From the beginning, A-T Controls has earned a stand-out reputation for its engineering expertise, quality service, and delivery of manual and automated engineered valves. Its focus on providing automation products through solution-driven selling, and its dedication to manufacturing with responsive communication, has made it a globally recognized leader of valve and actuator solutions. Valve World had the pleasure of speaking with President and CEO, Brian Wright, about A-T Controls’ dedication to working on innovative and automated products for the next generation, and its remarkable solution-focused services.
By Shopia Ketheeswararajah and Justin Yule
Strong Roots
Founded in 1994, A-T Controls set out to provide end-users with automated valves, actuation, and quarter turn valve accessories. In 1997, the company started to design and manufacture its own valve line. Since then, A-T Controls has progressively added new valve products and improved previous designs to meet the needs of modernized systems.
Operating from its 122,000 sq. ft. headquarters in Cincinnati, Ohio, and its 98,000 sq. ft. facility in Stafford, Texas, the company offers efficient and convenient packages to end users in several industrial sectors. Its focus on providing problem solving and solution-oriented services for quarter turn valves has distinguished it from other suppliers as the go-to source for any valve need.
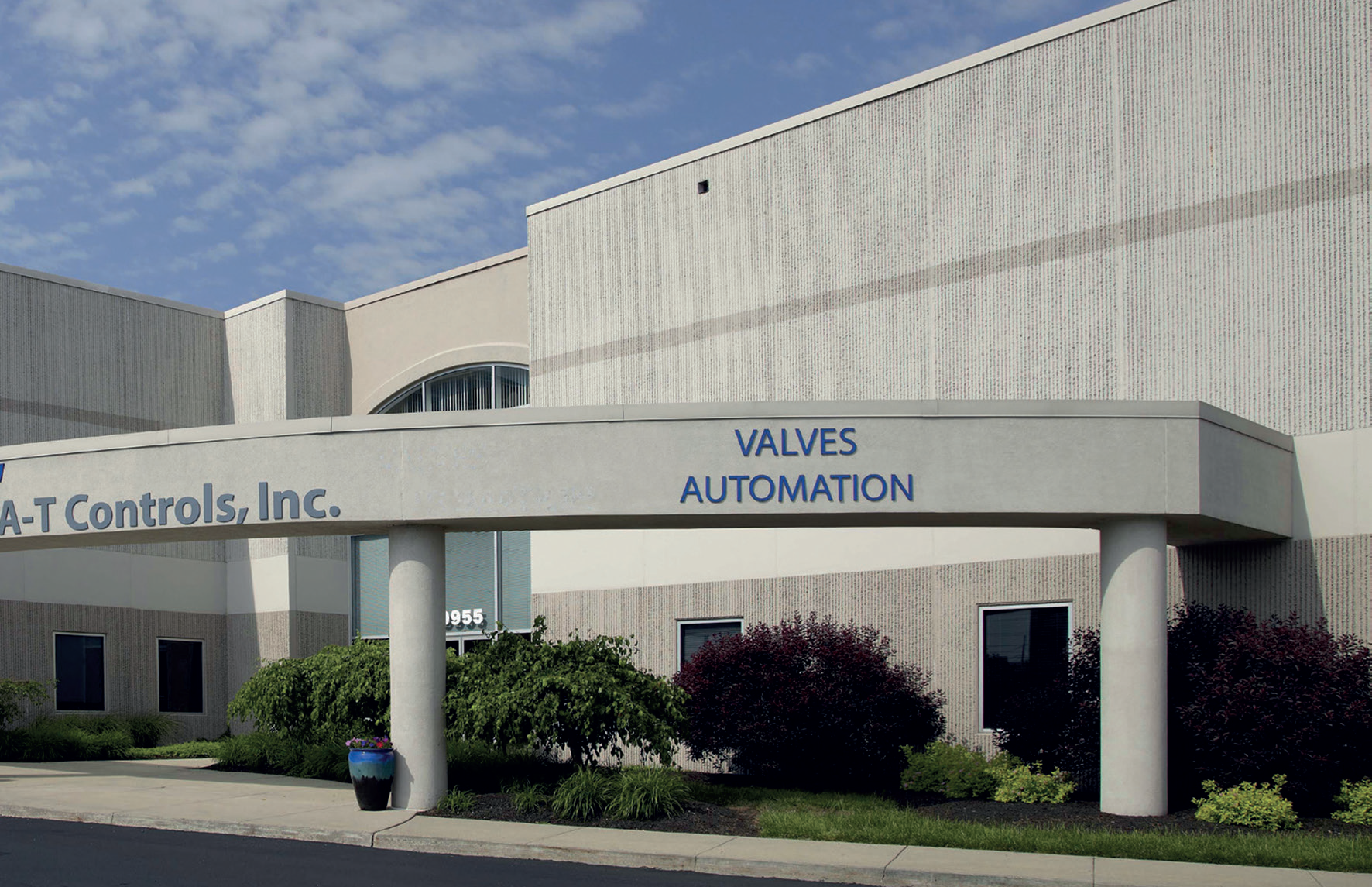
“We are a one-stop-shop,” explained Wright. “Customers can look to us for solutions about any quarter-turn application. We are not afraid of bespoke products and modification requests.” Because of its broad product range, A-T Controls can tackle a long list of markets, including oil & gas, pharmaceutical binding, power, food & beverage, water & wastewater, as well as pulp & paper industries. This versatility has provided the company greater opportunities to excel.
“I think our longevity can be attributed to the immense breadth of products we offer, our loyalty to our distribution network, and the consistency in our products. We are second-to-none in terms of our offerings in the quarter turn valve and automation business,” he continued.
A Vast Range of Products
While its product portfolios include flanged valves, three-ways, and high-performance butterfly valves, the company’s primary focus has always been on automation and quarter turn valve solutions.
