Valve World Americas recently had the pleasure of speaking with Ibrahim Gadala, Research Engineer, Petrochemicals R&D, working at NOVA Chemicals. Gadala works in the Center for Applied Research, which is the largest private research facility in Western Canada. NOVA Chemicals’ Olefins and Polyolefins business unit produces and sells ethylene, PE resins, and co-products from its two manufacturing centers, located in Alberta and Ontario, Canada. Gadala has a unique insight into the challenges and opportunities facing the petrochemical industry at this time. Gadala shared his thoughts about developments in integrity, valves, welding, corrosion modeling, failure analytics, and sustainability.
By Sara Mathov
Background and Career
Gadala has worked for years in asset integrity, and his current role at NOVA is no different. Working in petrochemical research and development, Gadala’s research focuses on materials integrity, corrosion, and reliability. Specifically, his team works to prove the viability of their olefins, ethylene producing and polyethylene plants, as well as pipeline integrity and construction. Gadala is a self-professed “big fan of failure analysis.” He also loves evidence of his hard work in the real world: “It is interesting to see when driving along the highway, that I did a pipeline assessment or an engineering assessment on one pipeline that is going under the road,” he shared.
Gadala is always thinking about risk factors and reliability when it comes to his projects, but that is not the only challenge he faces when getting a major project off the ground. For the more large-scale research and development projects, there is a lot of interaction and coordination between different stakeholders. This can become somewhat of a juggling act, since each different stakeholder naturally has a different objective. Gadala’s team has become accustomed to dealing with these challenges, and they still manage to put the research and the science first.

Welding & Valves
Gadala’s role as a R&D Engineer means that he has insights into some of the most common problems in the industry. With welding, he explains that the durability of the weld in a corrosive environment depends on a number of factors, including: the microstructure of the heat-affected zone, the constituents of the base metal, and electrolyte. “The microstructures that make up the heat-affected zone and the base metal are often quite different, which can cause several issues. Damage as a result of microstructural change is fairly common,” said Gadala. “Initially it can start as a weld with a ‘lack of fusion’ defect, which is when there is an issue in the bond between the weld and the base material. Corrosive media entering this void can lead to galvanic corrosion: when two dissimilar metals are connected and exposed to the same corrosive environment.
Valves are equally as integral to Gadala’s industry as welding. NOVA Chemicals uses many different types of valves on their projects, including generic valves, stainless steel valves, and higher-grade valves made using exotic materials. “The most common valve we use is probably a ball valve. We also have unidirectional valves and choke valves that can be very useful,” said Gadala. NOVA Chemicals does sometimes run into problems with its valves, due to the fact that their projects are very specialized and often require valves with a very specific trim and internal geometry. “One possible solution would be for engineers to be able to have free reign to say; ‘okay, I want this valve type, this design, and this material,’ and somehow the manufacturer would be able to make it. Maybe 3D printing or some other new manufacturing techniques could help us achieve this goal.”
Why Stainless Steel?
When asked why people might choose to use stainless steel over other materials, Gadala had a complex response. First and foremost, he said that stainless steel is “really transferable.” However, he also notes that stainless steel, like any metal used in the welding process, is vulnerable to corrosion and deterioration over time. There are mitigation techniques that engineers can employ, including corrosion inhibitors and anodes. More research needs to be completed in order to determine which techniques work best on stainless steels: “If we were able to finalize or be confident in our corrosion model for carbon steels, and take that one step further, we could do more accurate corrosion modeling for stainless steels.” Oxide film modeling on stainless steel is much harder to do than modeling the typically active corrosion of carbon steel.
In current projects, grades of stainless steel range from 316L to 304, sometimes going into higher grades. “There are many different factors that can cause corrosion to occur, including pitting corrosion, uniform corrosion, stress corrosion, cracking, or hydrogen embrittlement. All of these issues threaten the structural integrity of the weld. Failure analysis and modeling in my department focus on the rate of degradation over the type of degradation, since there are so many different types. Rate is more important in terms of finding concrete solutions to the problem,” explained Gadala.
