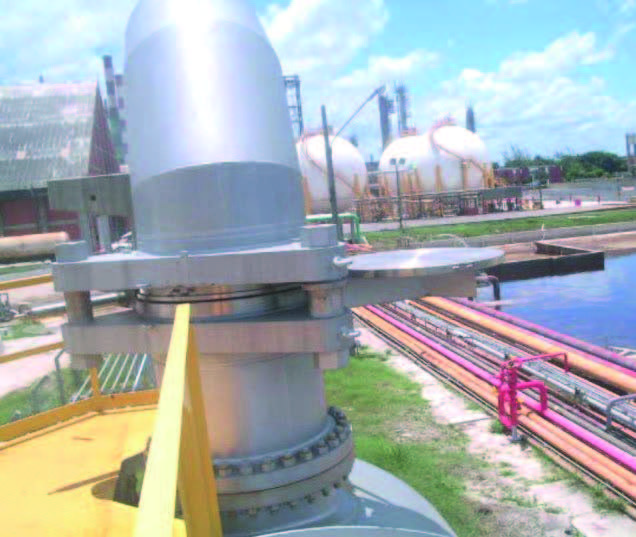
Issue & Importance
A Canadian methanol producer was using a line blocking system designed when the plant was originally built in the 1970s. At least two workers were required to spread the pipe at a flange in order to put the blocking system in place.
When the reformer tripped, which happened three times a year, it took approximately eight hours for a crew of two to four workers to isolate all six critical lines. Each hour of lost production time cost the plant roughly CAD $20,000.
The piping and welding manager knew that there had to be a better solution and approached Armour Valve for advice. Their partner SchuF offers a Cam-Set® Line Blind with advantages over traditional blocking which were presented for consideration.
Modern blind systems are designed around an internal cam system that negates the need to spread the body flanges or move the adjacent piping when the spectacle plate is changed.
This simple feature has enormous benefits, as piping movement can cause misalignment of the piping, piping and vessel damage, and physical injury to the workers moving the heavy piping. The internal cam-mechanism allows the plate to swing from open to closed position within a minute. As soon as the pipeline is drained, the cam-mechanism can be opened by turning the actuator screw (or hand wheel).
Now, the spectacle plate can be turned and positioned, and finally the cam-mechanism can be closed again by closing the hand wheel.
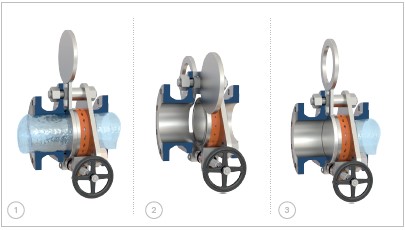
How it Works
The internal cam system is actuated via a single actuator screw which is perpendicular to the axis of the pipe. When the screw is rotated a movable inclined plane slides against a fixed inclined plane, moving the seal carrier away from the spectacle plate, thus freeing it to be moved to a new position.
Solution
After extensive research and evaluation, the piping and welding manager decided to install six line blinds on lines ranging from 1” to 12” and pressure rating from ANSI 150 to ANSI 900 class.
Unlike traditional line blinds, a single worker without the use of special tools or equipment can operate a 10” or smaller SchuF Cam-Set® Line Blind. In sizes above 10”, the line blinds are equipped with a counterweight option to facilitate quick blinding.
In addition, all of the bolts are tack welded and cannot be unintentionally removed or loosened. With no bolts to remove or loosen, the plant was able to achieve absolute positive safe shut-off of all six lines in less than 15 minutes. The overall process took approximately one hour including travel between lines.
Impact
The methanol producer’s main priority was safety, followed closely by cost savings. The blinds ensured absolute isolation. If they were to leak, it would be to atmosphere and not downstream where people are working. Fewer workers were required to isolate the lines and the plant benefitted from savings on labor hours and downtime (refer to Table 1). The facility was able to recoup its investment after the first trip of the reformer, less than one year from installation.
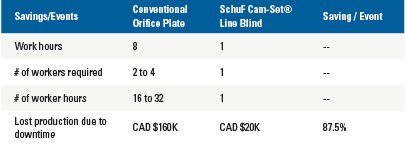