A-T Controls offers complete automation services for quarter turn valves through its Triac brand of actuators and accessories; these are well-known within the industry for quality. It also manufactures precision mounting kits to automate other manufacturers’ ball, butterfly, and plug valves. “In the last couple of years, for example, we have introduced a spring return electric actuator, with different pressures and designs of our trunnion ball valve offering. This has been steadily gaining market share,” stated Wright.

Its vast range of products is complemented by a full accessory line that includes solenoid valves, filter regulators, limit switches, proximity sensors, positioners, manual overrides, and customer valve mounting hardware. “All of our assemblies are calibrated, tested, and properly packaged to ensure that the user receives the exact product required for their application,” he noted. “Every actuator and actuated assembly is provided with a serial number upon completion, which allows for easy traceability.”
As specific distribution requirements are one of the many aspects that propel innovation at A-T Controls, its engineers and distribution team are diligent in gathering information that targets the market’s current pain points. Using this information, innovation can be conceived from the ground up, or added as a variation to an existing product.
Total Service
To modernize its systems and processes, and exceed its customers’ expectations, A-T Controls regularly revaluates its products and distribution systems. “We are constantly asking our distributors what they want to see next. This can be in terms of product features, internal and external communications, integration, as well as services and solution-oriented improvements or adjustments,” said Wright. The company takes pride in receiving and implementing customer feedback to create holistic solution-oriented answers. “We have a team of engineers that respond to specific customer issues, because not every application is cookie-cutter. People come to us for solutions for abrasion, high-pressure, material compatibility, or end connections that need to be customized,” explained Wright. “We are equipped to react quickly and efficiently to help when customers require application assistance, and we know that if we can solve a client’s difficult problems, they will know they can also come to us with the easy ones.”