One of the most common causes of corrosion in 300 series stainless steels is chlorine induced degradation. Chloride and stress combined can cause cracking, and in upstream projects, there is water with a high chloride or salt content. This causes the degradation of stainless steel through pitting and potentially cracking very quickly. On the other hand, under normal atmospheric conditions, stainless steels work pretty well. Modeling for stainless steels is challenging; Gadala explained. “What we are seeing is that in very specific environments, that are not 100% aqueous, you cannot run the electrochemical experiments. Our team runs electrochemical experiments on metals to determine the type and rate of corrosion, but these experiments do not work without water to conduct the electricity. This poses a problem for stainless steels, since often they are used in non-aqueous environments.” Overall, Gadala certainly sees the value and adaptability of stainless steels, but would like to see more research into how stainless steel degrades in specialized environments.
Failure Analysis & Corrosion Modeling
Corrosion modeling has been around for a long time, but in recent years, vast strides have been made towards improving predictions and expanding their applications. Field studies are one example; previously, observing pipelines and other machinery in the field was the only way to gauge the risk of corrosion. Now, engineers can use the finite element method and computational fluid dynamics to perform risk assessments in house rather than out in the field. “A multi-physics software includes not only the fluid physics, i.e., the fluid flow regimes, and not only the heat transfer, stress analysis, but all of it combined, and how each one of them interacts with one another,” said Gadala. “Being able to accurately model how a heat exchanger or a pressure vessel will perform would allow engineers to see where the degradation would occur and take preventative measures.”
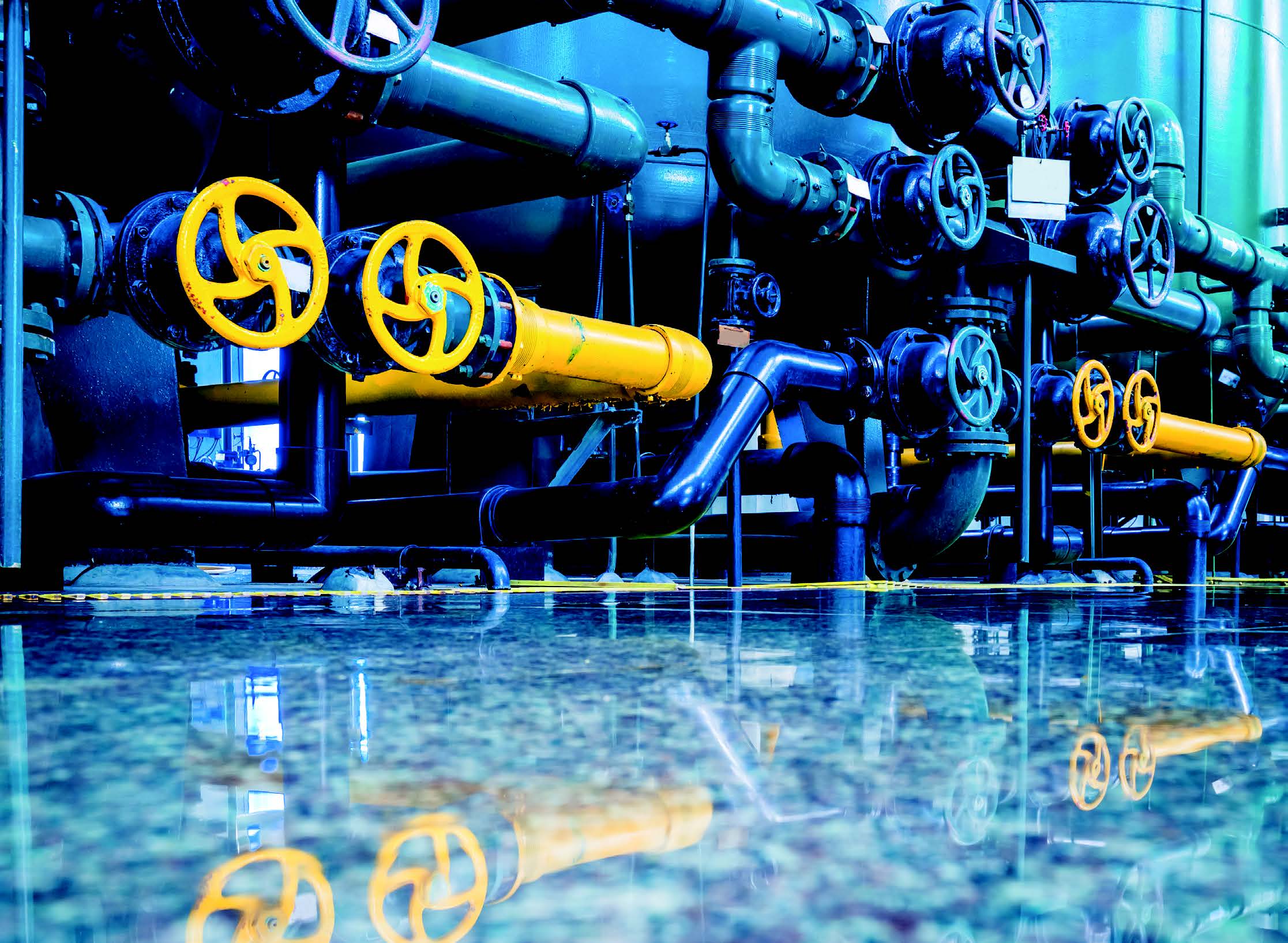
These preventative measures are key in terms of efficiency and product quality, but also in terms of cost effectiveness. Instead of doing a full inspection, inspection could be narrowed down to the areas that are at highest risk of corrosion and degradation. “In addition to modeling and failure analysis, there are some welding techniques that can be preventative in nature,” stated Gadala. “It comes down to procedures, specific techniques, and following recommended practices such as API 577. The process involves setting up a procedure that is specific to the case, having welders do test runs, and evaluating the weld quality. Ideally, this all should happen before the welding of the actual structure begins.”