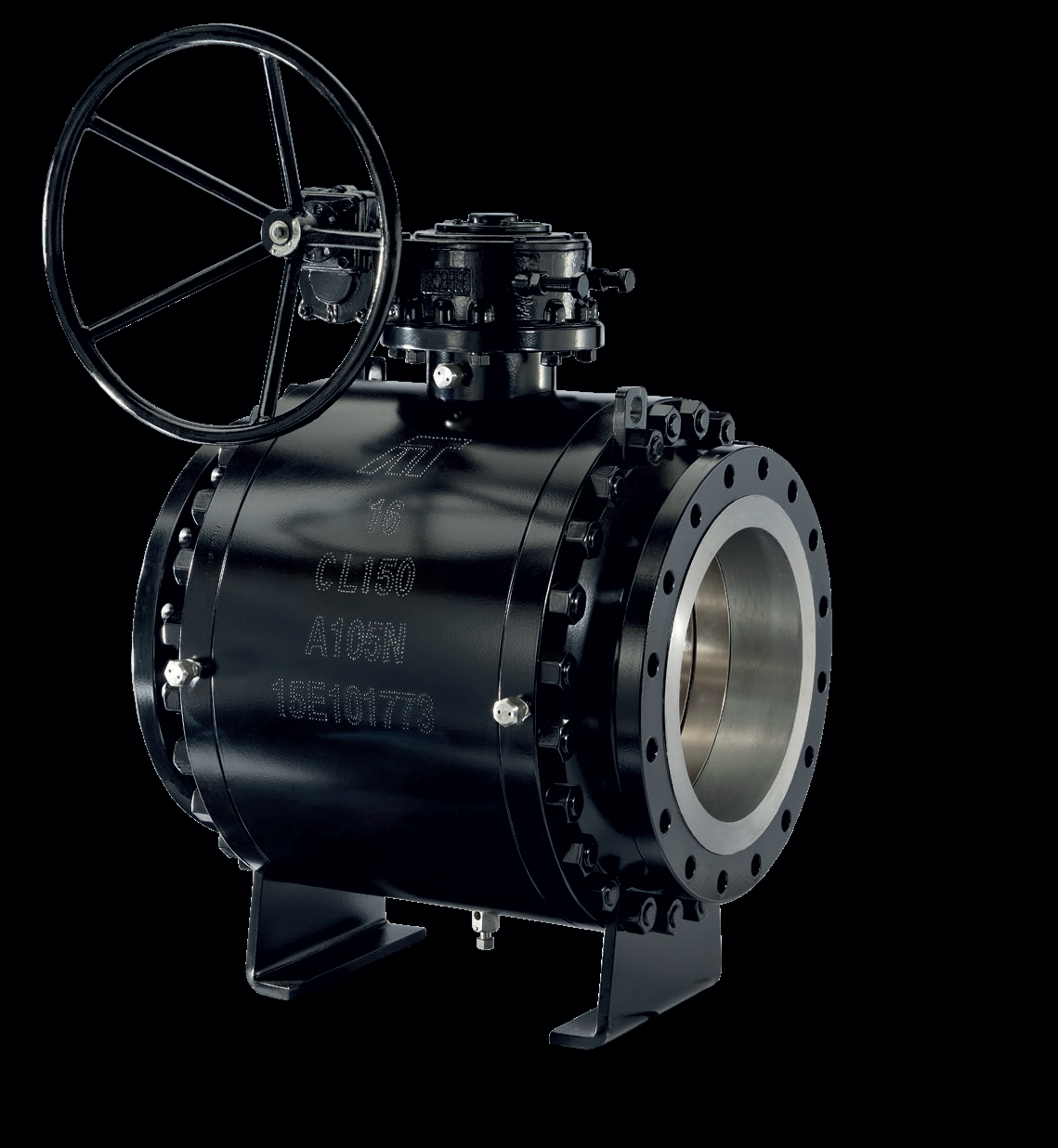
Upon acquiring a small company from Houston, Texas, A-T Controls was able to further expand its offerings to include an innovative controller, the Mighty Controller, which operates the company’s system group. The Mighty Controller is an innovative computing device designed for OEMs and system integrators who want to modernize existing approaches to local system controls. “We sell manual and automated quarter turn valves, and with applications like the Mighty Controller, we also offer a complete system to our customers. The Mighty Controller provides information such as temperature, torque signatures, and vibration measurements giving the end user useable data that can be used to mitigate the risks of failures,” said Wright. “Ultimately it can optimize the actuator and valve positions to increase efficient flow through the wellhead.”
A-T Controls has built trust with industrywide clients, applying its strengths, and rallying its resources towards unwavering effort and creative solutions.
Leading the Way
A-T Controls believes there are two kinds of company cultures: leading or following. “We are dedicated to being the leader – we do not want to fall behind and follow other companies as technology progresses. We want to be known for our high quality, high standards, and dedication to solution focused service,” Wright commented.
To ensure it provides its customers with the best products, the company sends all its valves to an independent third party for testing to ensure nothing is overlooked. As a result, the distribution department is heavily involved in the production side of the business. “By conducting everything from ISO 9000 to API audits, the team continues to ensure production and operations are following the comprehensive quality mandates.”
The company’s commitment to being available, responsive, and innovative, along with a broad offering of quality products, has allowed it to truly put the customer first. “Our response to the needs of distribution, customers, and end users is paramount,” stated Wright. “From the moment a customer picks up the phone for their inquiry, A-T Controls guarantees that the client is speaking to a knowledgeable representative.”
Its highly experienced engineering and sales staff, coupled with its extensive inventory, therefore provide the customer with solutions needed to fulfill most valve and actuator requirements, while offering a competitive price and fast turnaround. “If someone comes to us with an application, wanting to know whether they need to vent the ball, or if they have an inquiry about materials and flow, we have the expertise to guide them towards applications that best fit their needs. We want to make sure that we provide the best outcome to our clients, as it is important to stay transparent and build trust,” said Wright. “A-T Controls’ responsiveness is driven towards getting the client’s question answered, not just a short answer, but the right answer.”
Emissions and Sustainability
Further, A-T Controls’ customer-centric approach means it has been attuned to the concerns clients have had about fugitive emissions. By focusing on total service, A-T Controls’ has become a leader in sustainability. Indeed, the decision to upgrade its packing systems and obtain certifications such as ISO 15848-2 arose from customer demands. A-T Controls started designing its valves over 20 years ago with a unique 3-packing system, using a pyramidal stem seal. The initial sealing of the stem to the packing is through a pyramid-type design, with Teflon. The secondary seal is an O-ring, and it seals both the stem side and the body side of the valve. The tertiary seal is the live loaded packing. With new standards came the requirement for fugitive emissions bonnets, a double set of packing, bellow seals, and much more for the rotary valve market. These changes and investments allow the company to provide preventive safety measures for the products that are being distributed, continuing to keep the best possible solutions for the end user and the industry.