Another major challenge that companies like NOVA Chemicals face is managing aging infrastructure. “A lot of the pipelines that are across the world are relatively old, and they are coming up on the end of their design life. There are also problems with documentation; back in the day, documentation was not as strict or stringent as it is now,” explained Gadala. “This makes it quite difficult for engineers to determine exactly what types of steel grade was used in the original construction of the pipeline. For new construction, materials are well documented, and radiography and ultrasonic inspections are performed on the welds to detect preservice damage.”
Sustainability: The Future of the Industry
When asked about next steps for the petrochemical industry, Gadala identified sustainability as one major goal that multiple companies are working towards. He explained that the production of ethylene, for example, involves using steam cracking to crack ethane into ethylene. “It is a very energy intensive process and uses a lot of natural gas. The industry is working towards reducing the impact of this process on the environment by decarbonizing the heating process.”
Gadala is also researching chemical recyclability. “This process would involve breaking the plastic down into its original monomers and repolymerizing it for reuse. NOVA Chemicals is in early ventures with waste collection companies as well in an attempt to improve the recyclability of materials.”
Another way to reduce waste would be to explore more cost-efficient methods and materials. Gadala is quite interested in seeing how strides in 3D printing and additive manufacturing could be applied to mechanical equipment like valves, pumps, and piping. “If 3D printing were to become the norm, it would mean that manufacturers could produce exactly the correct amount of products that companies need, rather than producing large batches of products that sometimes go to waste,” Gadala said. “Sustainability is what we all hope for. We all want to work diligently, work smarter, and eventually succeed in reducing our carbon footprint. We want to not only make products that have less impact on the environment, but also clean up the environment. Talking about this stuff is really on the front end of research and development right now. If the industry works together on these goals, we are sure to see more sustainable methods in the near future. For myself at NOVA Chemicals, and other companies, we continue to research through challenges and find new innovative solutions,” he concluded.