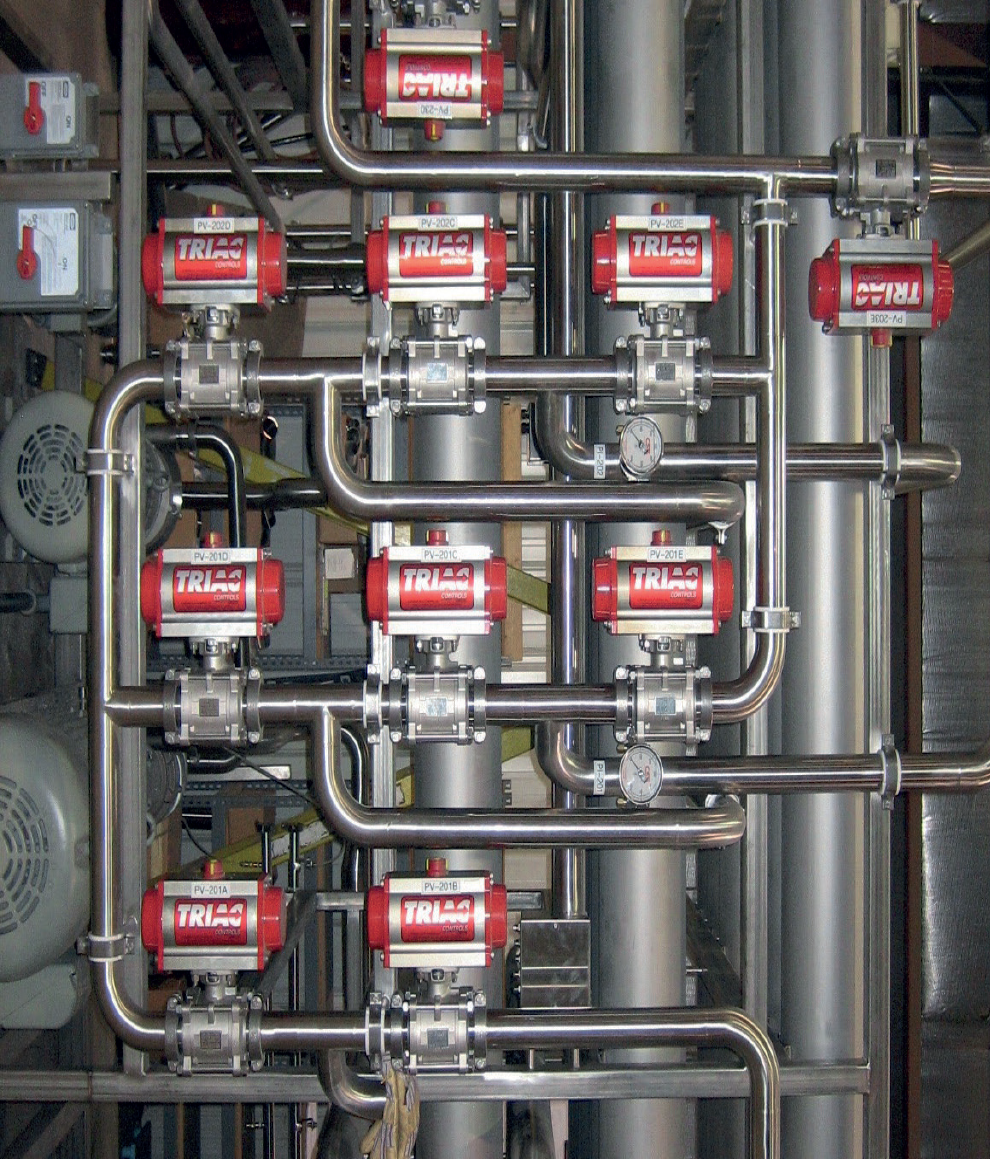
ISO 15848-2 is a standard that evaluates how well valve seals prevent fugitive emissions. The standard tests valve stem seals and body seals for leakage (measured in concentration or a leak rate) and categorizes valves into different ‘tightness classes’ based on how well a valve performed through a series of tests (endurance classes) at different temperatures and pressures (temperature classes). These classes are determined based on the test fluid used, the number of cycles the valve undergoes, the temperature the test, and how a valve is identified (isolating or control valve). Isolating valves can be tested to 2,500 cycles, while control valves can be tested to 100,000 cycles. Methane and Helium are both allowed as test fluids, and the standard does not allow for any correlations between them. ISO 15848-2 testing uses helium for production testing of valves that have already passed ISO 15848-1 testing. The allowable leakage rate of stem seals is also characterized in tightness classes, and the allowable leakage from body seals. A-T Controls can provide ISO 15848-2 testing at their Cincinnati facility. All valves are identified with a tag that indicates the unique test for each valve.
What Does the Future Hold for A-T Controls?
A-T Controls is excited for what is to come next within the valve market. It will continue to grow with its customers and introduce new products and automations that will broaden its offerings even further. While the supply chain issues of the COVID- 19 years created obstacles, the company recognized that it needed to continue to adapt and innovate. “To account for those challenges, we took proactive measures, such as getting ahead of blanket orders, raw materials, and increasing foundry capacities. Although it was not a simple process, A-T Controls prides itself on its ability to successfully manage the troubleshoot processes,” commented Wright.
“We will continue to see interest in connectivity and monitoring for processes. The systems group and some of the product features speak to this,” said Wright. Data driven initiatives will continue to be a larger part of what the company offers. “Our success is determined by the quality of people who work diligently and honestly in the company. Whether it is our sales department, engineering, production, or quality assurance, all the people at A-T Controls that touch the process, care about the customer’s needs,” he concluded.